restauration moteur ancien opel des années 60
+2
Daniel
Eric L
6 participants
oocb :: Partie Publique :: L'atelier
Page 7 sur 8
Page 7 sur 8 • 1, 2, 3, 4, 5, 6, 7, 8
Re: restauration moteur ancien opel des années 60
Direction et réglage des roues avant Kapitän P 2,6 L
Par suite de la nouvelle direction des pneus (7,00-14), les distances du sol pour l’établissement du plan de mesure de la voiture pour le réglage de l’essieu avant, se sont modifiées.
A – Distance à l’avant : Mesurés depuis le point le plus bas du longeron du châssis avant jusqu’au sol 334,5 mm.
B – Distance à l’arrière : Mesurée depuis le point le plus bas du longeron du châssis arrière jusqu’au sol 339 mm.
Le réglage des roues avant ne doit intervenir que dans ce plan de mesure.
Distance entre l’extrémité antérieure du longeron et la surface plane du sol.
Distance entre l’extrémité postérieure du longeron et la surface plane du sol.
Données des réglages : Carrossage ° + 30’
0 - 15’
Chasse 1°30’ +
- 30’
Pincement 1 - 3 mm
Important : Les données de réglage qui précèdent doivent aussi être prévues rétroactivement pour les modèles révolus Kapitän P et les réglages de roues avant y relatifs doivent être opérés ainsi.
On maintiendra cependant les anciennes indications concernant les distances du sol pour le plan de mesure de la voiture.
La pression de pneu pour le réglage est de 1,6 atm, à l’avant, et de 1,7 atm à l’arrière (pleine charge)
LD
Par suite de la nouvelle direction des pneus (7,00-14), les distances du sol pour l’établissement du plan de mesure de la voiture pour le réglage de l’essieu avant, se sont modifiées.
A – Distance à l’avant : Mesurés depuis le point le plus bas du longeron du châssis avant jusqu’au sol 334,5 mm.
B – Distance à l’arrière : Mesurée depuis le point le plus bas du longeron du châssis arrière jusqu’au sol 339 mm.
Le réglage des roues avant ne doit intervenir que dans ce plan de mesure.
Distance entre l’extrémité antérieure du longeron et la surface plane du sol.
Distance entre l’extrémité postérieure du longeron et la surface plane du sol.
Données des réglages : Carrossage ° + 30’
0 - 15’
Chasse 1°30’ +
- 30’
Pincement 1 - 3 mm
Important : Les données de réglage qui précèdent doivent aussi être prévues rétroactivement pour les modèles révolus Kapitän P et les réglages de roues avant y relatifs doivent être opérés ainsi.
On maintiendra cependant les anciennes indications concernant les distances du sol pour le plan de mesure de la voiture.
La pression de pneu pour le réglage est de 1,6 atm, à l’avant, et de 1,7 atm à l’arrière (pleine charge)
LD
Daniel- Messages : 544
Date d'inscription : 22/04/2012
Age : 81
Localisation : Paris Ouest
Opeldel aime ce message
Re: restauration moteur ancien opel des années 60

lucdm- Admin
- Messages : 3261
Date d'inscription : 20/04/2012
Age : 68
Localisation : Natoye / Président OOCB
Re: restauration moteur ancien opel des années 60
Couples de serrage Olympia –types 1958
Désignation Couple
m/kg
(cm/kg)
Suspension de roues avant
Axe de triangle inférieur au moins 14
Axe de triangle supérieur au moins 8
Douille filetée dans le triangle inférieur, à l’intérieur 19 - 22
avec pièce à pré charge engagée (valeur de contrôle ) 11 - 15
Douille filetée dans le triangle inférieur, à l’extérieur
avec pièce à pré charge engagée 8 - 15
sans pièce à pré charge (valeur de contrôle) 6 - 8
Fixation, rotule au triangle supérieur 2,2 - 2,5
Fixation rotule à la fusée d’essieu 3 - 3,4
Fixation amortisseur au triangle inférieur 2,2 - 2,5
Contre écrou, amortisseur 0,2 - 0,3
Ecrous avant au châssis avant 5,2 - 5,8
Pont arrière
Ecrous, étriers de ressort (Olympia Rekord et Olympia ) 1,8 - 2,2
Ecrous, étriers de ressort (Caravan et Fourgonnette) 3,0 - 3,4
Contre écrous pour étrier de ressort (Olympia Rekord, Olympia,
Caravan et Fourgonnette) 3,8 - 4,2
Ecrous, pendants de ressorts 4,2 - 4,7
Ecrous, ressorts arrière à l’avant 2,8 - 3,1
Boulons, couronne 5,2 - 5,8
Boulons, chapeaux de palier au carter de pont arrière 4,2 - 4,7
Boulons, couvercle au carter arrière 0,9 - 1,1
Contre écrous, amortisseurs en haut 0,2 - 0,3
Ecrous, amortisseurs en bas 4,2 - 4,7
Fixation, arbre de cardan au flasque 2,3 - 2,5
Freins
Fixation, cylindre de frein de roue au flasque de frein 0,3 - 0,35
Fixation, flasque de frein à la fusée et au levier de direction 6,5 - 7,0
Ecrous à raccord pour toutes les conduites de frein 1,3 - 1,5
Moteur et embrayage
Ecrous, bielles 6,5 - 7,0
Boulons, chapeaux de palier de vilebrequin 9,7 - 11,1
Boulons, chevalet de pompe à huile au bloc - cylindre 4,2 - 4,7
Fixation, pompe à huile à chevalet de pompe à huile 2,2 - 2,5
Boulons, volant au vilebrequin 5,2 - 5,8
Boulons, carter d’embrayage au bloc cylindre 7,0 - 7,8
Suspension avant de moteur au bloc cylindre 3,2 - 3,6
Suspension avant du moteur au longeron du châssis avant 2,2 - 2,5
Suspension avant du moteur (bloc amortisseur au support) 2,2 - 2,5
Fixation, suspension arrière de moteur à la transmission 2,1 - 2,4
Fixation, suspension arrière de moteur à la traverse du moteur 2,2 - 2,5
Boulons, fixation de la culasse 9,0 - 10,0
Boulons, assemblage tubulure d’admission et collecteur
d’échappement au bloc cylindre 4,2 - 4,7
Transmission
Fixation, transmission au carter d’embrayage 4,2 - 4,7
Fixation, prolonger de carter de transmission au carter
de transmission 2,2 - 2,3
Vis d’arrêt, levier intermédiaire d’engagement
à l’axe du levier de commande 1,8 - 2,0
Installation du carburant et conduite d’échappement
Vis à tôle, réservoir à carburant à l’infrastructure 0,8 - 1,1
Boulons, tuyau au collecteur d’échappement 2,2 - 2,7
Boulons, étrier – suspension du pot d’échappement 1,0 - 1,3
Direction
Boulons, couvercle au boîtier de direction 3,0 - 3,4
Fixation boîtier de direction au longeron 4,2 - 4,7
Ecrou bras de Pitman 15 - 17
Ecrou crénelé, levier intermédiaire de direction au support du dit 6 - 9
Tous les écrous rotule timonerie de direction 3,7 - 4,1
Ecrous pour timonerie de direction – colliers de serrage 2,2 - 2,5
Vis lenticulaire, collier à écrou de direction (55 - 65)
Ecrou, volant de direction 1,5 - 1,9
Fixation, support de tuyau de sélection au boîtier 0,30 - 0,35
Roues
Ecrous de roue 8 – 10
Equipement électrique
Ecrous, cadre de batterie au support de batterie ( 16 -18 )
Refroidissement
Vis à tôle, fixation du radiateur 0,9 -1,1
Valeur couple en cm/kg (… ….)
Exemple : 7,0 nm = 71,3801…. Kg/cm
LD Historien de l’OOCB
Désignation Couple
m/kg
(cm/kg)
Suspension de roues avant
Axe de triangle inférieur au moins 14
Axe de triangle supérieur au moins 8
Douille filetée dans le triangle inférieur, à l’intérieur 19 - 22
avec pièce à pré charge engagée (valeur de contrôle ) 11 - 15
Douille filetée dans le triangle inférieur, à l’extérieur
avec pièce à pré charge engagée 8 - 15
sans pièce à pré charge (valeur de contrôle) 6 - 8
Fixation, rotule au triangle supérieur 2,2 - 2,5
Fixation rotule à la fusée d’essieu 3 - 3,4
Fixation amortisseur au triangle inférieur 2,2 - 2,5
Contre écrou, amortisseur 0,2 - 0,3
Ecrous avant au châssis avant 5,2 - 5,8
Pont arrière
Ecrous, étriers de ressort (Olympia Rekord et Olympia ) 1,8 - 2,2
Ecrous, étriers de ressort (Caravan et Fourgonnette) 3,0 - 3,4
Contre écrous pour étrier de ressort (Olympia Rekord, Olympia,
Caravan et Fourgonnette) 3,8 - 4,2
Ecrous, pendants de ressorts 4,2 - 4,7
Ecrous, ressorts arrière à l’avant 2,8 - 3,1
Boulons, couronne 5,2 - 5,8
Boulons, chapeaux de palier au carter de pont arrière 4,2 - 4,7
Boulons, couvercle au carter arrière 0,9 - 1,1
Contre écrous, amortisseurs en haut 0,2 - 0,3
Ecrous, amortisseurs en bas 4,2 - 4,7
Fixation, arbre de cardan au flasque 2,3 - 2,5
Freins
Fixation, cylindre de frein de roue au flasque de frein 0,3 - 0,35
Fixation, flasque de frein à la fusée et au levier de direction 6,5 - 7,0
Ecrous à raccord pour toutes les conduites de frein 1,3 - 1,5
Moteur et embrayage
Ecrous, bielles 6,5 - 7,0
Boulons, chapeaux de palier de vilebrequin 9,7 - 11,1
Boulons, chevalet de pompe à huile au bloc - cylindre 4,2 - 4,7
Fixation, pompe à huile à chevalet de pompe à huile 2,2 - 2,5
Boulons, volant au vilebrequin 5,2 - 5,8
Boulons, carter d’embrayage au bloc cylindre 7,0 - 7,8
Suspension avant de moteur au bloc cylindre 3,2 - 3,6
Suspension avant du moteur au longeron du châssis avant 2,2 - 2,5
Suspension avant du moteur (bloc amortisseur au support) 2,2 - 2,5
Fixation, suspension arrière de moteur à la transmission 2,1 - 2,4
Fixation, suspension arrière de moteur à la traverse du moteur 2,2 - 2,5
Boulons, fixation de la culasse 9,0 - 10,0
Boulons, assemblage tubulure d’admission et collecteur
d’échappement au bloc cylindre 4,2 - 4,7
Transmission
Fixation, transmission au carter d’embrayage 4,2 - 4,7
Fixation, prolonger de carter de transmission au carter
de transmission 2,2 - 2,3
Vis d’arrêt, levier intermédiaire d’engagement
à l’axe du levier de commande 1,8 - 2,0
Installation du carburant et conduite d’échappement
Vis à tôle, réservoir à carburant à l’infrastructure 0,8 - 1,1
Boulons, tuyau au collecteur d’échappement 2,2 - 2,7
Boulons, étrier – suspension du pot d’échappement 1,0 - 1,3
Direction
Boulons, couvercle au boîtier de direction 3,0 - 3,4
Fixation boîtier de direction au longeron 4,2 - 4,7
Ecrou bras de Pitman 15 - 17
Ecrou crénelé, levier intermédiaire de direction au support du dit 6 - 9
Tous les écrous rotule timonerie de direction 3,7 - 4,1
Ecrous pour timonerie de direction – colliers de serrage 2,2 - 2,5
Vis lenticulaire, collier à écrou de direction (55 - 65)
Ecrou, volant de direction 1,5 - 1,9
Fixation, support de tuyau de sélection au boîtier 0,30 - 0,35
Roues
Ecrous de roue 8 – 10
Equipement électrique
Ecrous, cadre de batterie au support de batterie ( 16 -18 )
Refroidissement
Vis à tôle, fixation du radiateur 0,9 -1,1
Valeur couple en cm/kg (… ….)
Exemple : 7,0 nm = 71,3801…. Kg/cm
LD Historien de l’OOCB
Daniel- Messages : 544
Date d'inscription : 22/04/2012
Age : 81
Localisation : Paris Ouest
Opeldel aime ce message
Re: restauration moteur ancien opel des années 60
Réglage de la télécommande de transmission –
Kapitän P avec 2,5L et 2,6L
Un réglage défectueux de la télécommande de transmission du produit au levier de commande au volant des bruits de cliquetis pendant la marche, lesquels peuvent être éliminés par l’application des instructions ci-après :
Réglage du chemin d’engagement
Amener le levier de commande au volant en position de 2e puis de 3e vitesse. Ce faisant, contrôler en continuant par un mouvement élastique du levier au-delà de chacune des positions de vitesse jusqu’à la butée finale, si la distance ‘A’ est la même pour les 2 vitesses engagées. Si tel n’est pas le cas, desserrer les 2 écrous à l’extrémité supérieure de la tringle de liaison et augmenter, avec un écrou, la longueur de la tringle, jusqu’au moment où la distance ‘A’ du chemin du levier de commande au volant est la même en engageant la 2e et la 3e vitesse.
Avant de serrer et de bloquer les écrous, il faut s’assurer que toutes les vitesses se laissent engager librement, sans crocher ni serrer. Graisser le levier de commande en forme de faucille à son endroit coulissant sur le levier d’intervention, avec de la graisse graphitée colloïdale M 48 ( Z-8277)
Contrôler en outre si les pièces d’isolation de bruits - anneaux en vulkollan ( polyuréthane), pièces de rechange N° 7 62 275, et rondelles, pièces de rechange N° N-35214 se trouvant déjà au-dessus et au bas de la pièce de réglage de la tringle de liaison. Sinon, monter ces pièces à cette occasion, en employant en même temps un espaceur neuf long de 28 mm, N° de pièces de rechange 7 62 130 dont la surface extérieure – surface coulissante dans la pièce de réglage doit également être graissée avec de la graisse graphitée colloïdale.
Réglage du chemin de sélection :
Amener le levier de commande au volant au point mort. Contrôler si la distance de commande depuis le volant en direction de ‘B’ vers les pédales se laisse agrandir par une légère pression du pouce, avec élasticité de 10 mm jusqu’au moment où un arrêt définitif contre du métal intervient.
Si, en revanche, ce contrôle fait constater d’une manière nettement sensible que le levier de commande heurte immédiatement le métal, c’est-à-dire que la distance est inférieure à celle précitée, il faut procéder à un nouveau réglage à l’extrémité supérieure de la tige d’inversion en desserrant les 2 écrous et en modifiant en conséquence la longueur de la tige.
LD
Kapitän P avec 2,5L et 2,6L
Un réglage défectueux de la télécommande de transmission du produit au levier de commande au volant des bruits de cliquetis pendant la marche, lesquels peuvent être éliminés par l’application des instructions ci-après :
Réglage du chemin d’engagement
Amener le levier de commande au volant en position de 2e puis de 3e vitesse. Ce faisant, contrôler en continuant par un mouvement élastique du levier au-delà de chacune des positions de vitesse jusqu’à la butée finale, si la distance ‘A’ est la même pour les 2 vitesses engagées. Si tel n’est pas le cas, desserrer les 2 écrous à l’extrémité supérieure de la tringle de liaison et augmenter, avec un écrou, la longueur de la tringle, jusqu’au moment où la distance ‘A’ du chemin du levier de commande au volant est la même en engageant la 2e et la 3e vitesse.
Avant de serrer et de bloquer les écrous, il faut s’assurer que toutes les vitesses se laissent engager librement, sans crocher ni serrer. Graisser le levier de commande en forme de faucille à son endroit coulissant sur le levier d’intervention, avec de la graisse graphitée colloïdale M 48 ( Z-8277)
Contrôler en outre si les pièces d’isolation de bruits - anneaux en vulkollan ( polyuréthane), pièces de rechange N° 7 62 275, et rondelles, pièces de rechange N° N-35214 se trouvant déjà au-dessus et au bas de la pièce de réglage de la tringle de liaison. Sinon, monter ces pièces à cette occasion, en employant en même temps un espaceur neuf long de 28 mm, N° de pièces de rechange 7 62 130 dont la surface extérieure – surface coulissante dans la pièce de réglage doit également être graissée avec de la graisse graphitée colloïdale.
Réglage du chemin de sélection :
Amener le levier de commande au volant au point mort. Contrôler si la distance de commande depuis le volant en direction de ‘B’ vers les pédales se laisse agrandir par une légère pression du pouce, avec élasticité de 10 mm jusqu’au moment où un arrêt définitif contre du métal intervient.
Si, en revanche, ce contrôle fait constater d’une manière nettement sensible que le levier de commande heurte immédiatement le métal, c’est-à-dire que la distance est inférieure à celle précitée, il faut procéder à un nouveau réglage à l’extrémité supérieure de la tige d’inversion en desserrant les 2 écrous et en modifiant en conséquence la longueur de la tige.
LD
Daniel- Messages : 544
Date d'inscription : 22/04/2012
Age : 81
Localisation : Paris Ouest
Opeldel aime ce message
Re: restauration moteur ancien opel des années 60
Direction Kapitän P dès 1958-
Dépose et pose de la direction
Quand toute la direction doit être déposée, il faut déposer le mécanisme de direction et l’ensemble du fourreau de la colonne de direction l’un après l’autre et non simultanément.
Ces deux parties doivent être séparées l’une de l’autre par la séparation de l’accouplement par disques d’acier. Il est dès lors possible de déposer et de poser selon les besoins, soit l’une soit l’autre de ces unités. Avant de déposer le mécanisme de direction ou l’ensemble du fourreau de la colonne de direction, il importe de marquer la position du flasque du mécanisme de direction par rapport au boîtier. Amener à cet effet les roues avant en position droite (point dur).
Dépose et pose du mécanisme de direction
Dévisser le flasque du mécanisme de direction de l’accouplement par disque d’acier. Les disques restent fixées au flasque du fourreau.
Pour arracher le bras de pitman, il faut dévisser le tuyau du pot d’échappement et le glisser vers le bas (pour Kap. 58/59 seulement)
Pour la pose, visser d’abord le mécanisme de direction au longeron du châssis avant ( couple 6- 6,5 mkg), puis en seconde ligne seulement à l’encastrement de roue. L’écrou intérieur de l’encastrement doit être réglé de manière qu’il n’en résulte aucune tension du mécanisme de direction. Visser ensuite l’écrou extérieur et serrer à raison de 6- 6,5 mkg.
Introduire les vis du flasque du mécanisme de direction dans l’accouplement par disques d’acier de manière que les tenons cylindriques des têtes de vis s’engagent dans les évidements correspondants du flasque du fourreau de la colonne de direction.
Intercaler au-dessus, de même qu’en dessous des disques d’acier une ronde arrondie aux arêtes (N° de pièces 904 802)
Désassemblage et assemblage du mécanisme de direction
Arracher le flasque du mécanisme de direction de la vis de direction avec la traverse S-1033 et l’emploi de 2 vis appropriées. Le désassemblage, la révision et l’assemblage du mécanisme de direction se fait en principe comme pour les modèles d’Olympia P et avec les mêmes outils.
Le flasque de mécanisme doit être - l’écrou de direction se trouvant en position médiane (point dur) – passé sur la vis de direction de manière qu’il (le flasque) soit orienté perpendiculairement par rapport à la marque en forme d’encoche pratiquée sur le coté frontal de la vis de direction. La moitié du flasque portant la marque en forme de point doit être dirigée vers le haut.
Lorsque la direction est complètement montée, que les roues avant sont en position droite et que le flasque du mécanisme de direction est perpendiculaire (la marque (point) vers le haut) , les rayons du volant doivent être orientés obliquement vers le bas.
Serrer la vis du flasque du mécanisme de direction avec un couple de 2,2 – 2,5 mkg Contre tenir le flasque, la direction ne doit pas être tournée en position extrême !
L’accouplement par disques d’acier comporte 3 disques, ainsi que le flasque de direction et le flasque du fourreau de la colonne de direction. Les disques d’acier sont fixés au flasque du fourreau par deux boulons six pans normaux et au flasque du mécanisme de direction par deux boulons spéciales (avec tenon cylindrique). Ces tenons doivent s’engager dans les évidements correspondants du flasque du fourreau de la colonne de direction. Pour éviter des pressions d’arêtes, des rondelles aux arêtes arrondies sont insérées sous toutes les vis. Visser l’accouplement à disques d’acier de manière que les flasques soient décalés de 90°.
Dépose et pose du fourreau de la colonne de direction
Dévisser le flasque du mécanisme de direction de l’accouplement à disques d’acier. Les disques d’acier restent donc fixés au flasque du fourreau. Détacher la timonerie de sélection et la pédale d’embrayage. Puis dévisser la fixation du fourreau au tableau de bord. Enlever le couvercle de fermeture du tablier et sortir le fourreau de la colonne de direction par l’intérieur de la voiture.
Au montage, visser d’abord d’une manière encore amovible, l’assemblage fourreau de la colonne de direction au tableau de bord puis visser à fond le flasque du fourreau à l’accouplement du disque acier.
Attention à la position médiane de la direction. Puis fixer définitivement le fourreau au tableau de bord. Veiller à une bonne étanchéité du couvercle de fermeture du tablier.
Désassemblage et assemblage du fourreau de la colonne de direction
1- Arracher le volant avec S-1033 comme dans le type Olympia P. Enlever comme jusqu’ici le levier de commande à main de la transmission.
Les vis à tôle du tuyau de revêtement de l’interrupteur de clignoteur se trouvent à l’intérieur de ce tuyau dessous l’interrupteur de clignoteur. Le tuyau de revêtement peut être enlevé après dévissage du levier de commande de clignoteur.
2- Retirer vers le haut le groupe de câbles et le câble de la serrure du volant. Pousser les câbles depuis le bas.
3- Dévisser les 2 vis à tête noyée de la cage à roulement supérieure du fourreau de la colonne de direction. Avec ces 2 vis, la serrure du volant est également fixée à la cage de roulement.
4- Dévisser le boulon fileté 6 pans et retirer la cage à roulement du fourreau.
5- Extraire en bas le flasque du fourreau à l’aide d’un extracteur.
6- Après dévissage de la bielle de liaison au bas du tuyau de sélection et du levier d’inversion avec support du fourreau, dévisser du fourreau encore deux autres boulons six pans de la cage à roulement inférieure. Attention au ressort de pression. Le tuyau de sélection est guidé dans la cage à roulement inférieure.
Au montage, monter les 2 anneaux en feutre bien graissés, décalés de 180° l’un par rapport à l’autre. Cas échéant, s’aider d’un tournevis afin de bien engager ces anneaux entre les empreintes du fourreau de la colonne. Le roulement inférieur d’arbre de direction est encastré et n’a pas besoin d’entretien. Pour changer ce roulement, l’extraire en frappant de légers coups et avec précaution tout autour de sa circonférence.
Introduire le roulement neuf prudemment par pression.
Le roulement supérieur d’arbre de direction doit être extrait et introduit par pression au moyen d’un bout de tuyau approprié.
Lors de la mise en place du flasque du fourreau de la colonne de direction sur l’arbre de direction, les évidements pratiqués dans la bague d’arrêt de la serrure du volant doivent être décalés de 90° par rapport à ceux du flasque du fourreau. Par ce moyen, la serrure bloque en position droite des roues avant.
Avant de placer l’appui du levier de commande à main, passer 2 tubes en matière synthétique de bas en haut depuis le trou des groupes de câbles dans le fourreau de la colonne, jusqu’au moment où ces 2 tuyaux flexibles dépassent encore d’environ 10 cm le trou latéral du fourreau. Le diamètre de ces flexibles est de 10 mm, soit 12 mm, longueur minimum 1 m.
Introduire les tubes flexibles sortant du trou latéral au haut du fourreau dans le trou ovale pratiqué dans la tôle de revêtement de l’interrupteur de clignoteur, et qui se trouve dessous le levier de commande du clignoteur.
Après avoir installé l’appui du levier de commande à main avec la cage de roulement supérieure, contrôler à l’aide de la jauge SW-187 la distance. A cette distance, le levier de commande du clignoteur et le levier de commande à main de la transmission se trouvent horizontalement en face l’une de l’autre.
Tirer vers le bas hors du fourreau de la colonne le groupe de câbles avec le tube flexible en matière synthétique. L’inscription sur la serrure du volant doit être tournée contre le volant.
Dépose et pose de la serrure du volant.
Au moment d’extraire le groupe de câbles de la serrure hors du fourreau, passer immédiatement un tube flexible avec le groupe de câbles dans le fourreau. Cela permet l’introduction du groupe de câbles lors du remontage de la serrure du volant.
Ajustage et réglage de la direction
Ce travail s’effectue, à part les points ci-après, comme dans le modèle Olympia P.
Extraire les rotules du bras pitman, afin de séparer la direction de la timonerie de direction.
Veiller à ce que la marque en forme d’encoche de la vis du mécanisme de direction soit horizontale en position médiane (quand le boîtier de direction est posé)
L’arbre de direction supérieur ne possède plus de marquage. C’est pourquoi le bras de pitman doit être orienté droit en avant lorsque la direction est montée - (point dur )
Pour le réglage du mécanisme de direction à l’état déposé, on peut fixer un volant Kapitän de secours au flasque du mécanisme de direction ( employer volant de secours de Kapitän 58/59)
LD
Dépose et pose de la direction
Quand toute la direction doit être déposée, il faut déposer le mécanisme de direction et l’ensemble du fourreau de la colonne de direction l’un après l’autre et non simultanément.
Ces deux parties doivent être séparées l’une de l’autre par la séparation de l’accouplement par disques d’acier. Il est dès lors possible de déposer et de poser selon les besoins, soit l’une soit l’autre de ces unités. Avant de déposer le mécanisme de direction ou l’ensemble du fourreau de la colonne de direction, il importe de marquer la position du flasque du mécanisme de direction par rapport au boîtier. Amener à cet effet les roues avant en position droite (point dur).
Dépose et pose du mécanisme de direction
Dévisser le flasque du mécanisme de direction de l’accouplement par disque d’acier. Les disques restent fixées au flasque du fourreau.
Pour arracher le bras de pitman, il faut dévisser le tuyau du pot d’échappement et le glisser vers le bas (pour Kap. 58/59 seulement)
Pour la pose, visser d’abord le mécanisme de direction au longeron du châssis avant ( couple 6- 6,5 mkg), puis en seconde ligne seulement à l’encastrement de roue. L’écrou intérieur de l’encastrement doit être réglé de manière qu’il n’en résulte aucune tension du mécanisme de direction. Visser ensuite l’écrou extérieur et serrer à raison de 6- 6,5 mkg.
Introduire les vis du flasque du mécanisme de direction dans l’accouplement par disques d’acier de manière que les tenons cylindriques des têtes de vis s’engagent dans les évidements correspondants du flasque du fourreau de la colonne de direction.
Intercaler au-dessus, de même qu’en dessous des disques d’acier une ronde arrondie aux arêtes (N° de pièces 904 802)
Désassemblage et assemblage du mécanisme de direction
Arracher le flasque du mécanisme de direction de la vis de direction avec la traverse S-1033 et l’emploi de 2 vis appropriées. Le désassemblage, la révision et l’assemblage du mécanisme de direction se fait en principe comme pour les modèles d’Olympia P et avec les mêmes outils.
Le flasque de mécanisme doit être - l’écrou de direction se trouvant en position médiane (point dur) – passé sur la vis de direction de manière qu’il (le flasque) soit orienté perpendiculairement par rapport à la marque en forme d’encoche pratiquée sur le coté frontal de la vis de direction. La moitié du flasque portant la marque en forme de point doit être dirigée vers le haut.
Lorsque la direction est complètement montée, que les roues avant sont en position droite et que le flasque du mécanisme de direction est perpendiculaire (la marque (point) vers le haut) , les rayons du volant doivent être orientés obliquement vers le bas.
Serrer la vis du flasque du mécanisme de direction avec un couple de 2,2 – 2,5 mkg Contre tenir le flasque, la direction ne doit pas être tournée en position extrême !
L’accouplement par disques d’acier comporte 3 disques, ainsi que le flasque de direction et le flasque du fourreau de la colonne de direction. Les disques d’acier sont fixés au flasque du fourreau par deux boulons six pans normaux et au flasque du mécanisme de direction par deux boulons spéciales (avec tenon cylindrique). Ces tenons doivent s’engager dans les évidements correspondants du flasque du fourreau de la colonne de direction. Pour éviter des pressions d’arêtes, des rondelles aux arêtes arrondies sont insérées sous toutes les vis. Visser l’accouplement à disques d’acier de manière que les flasques soient décalés de 90°.
Dépose et pose du fourreau de la colonne de direction
Dévisser le flasque du mécanisme de direction de l’accouplement à disques d’acier. Les disques d’acier restent donc fixés au flasque du fourreau. Détacher la timonerie de sélection et la pédale d’embrayage. Puis dévisser la fixation du fourreau au tableau de bord. Enlever le couvercle de fermeture du tablier et sortir le fourreau de la colonne de direction par l’intérieur de la voiture.
Au montage, visser d’abord d’une manière encore amovible, l’assemblage fourreau de la colonne de direction au tableau de bord puis visser à fond le flasque du fourreau à l’accouplement du disque acier.
Attention à la position médiane de la direction. Puis fixer définitivement le fourreau au tableau de bord. Veiller à une bonne étanchéité du couvercle de fermeture du tablier.
Désassemblage et assemblage du fourreau de la colonne de direction
1- Arracher le volant avec S-1033 comme dans le type Olympia P. Enlever comme jusqu’ici le levier de commande à main de la transmission.
Les vis à tôle du tuyau de revêtement de l’interrupteur de clignoteur se trouvent à l’intérieur de ce tuyau dessous l’interrupteur de clignoteur. Le tuyau de revêtement peut être enlevé après dévissage du levier de commande de clignoteur.
2- Retirer vers le haut le groupe de câbles et le câble de la serrure du volant. Pousser les câbles depuis le bas.
3- Dévisser les 2 vis à tête noyée de la cage à roulement supérieure du fourreau de la colonne de direction. Avec ces 2 vis, la serrure du volant est également fixée à la cage de roulement.
4- Dévisser le boulon fileté 6 pans et retirer la cage à roulement du fourreau.
5- Extraire en bas le flasque du fourreau à l’aide d’un extracteur.
6- Après dévissage de la bielle de liaison au bas du tuyau de sélection et du levier d’inversion avec support du fourreau, dévisser du fourreau encore deux autres boulons six pans de la cage à roulement inférieure. Attention au ressort de pression. Le tuyau de sélection est guidé dans la cage à roulement inférieure.
Au montage, monter les 2 anneaux en feutre bien graissés, décalés de 180° l’un par rapport à l’autre. Cas échéant, s’aider d’un tournevis afin de bien engager ces anneaux entre les empreintes du fourreau de la colonne. Le roulement inférieur d’arbre de direction est encastré et n’a pas besoin d’entretien. Pour changer ce roulement, l’extraire en frappant de légers coups et avec précaution tout autour de sa circonférence.
Introduire le roulement neuf prudemment par pression.
Le roulement supérieur d’arbre de direction doit être extrait et introduit par pression au moyen d’un bout de tuyau approprié.
Lors de la mise en place du flasque du fourreau de la colonne de direction sur l’arbre de direction, les évidements pratiqués dans la bague d’arrêt de la serrure du volant doivent être décalés de 90° par rapport à ceux du flasque du fourreau. Par ce moyen, la serrure bloque en position droite des roues avant.
Avant de placer l’appui du levier de commande à main, passer 2 tubes en matière synthétique de bas en haut depuis le trou des groupes de câbles dans le fourreau de la colonne, jusqu’au moment où ces 2 tuyaux flexibles dépassent encore d’environ 10 cm le trou latéral du fourreau. Le diamètre de ces flexibles est de 10 mm, soit 12 mm, longueur minimum 1 m.
Introduire les tubes flexibles sortant du trou latéral au haut du fourreau dans le trou ovale pratiqué dans la tôle de revêtement de l’interrupteur de clignoteur, et qui se trouve dessous le levier de commande du clignoteur.
Après avoir installé l’appui du levier de commande à main avec la cage de roulement supérieure, contrôler à l’aide de la jauge SW-187 la distance. A cette distance, le levier de commande du clignoteur et le levier de commande à main de la transmission se trouvent horizontalement en face l’une de l’autre.
Tirer vers le bas hors du fourreau de la colonne le groupe de câbles avec le tube flexible en matière synthétique. L’inscription sur la serrure du volant doit être tournée contre le volant.
Dépose et pose de la serrure du volant.
Au moment d’extraire le groupe de câbles de la serrure hors du fourreau, passer immédiatement un tube flexible avec le groupe de câbles dans le fourreau. Cela permet l’introduction du groupe de câbles lors du remontage de la serrure du volant.
Ajustage et réglage de la direction
Ce travail s’effectue, à part les points ci-après, comme dans le modèle Olympia P.
Extraire les rotules du bras pitman, afin de séparer la direction de la timonerie de direction.
Veiller à ce que la marque en forme d’encoche de la vis du mécanisme de direction soit horizontale en position médiane (quand le boîtier de direction est posé)
L’arbre de direction supérieur ne possède plus de marquage. C’est pourquoi le bras de pitman doit être orienté droit en avant lorsque la direction est montée - (point dur )
Pour le réglage du mécanisme de direction à l’état déposé, on peut fixer un volant Kapitän de secours au flasque du mécanisme de direction ( employer volant de secours de Kapitän 58/59)
LD
Daniel- Messages : 544
Date d'inscription : 22/04/2012
Age : 81
Localisation : Paris Ouest
Opeldel aime ce message
Re: restauration moteur ancien opel des années 60
Direction à vis sans fin et galet et direction à circuit de billes Kapitän 1954.
Pré charge des roulements d’arbre de direction 280 gr
Réglage de l’engrènement galet denté dans l’arbre de direction 300-400 gr
A partir du N° de châssis Kapitän 1954 LV 51'043 (janvier 1955), la voiture Kapitän a reçu la direction à circuit à billes.
La direction de circuit à billes est soumise aux mêmes prescriptions que celles applicables à Kapitän P en ce qui concerne le réglage de la portée de l’arbre de direction est celui de l’engrenage axe Pitman écrou de direction.
Roulement supérieur de l’arbre de direction
Le support du roulement supérieur de l’arbre de direction (bien graisser le filetage avant de visser) doit être visser sur l’appui du levier de commande à main jusqu’au moment où la distance depuis l’arête supérieure de l’appui jusqu’au centre de l’alésage pour la cheville cylindrique est de 40,5 +- 0,75 mm
Dans cette position, l’arête inférieure du support affleure pour ainsi dire l’échancrure de l’appui du levier de commande à main.
Au montage du tuyau de sélection, veiller à ce que tous les endroits coulissants soient bien graissés, tremper les anneaux de feutre dans de la graisse et les installer décalés de 180° l’un par rapport à l’autre.
En bas dans le fourreau de la colonne de direction est placé d’abord un anneau en feutre, puis une rondelle, ensuite un ressort de pression conique (le grand diamètre vers le bas)
Sur l’arbre doivent être glissés deux anneaux amortisseurs en caoutchouc jusqu’environ au milieu, pour empêcher que l’arbre ne heurte le tuyau de sélection.
Nota : Au cas où le tuyau de sélection doit être remplacé sans que la direction soit démontée et le mécanisme désassemblé, les deux anneaux en caoutchouc, après le montage du tuyau de sélection neuf, doivent absolument être poussés sur l’arbre à l’aide d’un tube à paroi mince ( diamètre de ce tube 19 mm à l’intérieur, 21 mm à l’extérieur, longueur 1 m environ)
A défaut de ces anneaux amortisseurs, l’arbre de direction et le tuyau de sélection feraient du bruit en se heurtant.
Si toute la direction a été désassemblée, les anneaux en caoutchouc peuvent être poussés jusqu’au milieu de l’arbre. Au moment de l’introduction prudente de l’arbre dans le fourreau de la colonne, il n’y a par contre aucun danger que les anneaux en caoutchouc soit déplacés.
Au montage de la bielle inférieure de liaison sur le tuyau de sélection il faut veiller à ce que cette bielle s’engage correctement dans son évidemment contre le tuyau de sélection.
Le passage des câbles dans le fourreau de la colonne de direction intervient à l’aide d’un tube en matière synthétique.
L’alésage du manchon de l’axe de Pitman est effectué avec l’alésoir de finition et la douille de guidage S-1047.
Dans le cas où une direction à vis sans fin et galet complète est remplacée par une direction à circuit à billes, il est absolument nécessaire d’échanger en même temps la douille de serrage.
Dans la direction de vis sans fin et galet cette mesure est de 17,5 mm.
Différences entre les douilles de serrage des directions à vis sans fin et galet et celles des directions à circuit à billes
1- Douille de serrage, longueur 81 mm +- 0,5 ( direction à vis sans fin et galet)
2- Bourrelet annulaire ( pour direction à circuit à billes
3- Douille de serrage, longueur 72 mm +- 0,5 ( direction à circuit de billes)
Mesure de distance entre le levier intermédiaire de direction et le support
L’écartement doit être de 20 +- 1,25 mm
LD
Direction à vis sans fin et galet et direction à circuit de billes Kapitän 1954.
Pré charge des roulements d’arbre de direction 280 gr
Réglage de l’engrènement galet denté dans l’arbre de direction 300-400 gr
A partir du N° de châssis Kapitän 1954 LV 51'043 (janvier 1955), la voiture Kapitän a reçu la direction à circuit à billes.
La direction de circuit à billes est soumise aux mêmes prescriptions que celles applicables à Kapitän P en ce qui concerne le réglage de la portée de l’arbre de direction est celui de l’engrenage axe Pitman écrou de direction.
Roulement supérieur de l’arbre de direction
Le support du roulement supérieur de l’arbre de direction (bien graisser le filetage avant de visser) doit être visser sur l’appui du levier de commande à main jusqu’au moment où la distance depuis l’arête supérieure de l’appui jusqu’au centre de l’alésage pour la cheville cylindrique est de 40,5 +- 0,75 mm
Dans cette position, l’arête inférieure du support affleure pour ainsi dire l’échancrure de l’appui du levier de commande à main.
Au montage du tuyau de sélection, veiller à ce que tous les endroits coulissants soient bien graissés, tremper les anneaux de feutre dans de la graisse et les installer décalés de 180° l’un par rapport à l’autre.
En bas dans le fourreau de la colonne de direction est placé d’abord un anneau en feutre, puis une rondelle, ensuite un ressort de pression conique (le grand diamètre vers le bas)
Sur l’arbre doivent être glissés deux anneaux amortisseurs en caoutchouc jusqu’environ au milieu, pour empêcher que l’arbre ne heurte le tuyau de sélection.
Nota : Au cas où le tuyau de sélection doit être remplacé sans que la direction soit démontée et le mécanisme désassemblé, les deux anneaux en caoutchouc, après le montage du tuyau de sélection neuf, doivent absolument être poussés sur l’arbre à l’aide d’un tube à paroi mince ( diamètre de ce tube 19 mm à l’intérieur, 21 mm à l’extérieur, longueur 1 m environ)
A défaut de ces anneaux amortisseurs, l’arbre de direction et le tuyau de sélection feraient du bruit en se heurtant.
Si toute la direction a été désassemblée, les anneaux en caoutchouc peuvent être poussés jusqu’au milieu de l’arbre. Au moment de l’introduction prudente de l’arbre dans le fourreau de la colonne, il n’y a par contre aucun danger que les anneaux en caoutchouc soit déplacés.
Au montage de la bielle inférieure de liaison sur le tuyau de sélection il faut veiller à ce que cette bielle s’engage correctement dans son évidemment contre le tuyau de sélection.
Le passage des câbles dans le fourreau de la colonne de direction intervient à l’aide d’un tube en matière synthétique.
L’alésage du manchon de l’axe de Pitman est effectué avec l’alésoir de finition et la douille de guidage S-1047.
Dans le cas où une direction à vis sans fin et galet complète est remplacée par une direction à circuit à billes, il est absolument nécessaire d’échanger en même temps la douille de serrage.
Dans la direction de vis sans fin et galet cette mesure est de 17,5 mm.
Différences entre les douilles de serrage des directions à vis sans fin et galet et celles des directions à circuit à billes
1- Douille de serrage, longueur 81 mm +- 0,5 ( direction à vis sans fin et galet)
2- Bourrelet annulaire ( pour direction à circuit à billes
3- Douille de serrage, longueur 72 mm +- 0,5 ( direction à circuit de billes)
Mesure de distance entre le levier intermédiaire de direction et le support
L’écartement doit être de 20 +- 1,25 mm
LD
Pré charge des roulements d’arbre de direction 280 gr
Réglage de l’engrènement galet denté dans l’arbre de direction 300-400 gr
A partir du N° de châssis Kapitän 1954 LV 51'043 (janvier 1955), la voiture Kapitän a reçu la direction à circuit à billes.
La direction de circuit à billes est soumise aux mêmes prescriptions que celles applicables à Kapitän P en ce qui concerne le réglage de la portée de l’arbre de direction est celui de l’engrenage axe Pitman écrou de direction.
Roulement supérieur de l’arbre de direction
Le support du roulement supérieur de l’arbre de direction (bien graisser le filetage avant de visser) doit être visser sur l’appui du levier de commande à main jusqu’au moment où la distance depuis l’arête supérieure de l’appui jusqu’au centre de l’alésage pour la cheville cylindrique est de 40,5 +- 0,75 mm
Dans cette position, l’arête inférieure du support affleure pour ainsi dire l’échancrure de l’appui du levier de commande à main.
Au montage du tuyau de sélection, veiller à ce que tous les endroits coulissants soient bien graissés, tremper les anneaux de feutre dans de la graisse et les installer décalés de 180° l’un par rapport à l’autre.
En bas dans le fourreau de la colonne de direction est placé d’abord un anneau en feutre, puis une rondelle, ensuite un ressort de pression conique (le grand diamètre vers le bas)
Sur l’arbre doivent être glissés deux anneaux amortisseurs en caoutchouc jusqu’environ au milieu, pour empêcher que l’arbre ne heurte le tuyau de sélection.
Nota : Au cas où le tuyau de sélection doit être remplacé sans que la direction soit démontée et le mécanisme désassemblé, les deux anneaux en caoutchouc, après le montage du tuyau de sélection neuf, doivent absolument être poussés sur l’arbre à l’aide d’un tube à paroi mince ( diamètre de ce tube 19 mm à l’intérieur, 21 mm à l’extérieur, longueur 1 m environ)
A défaut de ces anneaux amortisseurs, l’arbre de direction et le tuyau de sélection feraient du bruit en se heurtant.
Si toute la direction a été désassemblée, les anneaux en caoutchouc peuvent être poussés jusqu’au milieu de l’arbre. Au moment de l’introduction prudente de l’arbre dans le fourreau de la colonne, il n’y a par contre aucun danger que les anneaux en caoutchouc soit déplacés.
Au montage de la bielle inférieure de liaison sur le tuyau de sélection il faut veiller à ce que cette bielle s’engage correctement dans son évidemment contre le tuyau de sélection.
Le passage des câbles dans le fourreau de la colonne de direction intervient à l’aide d’un tube en matière synthétique.
L’alésage du manchon de l’axe de Pitman est effectué avec l’alésoir de finition et la douille de guidage S-1047.
Dans le cas où une direction à vis sans fin et galet complète est remplacée par une direction à circuit à billes, il est absolument nécessaire d’échanger en même temps la douille de serrage.
Dans la direction de vis sans fin et galet cette mesure est de 17,5 mm.
Différences entre les douilles de serrage des directions à vis sans fin et galet et celles des directions à circuit à billes
1- Douille de serrage, longueur 81 mm +- 0,5 ( direction à vis sans fin et galet)
2- Bourrelet annulaire ( pour direction à circuit à billes
3- Douille de serrage, longueur 72 mm +- 0,5 ( direction à circuit de billes)
Mesure de distance entre le levier intermédiaire de direction et le support
L’écartement doit être de 20 +- 1,25 mm
LD
Direction à vis sans fin et galet et direction à circuit de billes Kapitän 1954.
Pré charge des roulements d’arbre de direction 280 gr
Réglage de l’engrènement galet denté dans l’arbre de direction 300-400 gr
A partir du N° de châssis Kapitän 1954 LV 51'043 (janvier 1955), la voiture Kapitän a reçu la direction à circuit à billes.
La direction de circuit à billes est soumise aux mêmes prescriptions que celles applicables à Kapitän P en ce qui concerne le réglage de la portée de l’arbre de direction est celui de l’engrenage axe Pitman écrou de direction.
Roulement supérieur de l’arbre de direction
Le support du roulement supérieur de l’arbre de direction (bien graisser le filetage avant de visser) doit être visser sur l’appui du levier de commande à main jusqu’au moment où la distance depuis l’arête supérieure de l’appui jusqu’au centre de l’alésage pour la cheville cylindrique est de 40,5 +- 0,75 mm
Dans cette position, l’arête inférieure du support affleure pour ainsi dire l’échancrure de l’appui du levier de commande à main.
Au montage du tuyau de sélection, veiller à ce que tous les endroits coulissants soient bien graissés, tremper les anneaux de feutre dans de la graisse et les installer décalés de 180° l’un par rapport à l’autre.
En bas dans le fourreau de la colonne de direction est placé d’abord un anneau en feutre, puis une rondelle, ensuite un ressort de pression conique (le grand diamètre vers le bas)
Sur l’arbre doivent être glissés deux anneaux amortisseurs en caoutchouc jusqu’environ au milieu, pour empêcher que l’arbre ne heurte le tuyau de sélection.
Nota : Au cas où le tuyau de sélection doit être remplacé sans que la direction soit démontée et le mécanisme désassemblé, les deux anneaux en caoutchouc, après le montage du tuyau de sélection neuf, doivent absolument être poussés sur l’arbre à l’aide d’un tube à paroi mince ( diamètre de ce tube 19 mm à l’intérieur, 21 mm à l’extérieur, longueur 1 m environ)
A défaut de ces anneaux amortisseurs, l’arbre de direction et le tuyau de sélection feraient du bruit en se heurtant.
Si toute la direction a été désassemblée, les anneaux en caoutchouc peuvent être poussés jusqu’au milieu de l’arbre. Au moment de l’introduction prudente de l’arbre dans le fourreau de la colonne, il n’y a par contre aucun danger que les anneaux en caoutchouc soit déplacés.
Au montage de la bielle inférieure de liaison sur le tuyau de sélection il faut veiller à ce que cette bielle s’engage correctement dans son évidemment contre le tuyau de sélection.
Le passage des câbles dans le fourreau de la colonne de direction intervient à l’aide d’un tube en matière synthétique.
L’alésage du manchon de l’axe de Pitman est effectué avec l’alésoir de finition et la douille de guidage S-1047.
Dans le cas où une direction à vis sans fin et galet complète est remplacée par une direction à circuit à billes, il est absolument nécessaire d’échanger en même temps la douille de serrage.
Dans la direction de vis sans fin et galet cette mesure est de 17,5 mm.
Différences entre les douilles de serrage des directions à vis sans fin et galet et celles des directions à circuit à billes
1- Douille de serrage, longueur 81 mm +- 0,5 ( direction à vis sans fin et galet)
2- Bourrelet annulaire ( pour direction à circuit à billes
3- Douille de serrage, longueur 72 mm +- 0,5 ( direction à circuit de billes)
Mesure de distance entre le levier intermédiaire de direction et le support
L’écartement doit être de 20 +- 1,25 mm
LD
Daniel- Messages : 544
Date d'inscription : 22/04/2012
Age : 81
Localisation : Paris Ouest
Opeldel aime ce message
Re: restauration moteur ancien opel des années 60
Suspension de roues avant Kapitaen ( Kapitän) dès 1958.
Suspension de roue avant
Branches de triangles de longueur inégale, disposées d’une manière non parallèle.
Axes de triangles croisés l’un part rapport à l’autre.
Dépose et pose de l’essieu avant
Les vis de fixation de l’essieu avant présentent une assise ajustée dans les blocs d’amortissement et aux points de réception du châssis avant. Si l’essieu avant résiste à la dépose, chasser d’abord les boulons au moyen d’un mandrin en métal doux. Ensuite l’essieu avant peut être enlevé.
A la pose de l’essieu avant, veiller à ce que les extrémités supérieures des tuyaux intérieurs des blocs d’amortissement s’engagent dans les trous des points de réception aux châssis avant, et centrent ainsi exactement l’essieu.
Avant l’application, introduire les boulons filetés de fixation de l’essieu avant dans les blocs d’amortissement en caoutchouc, servant au centrage.
Serrer les boulons de fixation de l’essieu avant gauche et droit avec 9 - 10 mkg et celles de l’avant avec 6 - 6,7 mkg
L’essieu avant doit, dans le plan de mesure, être suspendu dans le caoutchouc.
La distance entre la face frontale dentée du caoutchouc d’amortissement et la surface d’application qui lui fait face, doit être tout autour uniformément de 2,5 mm environ.
La voiture se trouve dans le plan de mesure quand il y a entre la surface plane du sol et les extrémités antérieures des longerons du châssis avant une distance de 332 mm et entre les extrémités postérieures des longerons de carrosserie une distance de 320 mm.
Attention :
Fixer les flexibles de frein des roues avant sans torsion et seulement lors du braquage intérieur complet des roues, c’est-à-dire roue gauche braquée à gauche, roue droite braquée à droite.
Remplacement des blocs d’amortissement en caoutchouc.
Les blocs d’amortissement sont interchangeables et se trouvent, à l’état comprimés, sous pré -charge.
La pression de compression lors du montage pour les blocs de gauche et de droite est d’au moins 450 kg et pour celui de l’avant d’au moins 150 kg
La compression doit être effectuée à l’aide de la presse de pression SW-324 sur une presse avec manomètre.
Comprimer les blocs d’amortissement à sec.
Les fentes qui se font face à l’extérieur du bloc d’amortissement en caoutchouc doivent, se trouver l’une derrière l’autre en direction de marche. Le côté frontal de la rondelle dentée caoutchouc doit se trouver vers le haut à l’état monté.
Ressorts avant
Pour la pose et la dépose des ressorts avant, il faut employer le nouveau dispositif de serrage S-1158. Veillez à ce qu’aucun montage, le ressort avant s’engage correctement dans l’anneau d’amortissement.
Stabilisateur
Les mesures de contrôle pour le stabilisateur sont les suivantes
Distance de milieu de l’œil à milieu de l’œil 816 + - 3 mm
Ecart du parallélisme des extrémités du stabilisateur jusqu’à 4 mm
Serrer les écrous extérieurs de la fixation du stabilisateur jusqu’au moment où les 2 tampons en caoutchouc supérieurs sont comprimés à la mesure de 42 - 1mm. Serrer les vis de couvercle de portée du stabilisateur au longeron de l’essieu avant avec 2 – 2,5 mkg
Fusées
La rotule supérieure est fixée dans la fusée, comme dans les types Olympia P. La tige de la rotule inférieure possède dans la fusée un siège conique. Avant la dépose de la fusée, il faut déposer l’amortisseur, comprimer le ressort avant et détacher la tige de la rotule inférieure.
Les rotules ne peuvent pas être désassemblées.
Avant la pose de la fusée, placer sur les tiges de rotule les capuchons remplis de graisse.
La rotule inférieure présente un jeu quand elle n’est pas chargée.
La rotule supérieure est exempte de jeu.
Triangles supérieurs et inférieurs
Ces triangles sont vissés au corps d’essieu et doivent être déposés pour le désassemblage et le remplacement des douilles filetées. Au dévissage du triangle supérieur, prendre garde aux espaceurs fourchus pour le réglage de la chasse et du carrossage. Marquer, évent, le nombre des espaceurs en tôle au corps d’essieu. Cependant, il faut toujours vérifier le réglage de la géométrie des roues avant.
Le triangle supérieur est vissé au corps avec un couple de 8,6 – 9,5 mkg et le triangle inférieur avec 4,5 – 5mkg
Les douilles filetées des triangles supérieurs et inférieurs sont identiques et sont livrées pour leur remplacement avec une sur dimension de 0,4 mm et 0,8 mm du diamètre extérieur. L’échange de ces douilles ne peut être opéré que sur les triangles déposés. Employer à cet effet les pièces à pré charge S-1159 pour triangle inférieur et S-1160 pour le triangle supérieur.
Les trous pour les douilles filetées dans les branches de triangle doivent être alésés au moyen d’un alésoir réglable (24,5 – 29 mm) Le réglage de l’alésoir a lieu avec les anneaux calibrés S-1148.
Si le triangle est complètement désassemblé, il faut mesurer d’abord visser la rotule aux branches de triangle, avant le vissage des douilles filetées, afin de réaliser une pré charge axiale des branches de triangle par rapport aux axes de triangle. L’angle entre l’axe et les branches de triangle inférieur est d’environ 25° et entre l’axe et les branches du triangle supérieur d’environ 90°, par rapport à la surface d’application de l’axe. Ceci correspond à la position de travail à l’état posé. Ce résultat peut être obtenu en calant à l’aide de blocs de bois appropriés.
Pour le vissage des douilles filetées, il faut mesurer avec la pièce à pré charge mise en place un couple de 19 – 22 mkg et au contrôle de l’assise ferme, sans pièce à pré charge, un couple de 11 – 15 mkg Visser les graisseurs de manière qu’ils soient dirigés vers le bas.
Roulements de roues et moyeux de roues avant
Pour l’installation par pression des bagues de roulement à billes et du joint annulaire dans le moyeu, employer la pièce de pression SW-323.
Géométrie de direction
Les conditions générales sont les mêmes que celles applicables aux types Olympia P.
Pression du pneu : Avant 1,6 arrière 1,8
Amener la voiture au plan de mesure.
Distance A à l’avant 332 mm Extrémité antérieure du longeron par rapport à la surface du sol plane.
Extrémité postérieure du longeron Distance B à l’arrière 320 mm par rapport à la surface du sol plane.
Le réglage du carrossage et de la chasse intervient à l’aide des espaceurs fourchus en tôle, intercalés entre les axes de triangles supérieurs et le corps d’essieu.
L’ajustement du carrossage se réalise par une intercalation égale d’espaceurs. La chasse est réglée par une intercalation inégale d’espaceurs. La différence d’épaisseur des espaceurs en tôle à un axe de triangle ne doit être que tout au plus de 0,75 mm. Par conséquent, la correction de la chasse n’est possible que dans les limites de cette différence d’épaisseur.
Pincement : 2 – 4 mm
Carrossage : 0° +- ¼°
Chasse : 1 ½° + - ½°
Angle de braquage avec la roue extérieure à 20°, roue intérieure 20 ½°
Le réglage du carrossage a la primauté sur celui de la chasse.
Les tôles d’épaisseur suivantes sont disponibles :
N° de pièces Epaisseur des espaceurs
3 08 713 0,40 mm
3 08 710 0,75 mm
3 08 711 1,50 mm
3 08 712 3,00 mm
Le réglage du pincement se fait aux 2 barres d’accouplement extérieures de la même façon que dans les types Olympia P.
La barre d’accouplement avec rotule et la barre avec œillet sont aplaties aux côtés intérieurs jusqu’aux demi-diamètre. Veiller pendant le montage des barres à ce que les deux extrémités aplaties glissent l’une sur l’autre.
Avant de visser le levier intermédiaire de direction, contrôler la distance entre le support de ce levier, laquelle doit être de 15 + 2,5 mm.
Serrer les vis de fixation du levier intermédiaire de direction avec 6 – 6,5 mkg
LD Historien de l'OOCB
Suspension de roue avant
Branches de triangles de longueur inégale, disposées d’une manière non parallèle.
Axes de triangles croisés l’un part rapport à l’autre.
Dépose et pose de l’essieu avant
Les vis de fixation de l’essieu avant présentent une assise ajustée dans les blocs d’amortissement et aux points de réception du châssis avant. Si l’essieu avant résiste à la dépose, chasser d’abord les boulons au moyen d’un mandrin en métal doux. Ensuite l’essieu avant peut être enlevé.
A la pose de l’essieu avant, veiller à ce que les extrémités supérieures des tuyaux intérieurs des blocs d’amortissement s’engagent dans les trous des points de réception aux châssis avant, et centrent ainsi exactement l’essieu.
Avant l’application, introduire les boulons filetés de fixation de l’essieu avant dans les blocs d’amortissement en caoutchouc, servant au centrage.
Serrer les boulons de fixation de l’essieu avant gauche et droit avec 9 - 10 mkg et celles de l’avant avec 6 - 6,7 mkg
L’essieu avant doit, dans le plan de mesure, être suspendu dans le caoutchouc.
La distance entre la face frontale dentée du caoutchouc d’amortissement et la surface d’application qui lui fait face, doit être tout autour uniformément de 2,5 mm environ.
La voiture se trouve dans le plan de mesure quand il y a entre la surface plane du sol et les extrémités antérieures des longerons du châssis avant une distance de 332 mm et entre les extrémités postérieures des longerons de carrosserie une distance de 320 mm.
Attention :
Fixer les flexibles de frein des roues avant sans torsion et seulement lors du braquage intérieur complet des roues, c’est-à-dire roue gauche braquée à gauche, roue droite braquée à droite.
Remplacement des blocs d’amortissement en caoutchouc.
Les blocs d’amortissement sont interchangeables et se trouvent, à l’état comprimés, sous pré -charge.
La pression de compression lors du montage pour les blocs de gauche et de droite est d’au moins 450 kg et pour celui de l’avant d’au moins 150 kg
La compression doit être effectuée à l’aide de la presse de pression SW-324 sur une presse avec manomètre.
Comprimer les blocs d’amortissement à sec.
Les fentes qui se font face à l’extérieur du bloc d’amortissement en caoutchouc doivent, se trouver l’une derrière l’autre en direction de marche. Le côté frontal de la rondelle dentée caoutchouc doit se trouver vers le haut à l’état monté.
Ressorts avant
Pour la pose et la dépose des ressorts avant, il faut employer le nouveau dispositif de serrage S-1158. Veillez à ce qu’aucun montage, le ressort avant s’engage correctement dans l’anneau d’amortissement.
Stabilisateur
Les mesures de contrôle pour le stabilisateur sont les suivantes
Distance de milieu de l’œil à milieu de l’œil 816 + - 3 mm
Ecart du parallélisme des extrémités du stabilisateur jusqu’à 4 mm
Serrer les écrous extérieurs de la fixation du stabilisateur jusqu’au moment où les 2 tampons en caoutchouc supérieurs sont comprimés à la mesure de 42 - 1mm. Serrer les vis de couvercle de portée du stabilisateur au longeron de l’essieu avant avec 2 – 2,5 mkg
Fusées
La rotule supérieure est fixée dans la fusée, comme dans les types Olympia P. La tige de la rotule inférieure possède dans la fusée un siège conique. Avant la dépose de la fusée, il faut déposer l’amortisseur, comprimer le ressort avant et détacher la tige de la rotule inférieure.
Les rotules ne peuvent pas être désassemblées.
Avant la pose de la fusée, placer sur les tiges de rotule les capuchons remplis de graisse.
La rotule inférieure présente un jeu quand elle n’est pas chargée.
La rotule supérieure est exempte de jeu.
Triangles supérieurs et inférieurs
Ces triangles sont vissés au corps d’essieu et doivent être déposés pour le désassemblage et le remplacement des douilles filetées. Au dévissage du triangle supérieur, prendre garde aux espaceurs fourchus pour le réglage de la chasse et du carrossage. Marquer, évent, le nombre des espaceurs en tôle au corps d’essieu. Cependant, il faut toujours vérifier le réglage de la géométrie des roues avant.
Le triangle supérieur est vissé au corps avec un couple de 8,6 – 9,5 mkg et le triangle inférieur avec 4,5 – 5mkg
Les douilles filetées des triangles supérieurs et inférieurs sont identiques et sont livrées pour leur remplacement avec une sur dimension de 0,4 mm et 0,8 mm du diamètre extérieur. L’échange de ces douilles ne peut être opéré que sur les triangles déposés. Employer à cet effet les pièces à pré charge S-1159 pour triangle inférieur et S-1160 pour le triangle supérieur.
Les trous pour les douilles filetées dans les branches de triangle doivent être alésés au moyen d’un alésoir réglable (24,5 – 29 mm) Le réglage de l’alésoir a lieu avec les anneaux calibrés S-1148.
Si le triangle est complètement désassemblé, il faut mesurer d’abord visser la rotule aux branches de triangle, avant le vissage des douilles filetées, afin de réaliser une pré charge axiale des branches de triangle par rapport aux axes de triangle. L’angle entre l’axe et les branches de triangle inférieur est d’environ 25° et entre l’axe et les branches du triangle supérieur d’environ 90°, par rapport à la surface d’application de l’axe. Ceci correspond à la position de travail à l’état posé. Ce résultat peut être obtenu en calant à l’aide de blocs de bois appropriés.
Pour le vissage des douilles filetées, il faut mesurer avec la pièce à pré charge mise en place un couple de 19 – 22 mkg et au contrôle de l’assise ferme, sans pièce à pré charge, un couple de 11 – 15 mkg Visser les graisseurs de manière qu’ils soient dirigés vers le bas.
Roulements de roues et moyeux de roues avant
Pour l’installation par pression des bagues de roulement à billes et du joint annulaire dans le moyeu, employer la pièce de pression SW-323.
Géométrie de direction
Les conditions générales sont les mêmes que celles applicables aux types Olympia P.
Pression du pneu : Avant 1,6 arrière 1,8
Amener la voiture au plan de mesure.
Distance A à l’avant 332 mm Extrémité antérieure du longeron par rapport à la surface du sol plane.
Extrémité postérieure du longeron Distance B à l’arrière 320 mm par rapport à la surface du sol plane.
Le réglage du carrossage et de la chasse intervient à l’aide des espaceurs fourchus en tôle, intercalés entre les axes de triangles supérieurs et le corps d’essieu.
L’ajustement du carrossage se réalise par une intercalation égale d’espaceurs. La chasse est réglée par une intercalation inégale d’espaceurs. La différence d’épaisseur des espaceurs en tôle à un axe de triangle ne doit être que tout au plus de 0,75 mm. Par conséquent, la correction de la chasse n’est possible que dans les limites de cette différence d’épaisseur.
Pincement : 2 – 4 mm
Carrossage : 0° +- ¼°
Chasse : 1 ½° + - ½°
Angle de braquage avec la roue extérieure à 20°, roue intérieure 20 ½°
Le réglage du carrossage a la primauté sur celui de la chasse.
Les tôles d’épaisseur suivantes sont disponibles :
N° de pièces Epaisseur des espaceurs
3 08 713 0,40 mm
3 08 710 0,75 mm
3 08 711 1,50 mm
3 08 712 3,00 mm
Le réglage du pincement se fait aux 2 barres d’accouplement extérieures de la même façon que dans les types Olympia P.
La barre d’accouplement avec rotule et la barre avec œillet sont aplaties aux côtés intérieurs jusqu’aux demi-diamètre. Veiller pendant le montage des barres à ce que les deux extrémités aplaties glissent l’une sur l’autre.
Avant de visser le levier intermédiaire de direction, contrôler la distance entre le support de ce levier, laquelle doit être de 15 + 2,5 mm.
Serrer les vis de fixation du levier intermédiaire de direction avec 6 – 6,5 mkg
LD Historien de l'OOCB
Daniel- Messages : 544
Date d'inscription : 22/04/2012
Age : 81
Localisation : Paris Ouest
Opeldel aime ce message
Re: restauration moteur ancien opel des années 60
Merci, Daniel! 

lucdm- Admin
- Messages : 3261
Date d'inscription : 20/04/2012
Age : 68
Localisation : Natoye / Président OOCB
Re: restauration moteur ancien opel des années 60
- Bonjour aux adhérents du club de l’OOCB
- Un petit cadeau de fin d’année très utile.
- Je viens de me payer un réchauffeur à induction pour défaire les boulons récalcitrants. Avec la rouille les boulons deviennent impossibles à desserrer et même à se rompre à la moindre traction un peu musclée. Vis, bougie, injecteur, collecteur d’échappement, boulon ou écrou situé dans un endroit assez difficile, etc. Plus besoin de chalumeau, etc. De cette manière, le verre, le caoutchouc, le plastique et les surfaces peintes ne sont pas endommagés dans la zone à traiter ou même dans les zones environnantes. L’écrou se desserra très facilement, avec une clé plate ou à tube, avec ou sans rallonge, clé à cliquet, etc. Attention : l’écrou ou le boulon, est lui très chaud, le prendre avec une pince ou avec des gants et le laisser refroidir avant de le manipuler.
Un Kit de réchauffeur d'induction magnétique de conducteur de dissipateur d'écrou rouillé de décolleur de chaleur – 900W - 220V avec ventilateur de refroidissement.
- Caractéristiques :
1. Système de chauffage sans perte, sans flamme.
2. 1 minute Processus de suppression. 97% de consommation d'énergie en moins. 1 cent pour enlever 1 boulon ne vous coûte que 1 cent. Poids de 1,9 kg
3. Adoptez la technologie de conduction de chaleur, aucune flamme, sécurité et protection de l'environnement. Cela réduit considérablement les risques d'accidents et de dommages potentiels.
4. Le plus rapide 60 secondes à 500 degrés centigrades, chauffage rapide, facile à enlever les vis rouillées avec une clé.
5. Ne pas endommager le boulon et le matériau autour de l'équipement.
6. Facile à utiliser, seulement 3 minutes à maîtriser.
7. Équipé de deux lumières LED pour les espaces étroits et sombres.
8. Plus de bobines sont disponibles. Chaque ligne convient à la taille de différents types de boulons.
9. La taille de deux livres. Par rapport aux outils à flamme conventionnels, il peut sauver la division de l'espace et le pistolet à démontage rapide à injection de capital. Il ne se limite pas aux voitures, aux équipements agricoles, aux navires et aux citernes. Il est très approprié pour l'entretien de diverses machines-outils.
Spécification :
Il existe 3 modèles suivant la tension à utiliser :
Modèle : 12V 110V 220V
Tension d'entrée 12V 110V 50/60Hz 220V 50/60Hz
Courant d'entrée 40A 7A 4A
Puissance de sortie 500W 500-900W 500-900W
Tension de sortie 40V 45V 25V
Courant de sortie 120A 180A 180A
- REMARQUE: Le temps de travail maximum pour une seule opération est de 4 ~ 5 minutes et il y aura une surchauffe ! Après la protection contre la surchauffe, le moteur principal et la bobine doivent être refroidis avant de pouvoir être utilisés pour la deuxième fois.
- Emballage inclus :
1 x HBR Main
1 bobine flexible 1,17 m Soft
1 bobine de 18 mm (diamètre de l'alésage) (Longueur 20 cm)
1 bobine de 22 mm (diamètre de l'alésage) (Longueur 20 cm)
1 bobine de 28mm (diamètre d'alésage) (Longueur 20cm)
2 x vis
1 x Manuel de l'utilisateur (multi langues)
- 1 mallette de transport -
- Ce modèle n’est pas un modèle à usage intensif. Il faut donc le laisser refroidir avant une prochaine utilisation. Mais bien utilisé, il fait des miracles. Il peut aussi redonner une seconde vie à des rondelles en cuivre qui deviennent dur et cassante. En chauffant la rondelle en cuivre, par l’induction, elle redeviendra plus souple et retrouvera une nouvelle vie.
- Son prix est de 250 Euros + frais de port.
- Pour un usage professionnel (intensif, réchauffement rapide), il existe des modèles en 1500W et + en 220V, ( station de 3 kw) de 800 Euros à plusieurs milliers d’Euros.
LD – Historien de l’OOCB.
- Un petit cadeau de fin d’année très utile.
- Je viens de me payer un réchauffeur à induction pour défaire les boulons récalcitrants. Avec la rouille les boulons deviennent impossibles à desserrer et même à se rompre à la moindre traction un peu musclée. Vis, bougie, injecteur, collecteur d’échappement, boulon ou écrou situé dans un endroit assez difficile, etc. Plus besoin de chalumeau, etc. De cette manière, le verre, le caoutchouc, le plastique et les surfaces peintes ne sont pas endommagés dans la zone à traiter ou même dans les zones environnantes. L’écrou se desserra très facilement, avec une clé plate ou à tube, avec ou sans rallonge, clé à cliquet, etc. Attention : l’écrou ou le boulon, est lui très chaud, le prendre avec une pince ou avec des gants et le laisser refroidir avant de le manipuler.
Un Kit de réchauffeur d'induction magnétique de conducteur de dissipateur d'écrou rouillé de décolleur de chaleur – 900W - 220V avec ventilateur de refroidissement.
- Caractéristiques :
1. Système de chauffage sans perte, sans flamme.
2. 1 minute Processus de suppression. 97% de consommation d'énergie en moins. 1 cent pour enlever 1 boulon ne vous coûte que 1 cent. Poids de 1,9 kg
3. Adoptez la technologie de conduction de chaleur, aucune flamme, sécurité et protection de l'environnement. Cela réduit considérablement les risques d'accidents et de dommages potentiels.
4. Le plus rapide 60 secondes à 500 degrés centigrades, chauffage rapide, facile à enlever les vis rouillées avec une clé.
5. Ne pas endommager le boulon et le matériau autour de l'équipement.
6. Facile à utiliser, seulement 3 minutes à maîtriser.
7. Équipé de deux lumières LED pour les espaces étroits et sombres.
8. Plus de bobines sont disponibles. Chaque ligne convient à la taille de différents types de boulons.
9. La taille de deux livres. Par rapport aux outils à flamme conventionnels, il peut sauver la division de l'espace et le pistolet à démontage rapide à injection de capital. Il ne se limite pas aux voitures, aux équipements agricoles, aux navires et aux citernes. Il est très approprié pour l'entretien de diverses machines-outils.
Spécification :
Il existe 3 modèles suivant la tension à utiliser :
Modèle : 12V 110V 220V
Tension d'entrée 12V 110V 50/60Hz 220V 50/60Hz
Courant d'entrée 40A 7A 4A
Puissance de sortie 500W 500-900W 500-900W
Tension de sortie 40V 45V 25V
Courant de sortie 120A 180A 180A
- REMARQUE: Le temps de travail maximum pour une seule opération est de 4 ~ 5 minutes et il y aura une surchauffe ! Après la protection contre la surchauffe, le moteur principal et la bobine doivent être refroidis avant de pouvoir être utilisés pour la deuxième fois.
- Emballage inclus :
1 x HBR Main
1 bobine flexible 1,17 m Soft
1 bobine de 18 mm (diamètre de l'alésage) (Longueur 20 cm)
1 bobine de 22 mm (diamètre de l'alésage) (Longueur 20 cm)
1 bobine de 28mm (diamètre d'alésage) (Longueur 20cm)
2 x vis
1 x Manuel de l'utilisateur (multi langues)
- 1 mallette de transport -
- Ce modèle n’est pas un modèle à usage intensif. Il faut donc le laisser refroidir avant une prochaine utilisation. Mais bien utilisé, il fait des miracles. Il peut aussi redonner une seconde vie à des rondelles en cuivre qui deviennent dur et cassante. En chauffant la rondelle en cuivre, par l’induction, elle redeviendra plus souple et retrouvera une nouvelle vie.
- Son prix est de 250 Euros + frais de port.
- Pour un usage professionnel (intensif, réchauffement rapide), il existe des modèles en 1500W et + en 220V, ( station de 3 kw) de 800 Euros à plusieurs milliers d’Euros.
LD – Historien de l’OOCB.
Daniel- Messages : 544
Date d'inscription : 22/04/2012
Age : 81
Localisation : Paris Ouest
Opeldel aime ce message
Re: restauration moteur ancien opel des années 60
Merci pour cette précieuse info, Daniel!
lucdm- Admin
- Messages : 3261
Date d'inscription : 20/04/2012
Age : 68
Localisation : Natoye / Président OOCB
Opeldel- Messages : 228
Date d'inscription : 21/04/2012
Age : 58
Localisation : Seloignes
Re: restauration moteur ancien opel des années 60
- Purger son circuit de frein sur nos anciennes OPEL
- Un circuit hydraulique mal purgé est beaucoup moins efficace qu’à la normale. À l’échauffement, il peut devenir totalement inopérant. Dans le cas du circuit d’embrayage, c’est très désagréable, mais, dans celui du circuit de freins, c’est bien sûr très dangereux.
- Il faut purger le circuit hydraulique pour deux raisons essentielles tout d’abord, si l’on vient d’effectuer des travaux sur la partie hydraulique, il y aura des bulles d’air qui auront pénétré dans le liquide. Or l’air est compressible alors que la qualité principale demandée à un liquide est justement de ne pas l’être. Il faut donc éliminer ces bulles d’air. D’autre part, le liquide de frein est avide d’humidité, et, avec le temps, il finit par contenir de l’eau en quantité suffisante pour faire rouiller les parties métalliques des pistons et des cylindres en contact avec ce liquide.
- De plus, et toujours du fait du vieillissement, il bout plus facilement, sous l’effet de la grande quantité de chaleur dégagée par les freins, d’autant plus que la présence d’eau facilite ce phénomène. En effet, un bon liquide de frein bout entre 180 et 280 degrés. Le bouillonnement dégage de l’air et rend le liquide compressible, élastique. La pédale de frein ou d’embrayage devient alors mol et « spongieuse » À la limite, en cas de fort échauffement, elle peut devenir complètement inefficace en conduite sportive, par exemple. Il faudra donc purger le circuit hydraulique de freins régulièrement tous les deux ans ou tous les 20.000 km au moins, par mesure de sécurité.
- Après avoir serré le frein à main, desserrez les écrous de roue à l’aide d’une croix, montez la voiture sur cric, puis dévissez complètement les écrous de roue.
- Retirez la roue, puis enfilez le tuyau de purge en plastique transparent sur la vis de purge. - - - Desserrez ensuite la vis de purge à l’aide d’une clé appropriée.
- Placez un récipient en verre sous le tuyau de purge, puis demandez à votre aide, de pomper très lentement sur la pédale de frein pour chasser l’air contenu en suspension dans le vieux Lockheed. Faites pomper jusqu’à ce que le bocal se soit vidé entièrement du liquide de frein usagé (reconnaissable à sa couleur noire)
- Le Lockheed se charge d’humidité avec l’âge, et est alors dangereux pour votre circuit de freinage, car il fait alors rouiller l’intérieur des cylindres de roue. Ici, nous voyons clairement l’émulsion formée par le mélange Lockheed/eau/air. Notons, qu’il ne faut sous aucun prétexte réutiliser le vieux Lockheed.
- Vérifications préliminaires :
- Le bocal étant vide, nettoyez-en le fond à l’aide d’un chiffon propre. Sur cette voiture, le circuit de frein étant double, le bocal possède un double réservoir.
- Sur cette voiture n’ayant qu’un simple circuit, le bocal de Lockheed est plus simple à nettoyer. Notons qu’ici, le maître cylindre est directement accolé au servo.
- Une fois le bocal nettoyé, remplissez-le de nouveau avec du Lockheed neuf. Faites très attention de ne pas renverser de liquide sur la carrosserie, car ce dernier attaque la peinture. Ne dépassez pas le repère « maxi »
- Avant d’effectuer la purge elle-même, il y a un certain nombre de précautions à prendre. Tout d’abord, il faut bien évidemment que tous les éléments du circuit hydraulique soient en parfait état : le maître-cylindre à la pédale de frein ne doit pas fuir, ni extérieurement ni intérieurement, sur la pédale ou sur la moquette où le liquide laissera des traces. Toutes les canalisations et tous les raccords vissés doivent être étanches, et en particulier les raccords souples aux roues (le caoutchouc ne doit pas être craquelé ou gonflé par une hernie) Enfin, les cylindres ne devront pas suinter sous les caches poussière en caoutchouc, dans les étriers ou dans les tambours de freins, aux roues.
- Si la voiture est équipée de freins à tambour, il faudra, d’abord régler le jeu des mâchoires au moyen des carrés ou des excentriques. Tournez ceux-ci jusqu’à ce que les garnitures des mâchoires « lèchent » les tambours. N’oubliez pas de régler également le frein à main. Enfin, si votre voiture est équipée d’un répartiteur de freinage (en général, les breaks ou commerciales pouvant transporter une charge élevée à l’arrière), elle devra être posée sur ses roues pendant la purge, car, si les roues arrière sont pendantes, le répartiteur ferme leur circuit hydraulique, rendant celle-ci impossible. S’il s’agit d’un limiteur, la purge se fait normalement.
Les précautions à prendre :
- Lorsque vous pompez sur la pédale de frein, il faut le faire très lentement, en appuyant bien à fond, et en laissant la pédale revenir chaque fois complètement au repos. - Tout en prenant garde à maintenir un niveau correct dans le bocal de frein, pompez jusqu’à ce que le liquide sorte propre et exempt de toute bulle d’air. - Après avoir refermé la vis de purge, complétez le niveau dans le bocal, puis revissez soigneusement le couvercle. Le travail est maintenant terminé, il ne nous reste plus qu’à remettre la roue en place.
11 - Vous aurez besoin d’un bout de tuyau souple et transparent du diamètre des vis de purge et d’un vieux bocal en verre. Munissez-vous de chiffons, car le liquide de frein est très agressif envers la peinture de la carrosserie et agit aussi vite qu’un décapant. Si vous en laissez tomber ne serait-ce qu’une goutte, essuyez-la immédiatement. Enfin et surtout, il faudra demander l’aide d’un ou, mieux, de deux amis. D’autre part, pendant l’opération de purge, il faut à tout moment observer très scrupuleusement toutes les conditions suivantes :
- Le bocal de réservoir du maître-cylindre doit être gardé rempli au moins à moitié, pendant toute la purge, avec du liquide de frein de la marque et conforme à la norme indiquée par le constructeur. La plupart des voitures allemandes, françaises, excepté notamment les Citroën à suspension hydropneumatique, utilisent du liquide de frein « Lockheed » Par contre, les voitures étrangères ont chacune leurs spécifications propres qu’il faut rigoureusement respecter. À défaut de toute indication, utilisez du « Lockheed » 55 universel ou un liquide conforme à la norme DOT 3- SAE J 1703. DOT 4 - SAE 1704. - Norme ISO 4925.
- La séquence des opérations de purge dépend directement du genre de circuit qui est monté sur votre voiture : circuit simple, double, en croix, double avant/arrière. Vous pourrez l’identifier en observant le maître cylindre.
- Ne laissez pas tomber de liquide sur la peinture de la carrosserie : c’est un décapant très efficace.
- NE RÉUTILISEZ JAMAIS le vieux liquide qui sort par les vis de purge. Même s’il semble parfaitement propre, il contient certainement de l’eau.
- Enlevez le tapis, tapis-brosse et moquette qui limite la course libre de la pédale de frein ou d’embrayage.
- Les différents types de circuit :
- Profitez de ce que la voiture est levée pour régler les excentriques de rattrapage de jeu des mâchoires de freins à tambours aux roues arrière.
- Comme indiqué précédemment lors des opérations de purge des freins, il est vivement recommandé de vérifier l’intégralité du circuit. Ici, voici comment contrôler l’état d’une Durit souple de raccordement aux freins avant. Elle ne doit pas être fendillée au niveau du raccord, aussi bien du côté roue que du côté circuit.
- Si l’étrier présente des suintements ou des traces de U gras, il est plus sage de le déposer afin de vérifier l’état du cache-poussière et du joint d’étanchéité du piston. Si lorsque vous soulevez le cache-poussière vous trouvez des traces de liquide de frein, il est indispensable de démonter complètement l’étrier en sortant le piston.
- Ouvrez le capot et repérez le maître cylindre, qui se trouve en regard de la pédale de frein sur le tablier de la cloison pare-feu et qui est surmonté le plus souvent par le bocal de liquide. Si le servofrein n’est pas fixé dessus, c’est le maître cylindre du servo qu’il faut observer. Vous le trouverez en suivant le tuyau partant du maître cylindre de la pédale. Si un seul tuyau en part, il s’agit d’un simple circuit. Si deux tuyaux en partent, c’est un système à double circuit : chacun dessert deux des quatre freins. Il faut suivre chaque tuyau et repérer quelles roues il dessert. Il faudra purger en même temps deux freins un de chaque circuit (de chaque tuyau du maître cylindre) Vous aurez besoin dans ce cas de l’aide de deux amis.
- L’opération de purge :
- Il y a trois façons de réaliser une purge des freins. La première, que l’on va appeler purge à la pédale où il faut deux opérateurs, un qui actionne la pédale de freins et un autre qui ouvre et ferme les purgeurs et les deux autres que l’on va nommer respectivement purge sous pression et purge par aspiration où on aura besoin d’un appareil spécifique mais pas d’un autre opérateur. Dans les trois cas, il faudra avoir sous la main un tube transparent et un récipient propre pour récupérer l’ancien liquide.- Toute intervention sur le circuit hydraulique fera entrer de l'air dans les canalisations entraînant une inefficacité du système de freinage.
Lorsqu’il y a présence d’air dans le circuit de freinage, la pédale est molle et sa course est plus importante que la normale.
C’est pourquoi il faut purger cet air à chaque fois que l’on intervient sur le circuit hydraulique des freins.
- L’ordre de la purge doit se faire sur les roues arrière situées le plus loin du bocal.
- Exemple : Commencer la purge par la roue arrière droite, puis la roue arrière gauche. Ensuite faire la purge à la roue avant droite puis la roue avant gauche.
- A défaut, l’ordre le plus courant est :
1) Arrière gauche.
2) Avant droit.
3) Arrière droit.
4) Avant gauche.
- La purge doit être faite dans l’ordre et de préférence avec le moteur et le contact coupé surtout sur les systèmes avec ABS.- Nettoyez le couvercle et le bocal du maître-cylindre. Ouvrez le couvercle en faisant bien attention à ne pas introduire d’impuretés dans le bocal. Remplissez-le avec du liquide neuf et maintenez-le plein, sinon le circuit va se désamorcer, de l’air va entrer et il faudra refaire la purge.
- En commençant par la roue la plus éloignée du maître cylindre, branchez le tuyau souple transparent sur la vis de purge que vous aurez nettoyée et plongez l’autre extrémité du tuyau dans un peu de liquide au fond du vieux bocal en verre, afin que l’air ne remonte pas dans le circuit lorsque vous relâchez la pédale de frein. Puis, avec une clé plate, ouvrez la vis de purge de deux tours environ. Dans le cas d’un double circuit, purgez deux freins en même temps : un de chaque circuit.
- Purge des freins à la pédale :
- Calez la pédale de frein. Pour ce faire, servez-vous d’un morceau de bois de charpente faisant 100 mm × 25 mm. Vous pouvez aussi employer une cale. L’objectif est d’empêcher la pédale de se rapprocher excessivement du plancher pendant la purge du circuit de freinage. Sinon, le piston du maître-cylindre risque d’aller trop bas et provoquer une fuite interne.
- C’est la façon de faire la plus usuelle mais elle n’est pas sans risque et il faut être deux pour la réaliser. Cette méthode est déconseillée pour les systèmes avec ABS.
Maître cylindre de frein arrive parfois et plus souvent qu’on ne le croit que les coupelles (joints de piston) du maître-cylindre se retournent lorsqu’on appuie sur la pédale et qu’on ouvre un purgeur.
- Quand cela arrive, même après plusieurs purges successives, la pédale de frein reste spongieuse et le freinage inefficace. Votre ami va alors appuyer à fond. Marquer un léger temps d’arrêt, puis relâcher la pédale complètement en soulevant même légèrement le pied, et ainsi de suite jusqu’à ce que du liquide de frein parfaitement propre et clair, et sans bulles microscopiques en suspension, apparaissent dans votre bocal. À chaque roue, lorsque le liquide est clair, fermez la vis de purge pendant que votre ami appuie lentement sur la pédale et non pas lorsqu’elle est relâchée ou en bout de course. Puis répétez l’opération pour les autres roues, toujours en maintenant le niveau dans le bocal du maître cylindre.
- Le retournement des coupelles imposera le remplacement du maître cylindre.
- La procédure de purge à la pédale :
- Appuyer sur la pédale de frein.
- Ouvrir le purgeur.
- Maintenir la pédale en appui à fond de course.
- Fermer le purgeur.
- Relâcher lentement la pédale jusqu’en butée haute.
Répéter l’opération jusqu’à ce que le liquide de frein s’écoule propre et exempt de bulles d’air tout en veillant au maintien du niveau de liquide de frein dans le réservoir.
Répéter cette procédure pour les autres roues dans l’ordre préconisé.
Ajuster le niveau dans le réservoir et remettre en place le bouchon d’origine.
- Si la pédale n’est pas assez ferme, recommencez l’opération en ouvrant la purge lorsque la pédale a déjà commencé d’être enfoncée et en la fermant lorsque la pédale est arrivée au plancher, et ainsi de suite. Vous pouvez également tenter de pomper très vite ou aussi d’enlever le tuyau et de placer votre doigt sur la purge en appuyant légèrement pour faire « clapet » et laisser sortir le liquide en empêchant l’air d’entrer, après avoir bien ouvert les purges. Puis refermez-les.
-------------------
- Manuel de réparation OPEL
- Revenons à nos anciennes Opel des années 1950/1960
- La Purge du circuit sous pression :
(Olympia Rekord, Olympia, Caravan, Fourgonnette de livraison, Kapitän)
1- Emplir le réservoir de l’appareil avec du liquide de frein jusqu’au niveau préconisé, et pomper de l’air dans le réservoir jusqu’à une pression de 1.1/2 à 2 atmosphères, 21 à 28 p.s.i.
2- Nettoyer l’extérieur du réservoir de liquide de la voiture et retirer son bouchon de remplissage.
3- Brancher le tuyau souple du réservoir de pression sur le réservoir de liquide de frein de la voiture en s’assurant bien que le raccord soit parfaitement étanche. Utiliser le raccord souple S-730.
4- Ouvrir lentement la vanne du réservoir sous pression de façon à mettre en pression le circuit de commande des freins.
5- Purger les freins dans l’ordre suivant :
1° Arrière gauche
2° Arrière droit
3° Avant droit
4° Avant gauche
6- Nettoyer la vis de purge puis retirer son capuchon de caoutchouc.
7- Adapter le tuyau de purge sur la vis de purge et laisser plonger l’extrémité libre du tuyau de purge dans un récipient transparent contenant déjà un peu de liquide de frein.
8- Desserrer la vis de purge de ½ tour environ et à laisser l’ouverture jusqu’à ce qu’il n’apparaisse plus aucune bulle d’air à l’extrémité du tuyau de purge et que le liquide s’écoule en un flot régulier et ininterrompu.
- Important :
- Lorsqu’on purge les freins avant, laisser la vis de purge ouverte pendant un temps un peu plus long pour être sûr que l’air qui peut se trouver dans le deuxième cylindre récepteur a le temps de s’évacuer aussi.
9- Fermer la vis de purge, retirer le tuyau de purge et réinstaller le capuchon de caoutchouc de la vis.
10- Purger chacun des freins de roue dans l’ordre indiqué plus haut.
11- Soumettre l’ensemble du circuit de freinage à une pression stable de 2 Kg environ et s’assurer que, dans ces conditions, il n’y a nulle part de fuite de liquide.
12- Débrancher le tuyau souple aboutissant au réservoir de liquide de la voiture et remettre le bouchon de réservoir en place.
-------------------
- Manuel de réparation OPEL
- Purge des freins à la pédale.
(Olympia Rekord, Olympia, Caravan, Fourgonnette de livraison, Kapitän)
1- Contrôler et, si nécessaire, compléter le niveau du liquide de frein, dans le réservoir de la voiture.
2- Effectuer la purge, des freins de roues dans l’ordre suivant :
1° Arrière gauche
2° Arrière droit
3° Avant droit
4° Avant gauche
3- Retirer soigneusement toutes les impuretés qui ont pu s’accumuler autour de la vis de purge, puis retirer le capuchon de caoutchouc de celle-ci.
4- Coiffer la vis de purge avec une extrémité du tuyau plongé dans un récipient de verre.
5- Ouvrir la vis de purge de ½ tour environ. Enfoncer vigoureusement la pédale de frein, la maintenir enfoncée un court instant, et la laisser revenir lentement à sa position de repos. Répéter cette opération de pompage jusqu’à ce que le liquide s’écoule en un flot régulier et ininterrompu à l’extrémité du tuyau de purge. Maintenant alors la pédale enfoncée et resserrer la vis de purge.
6- Retirer le tuyau de purge, et réinstaller à sa place le capuchon de caoutchouc de la vis de purge.
7- Purger successivement chacun des freins de roue en observant l’ordre préconisé.
- Réglage des mâchoires de freins avant :
8- Régler isolément chaque mâchoire de frein par les orifices pratiqués à cet effet dans le plateau de frein. Faire tourner la roue dans le sens de la marche avant, et faire tourner l’excentrique de réglage jusqu’à ce que la garniture vienne toucher le tambour, faire ensuite tourner l’excentrique de réglage en sens inverse jusqu’à ce que le tambour se trouve à nouveau complètement libre de tourner.
- Freins des roues arrière :
9- Le réglage s’effectue de la même façon que pour les freins avant, à la seule exception que chaque excentrique assure à la fois le réglage des deux mâchoires qui comporte le frein de roue.
Course morte de la pédale avant que son poussoir ne vienne toucher le piston du maître cylindre : approx : 5 mm
- Réglage du frein à main :
10- (Olympia Rekord, Olympia, Caravan, Fourgonnette de livraison)- Résistance normale lorsqu’on tire la poignée jusqu’au deuxième cran de la crémaillère.
(Kapitän)
- Résistance normale lorsqu’on tire la poignée jusqu’au quatrième cran de la crémaillère.
- Publicité de la brochure : (1955/1958)
- GENERAL MOTORS CONTINAL Antwerpen
- Pour votre OPEL rien ne vaut les produits d’entretien OPEL
- Liquide de freins Delco Super II with HTD Heavy Duty conçu pour un service intensif, protège la canalisation et organes de freinage. Il conserve toute sa fluidité, même sous basse température.
- Fin de l’extrait du manuel OPEL GM FRANCE
----------------------
- Suite :
- Vérifications finales :
- Si la pédale est bien dure, appuyez très fort dessus pendant deux minutes : la pédale doit rester parfaitement ferme et ne doit absolument pas s’enfoncer vers le plancher. Vous pourrez alors déceler toute fuite dans le circuit par une inspection visuelle détaillée de tous les éléments, tuyauteries rigides, Durits souples (surtout celles des roues avant, et tous les raccords vissés) Si elle ramollit ou qu’elle s’enfonce doucement au plancher quelque chose ne va pas et il est indispensable d’en trouver la cause. NE ROULEZ PAS TANT QUE LA PÉDALE N’EST PAS PARFAITEMENT FERME ET LA COURSE NORMALE ! Enfin, bloquez bien les vis de purge, refaire le niveau dans le bocal. Vous pouvez effectuer un essai sur une route peu fréquentée en regardant bien si personne ne vous suit. Si l’essai n’est pas concluant, recommencez la purge après avoir vérifié le reste du système de frein (plaquettes, garnitures)
- Attention : toutes les opérations concernant les dispositifs de freinage sont très sérieuses et peuvent présenter un grand danger si elles ne sont pas exécutées parfaitement. En cas de doute sur vos compétences, n’hésitez pas à confier votre voiture à un garagiste, surtout si vous n’êtes pas certain de votre travail.
- Purge des freins sous pression
- C’est la façon de procéder qui est préconisée par les constructeurs d’automobiles pour tous les systèmes de freinage et spécialement ceux avec ABS.
- Sur certain véhicule équipé de l’ABS, il peut être, en plus, obligatoire de connecter une valise de diagnostic au calculateur ABS s’il dispose d’un programme spécifique pour purger les électrovannes.
- Le principe de cette méthode est d’envoyer du liquide de frein sous pression par le bouchon du bocal pour le pousser jusqu’aux purgeurs.
- La pression conseillée est d’environ 1.5 bars sans jamais dépasser 2 bars au maximum.
- Appareil purge freins sous pression : Pour purger sous pression, les professionnels se servent d’une station de purge, manuelle ou automatique, mais cet outillage onéreux n’a aucun intérêt pour un particulier qui ne s’en servira qu’occasionnellement.
- Heureusement, il existe sur le marché, un petit appareil de purge très pratique et abordable pour un particulier qui se sert de la pression d’une roue, la roue de secours est l’idéal, pour pressuriser le bocal de frein.
- Cet appareil est livré avec plusieurs bouchons de bocal pour les véhicules les plus courant mais qui ne conviendrons pas pour tous les véhicules.
- Si aucun bouchon ne convient pour votre véhicule, la solution est de vous procurez un deuxième bouchon d’origine (neuf ou d’occasion), de le percer au centre et de placer une valve de pneu dans l’orifice.
- Procédure de purge des freins sous pression
- Remplir l’appareil de liquide de frein neuf.
- Mettre en place le bouchon adapté sur le bocal et connecter le tuyau de l’appareil.
- Mettre l’appareil sous pression.
- Ouvrir un par un chaque purgeur dans l’ordre préconisé jusqu’à ce que le liquide de frein s’écoule propre et exempt de bulles d’air.
- Ajuster le niveau dans le réservoir et remettre en place le bouchon d’origine.
- Purge des freins par aspiration
- Appareil purge freins par aspiration :Comme pour la méthode sous pression, la purge par aspiration nécessite un appareillage spécifique.
- Le principe de cette méthode et de créer une dépression par le purgeur pour aspirer le liquide. Cette dépression peut être créée avec une pompe manuelle ou par vacuum avec de l’air comprimé (nécessite un compresseur).
- Pour un particulier, cet appareil à pompe manuelle semble être un bon compromis entre prix et facilité d’utilisation.
- Procédure de purge des freins par aspiration
- Brancher le tuyau au purgeur.
- Créer la dépression sur l’appareil.
- Ouvrir le purgeur jusqu’à ce que le liquide de frein s’écoule propre et exempt de bulles d’air tout en veillant au maintien du niveau de liquide de frein dans le réservoir.
- Resserrez la vis de purge à la fin de l’écoulement. Il suffit de la tourner d’un quart de tour, mais vers la droite, pour la fermer et empêcher toute entrée d’air dans le circuit lorsque le frein sera relâché - Fermer le purgeur.
- Répéter cette procédure pour les autres roues dans l’ordre préconisé.
- Ajuster le niveau dans le réservoir et remettre en place le bouchon d’origine.
- Répétez l’opération. Vous devrez le faire autant de fois que nécessaire. Le but est d’obtenir un écoulement de fluide propre à l’autre extrémité du tube de purge. Généralement, il suffit d’ajouter du fluide neuf dans le réservoir 5 ou 6 fois par cycle. Ne laissez jamais le niveau tomber trop bas dans le réservoir, sinon vous risquez d’avoir une entrée d’air dans le maître-cylindre.
- Protection de l’environnement :
- Le liquide de frein est très nocif pour l’environnement. Il est donc obligatoire de le recycler à la déchetterie ou chez un réparateur professionnel.
- Les accessoires de purges depuis 22 Euros.
- Les accessoires de purges avec manomètre depuis 50 Euros.
- Les accessoires de purges de frein pneumatique, air comprimé, avec différents adaptateurs, depuis 100 Euros.
- Liquide de frein : de 4 Euros à 16 Euros.
- Liquide de frein universel ENV6 Bosch 1 L remplace le DOT 3, 4, 5.1 : 16,35 Euros le litre.
- Liquide de frein Bendix (55) = DOT 3
- J’ai acheté récemment un :
OBD2 Stylo Testeur Test Liquide de Frein Voiture Diagnostic 5 LED
- Vérification simple et rapide de la qualité du liquide de frein.
- Ce testeur identifie le pourcentage d'eau dans le liquide de frein.
- Insérez le testeur dans le réservoir pendant une seconde, le résultat du test s'affiche immédiatement par LED.
Le testeur s’éteindra automatiquement après 12 secondes d'inactivité.
- Un outil indispensable pour votre sécurité : une manière simple et rapide de vérifier la qualité du liquide de frein.
- Fonctionne pour du liquide DOT3, DOT4 et DOT5.1.
- Alimentation: 1.5 V Pile "AAA" (Pile non incluse)
- Ne fonctionne pas pour le liquide DOT5 à base de silicone.
- Fonctionnement LED :
Le vert = teneur en eau dans le liquide de frein H2O < 1.5%, liquide de frein qualifié : OK
Le jaune = liquide de frein à faible teneur en eau H2O = 1.5% à 3%, peut continuer à être utilisé, testez à nouveau six mois plus tard – 2 LED jaune OK
Le rouge = teneur en eau dans le liquide de frein H2O > 3%, ne peut pas continuer à être utilisé, le liquide de frein doit être remplacé. - 1 LED rouge H2O > 3%, une 2e LED rouge H2O > 4%
- Avec ce testeur j’ai put comparer le niveau de l’eau dans le liquide de frein. Surprise sur une voiture qui avait un taux élevé en eau. 1 LED rouge allumée = H2O > 3%
- Facile d'utilisation, un rinçage avant rangement et votre outil peut être réutilisé !
- Prix : Stylo testeur en vente depuis 6 Euros … (sauf DOT 5)
: Testeur de liquide de frein numérique : + de 20 Euros (sauf DOT 5)
- Pour les PROS :
- Testeur de liquide de frein Facom LCD : 512 Euros (sauf DOT 5) - Testeur de liquide de frein ATE : 750 Euros (sauf DOT 5)
- KS TOOLS 150.2198 Testeur de liquide de frein digital avec imprimante : 1365 Euros (sauf DOT 5)
- Le DOT 3 point d’ébullition : 220°C
- Le DOT 4 point d’ébullition : 240°C
- Le DOT 5.1 a un point humide d'ébullition d'environ 185 ° De plus le DOT 5.1 est deux fois moins visqueux que le DOT 4. En pratique, cela signifie qu'un système de freinage utilisant du DOT 5.1 aura un temps de réponse plus rapide, une meilleure modulation de freinage et une rétraction plus rapide des plaquettes. Le DOT 3, 4, 5.1 : Il s'agit d'une huile synthétique, à base de polyglycols.
- Bases les plus répandues, on y trouve les DOT 3, DOT 4, DOT 5.1. Ce sont des fluides de couleur ambre, qui présentent l'avantage d'être miscibles entre eux, et de ne pas être corrosifs pour les joints caoutchouc des étriers et des cylindres de frein. Ils sont généralement à base de glycol.
- DOT 5 liquide de freinage et d’embrayage à base de silicone. Le liquide de frein à base de silicone TRW DOT 5 permet une puissance de freinage optimale et garantie, produit de haute performance.
Spécialement recommandé pour les véhicules de collection et de compétition.
- Tout véhicule susceptible d'affronter des taux d'humidité importants.
- LIQUIDE DE FREIN DOT 5 SILICONE a pour propriétés :
- Insensible à l'humidité.
- Non miscible aux liquides de freins synthétiques (DOT 4 et DOT 5.1) et minéraux (LHM)
- Excellente compatibilité avec les joints et matières plastiques présents dans les circuits de freinage.
- Il n’endommage pas la peinture ni les surfaces imprimées.
- Point d’ébullition : 260°C
- Ne pas utiliser avec les systèmes fonctionnant d’origine avec des liquides à base minérale. Il est préférable de changer tous les joints du circuit de freinage lors du passage au DOT 5 silicone.
- Les dénominations DOT 5 et DOT 5.1 prêtent à équivoque. Il est impératif de ne jamais mélanger du DOT 5 (silicone) ou du DOT 2 avec les autres types, car il y a risque de détérioration des joints. Couleur violette.
Prix : 40 à 58 Euros le litre. Made in USA.
- Bases minérales :
- Elles sont réservées à certains modèles spécifiques de véhicules :
Citroën LHM et Rolls-Royce, le LHS Citroën dans les DS19 et ID, etc. … rouges ou verts. - Ces produits sont strictement réservés à quelques voitures (équipées de centrales hydrauliques) et ne sont pas miscibles avec d’autres liquides de freins. - Les liquides de freins sont classés en différentes catégories, spécifiées par le Department Of Transportation américain (d’où le sigle DOT utilisé)
- Bases synthétiques :
- Bases les plus répandues, on y trouve les DOT 3, DOT 4, DOT 5.1. Ce sont des fluides de couleur ambre, qui présentent l'avantage d'être miscibles entre eux, et de ne pas être corrosifs pour les joints caoutchouc des étriers et des cylindres de frein. Ils sont généralement à base de glycol.
- Bases silicone :
- Concerne le DOT 5. Les bases silicone présentent l'avantage d'être hydrophobes et donc d'être moins concernées par les problèmes de vieillissement.
Les dénominations DOT 5 et DOT 5.1 prêtent à équivoque. Il est impératif de ne jamais mélanger du DOT 5 (silicone) ou du DOT 2 avec les autres types, car il y a risque de détérioration des joints. Le liquide DOT 5.1 est normalement réservé à certains usages (compétition, contraintes thermiques élevées, etc.). Le liquide DOT 5 a cependant l'avantage de ne pas absorber d'humidité, ce pourquoi on l'utilise souvent aussi avec des joints adaptés dans les véhicules de collection qui ne roulent que rarement. L'appellation DOT 5.1 peut-être trompeuse par rapport aux qualités du DOT 4+ aussi appelé Super DOT 4 ou DOT 4 ESP. En effet, le tableau montre les caractéristiques qualitatives supérieures de ce dernier contrairement à ce que la numérotation pourrait suggérer. On constate que ce liquide est deux fois moins visqueux que le simple DOT 4.
- Utilisation du DOT 4 +
- Fluide destiné aux circuits de freins à disque ou à tambour ainsi qu’à la plupart des systèmes
d’embrayages des véhicules.
- Il convient aux régimes sévères d’utilisations (freins à disque atteignant des températures
élevées) et est particulièrement recommandé pour les véhicules équipés de systèmes
d’assistance de conduite tels que ESP (programme de stabilisation électronique), l’EBS
(système de freinage électronique), l’ABS (système antiblocage), l’ARS (accélération anti- dérapage),…destiné à améliorer le contrôle de trajectoire des véhicules automobiles et à
améliorer la sécurité routière.
- Propriétés et avantages :
- Haut point d’ébullition, évitant la formation de tampons de vapeur (« vapor lock ») dans
les circuits lors de l’utilisation intensive des freins.
- Faible viscosité à basse température pour une parfaite compatibilité avec les systèmes
d’assistance de conduite. Miscible à tous les autres liquides de freins DOT 5.1, DOT 4 et DOT 3. Compatible avec les différents types de joints et matériaux utilisés dans les circuits de
freinage et modulateurs hydrauliques. Haut pouvoir anticorrosion répondant aux exigences les plus sévères.
- Précautions d’emploi :
- Ne convient pas pour les circuits recommandant l’emploi d’un liquide hydraulique
minérale ou l’emploi d’un liquide de frein siliconé (norme DOT 5)
Voici quelques caractéristiques des principaux liquides de frein :
DOT 3 Norme ISO 4925 : grade 3 Viscosité cinématique maximale à −40 °C (en mm2 s−1) = 1500 - Température d'ébullition = 205° C - Température d'ébullition avec 3,7 % d'eau 140° C
DOT 4 Norme ISO 4925 : grade 4 Viscosité cinématique maximale à −40 °C (en mm2 s−1) = 1800 - Température d'ébullition = 230° C - Température d'ébullition avec 3,7 % d'eau 155° C
DOT 5 Norme ISO 4925 : grade 5 Viscosité cinématique maximale à −40 °C (en mm2 s−1) = < 700 - Température d'ébullition = 260° C - Température d'ébullition avec 3,7 % d'eau 185° C
DOT 5.1 Norme ISO 4925 : grade 5.1 Viscosité cinématique maximale à −40 °C (en mm2 s−1) = 900 - Température d'ébullition = 270° C - Température d'ébullition avec 3,7 % d'eau 191° C
DOT 4 + Norme ISO 4925 : grade 6 Viscosité cinématique maximale à −40 °C (en mm2 s−1) = 750 - Température d'ébullition = 300° C - Température d'ébullition avec 3,7 % d'eau 195° C
- Un circuit hydraulique mal purgé est beaucoup moins efficace qu’à la normale. À l’échauffement, il peut devenir totalement inopérant. Dans le cas du circuit d’embrayage, c’est très désagréable, mais, dans celui du circuit de freins, c’est bien sûr très dangereux.
- Il faut purger le circuit hydraulique pour deux raisons essentielles tout d’abord, si l’on vient d’effectuer des travaux sur la partie hydraulique, il y aura des bulles d’air qui auront pénétré dans le liquide. Or l’air est compressible alors que la qualité principale demandée à un liquide est justement de ne pas l’être. Il faut donc éliminer ces bulles d’air. D’autre part, le liquide de frein est avide d’humidité, et, avec le temps, il finit par contenir de l’eau en quantité suffisante pour faire rouiller les parties métalliques des pistons et des cylindres en contact avec ce liquide.
- De plus, et toujours du fait du vieillissement, il bout plus facilement, sous l’effet de la grande quantité de chaleur dégagée par les freins, d’autant plus que la présence d’eau facilite ce phénomène. En effet, un bon liquide de frein bout entre 180 et 280 degrés. Le bouillonnement dégage de l’air et rend le liquide compressible, élastique. La pédale de frein ou d’embrayage devient alors mol et « spongieuse » À la limite, en cas de fort échauffement, elle peut devenir complètement inefficace en conduite sportive, par exemple. Il faudra donc purger le circuit hydraulique de freins régulièrement tous les deux ans ou tous les 20.000 km au moins, par mesure de sécurité.
- Après avoir serré le frein à main, desserrez les écrous de roue à l’aide d’une croix, montez la voiture sur cric, puis dévissez complètement les écrous de roue.
- Retirez la roue, puis enfilez le tuyau de purge en plastique transparent sur la vis de purge. - - - Desserrez ensuite la vis de purge à l’aide d’une clé appropriée.
- Placez un récipient en verre sous le tuyau de purge, puis demandez à votre aide, de pomper très lentement sur la pédale de frein pour chasser l’air contenu en suspension dans le vieux Lockheed. Faites pomper jusqu’à ce que le bocal se soit vidé entièrement du liquide de frein usagé (reconnaissable à sa couleur noire)
- Le Lockheed se charge d’humidité avec l’âge, et est alors dangereux pour votre circuit de freinage, car il fait alors rouiller l’intérieur des cylindres de roue. Ici, nous voyons clairement l’émulsion formée par le mélange Lockheed/eau/air. Notons, qu’il ne faut sous aucun prétexte réutiliser le vieux Lockheed.
- Vérifications préliminaires :
- Le bocal étant vide, nettoyez-en le fond à l’aide d’un chiffon propre. Sur cette voiture, le circuit de frein étant double, le bocal possède un double réservoir.
- Sur cette voiture n’ayant qu’un simple circuit, le bocal de Lockheed est plus simple à nettoyer. Notons qu’ici, le maître cylindre est directement accolé au servo.
- Une fois le bocal nettoyé, remplissez-le de nouveau avec du Lockheed neuf. Faites très attention de ne pas renverser de liquide sur la carrosserie, car ce dernier attaque la peinture. Ne dépassez pas le repère « maxi »
- Avant d’effectuer la purge elle-même, il y a un certain nombre de précautions à prendre. Tout d’abord, il faut bien évidemment que tous les éléments du circuit hydraulique soient en parfait état : le maître-cylindre à la pédale de frein ne doit pas fuir, ni extérieurement ni intérieurement, sur la pédale ou sur la moquette où le liquide laissera des traces. Toutes les canalisations et tous les raccords vissés doivent être étanches, et en particulier les raccords souples aux roues (le caoutchouc ne doit pas être craquelé ou gonflé par une hernie) Enfin, les cylindres ne devront pas suinter sous les caches poussière en caoutchouc, dans les étriers ou dans les tambours de freins, aux roues.
- Si la voiture est équipée de freins à tambour, il faudra, d’abord régler le jeu des mâchoires au moyen des carrés ou des excentriques. Tournez ceux-ci jusqu’à ce que les garnitures des mâchoires « lèchent » les tambours. N’oubliez pas de régler également le frein à main. Enfin, si votre voiture est équipée d’un répartiteur de freinage (en général, les breaks ou commerciales pouvant transporter une charge élevée à l’arrière), elle devra être posée sur ses roues pendant la purge, car, si les roues arrière sont pendantes, le répartiteur ferme leur circuit hydraulique, rendant celle-ci impossible. S’il s’agit d’un limiteur, la purge se fait normalement.
Les précautions à prendre :
- Lorsque vous pompez sur la pédale de frein, il faut le faire très lentement, en appuyant bien à fond, et en laissant la pédale revenir chaque fois complètement au repos. - Tout en prenant garde à maintenir un niveau correct dans le bocal de frein, pompez jusqu’à ce que le liquide sorte propre et exempt de toute bulle d’air. - Après avoir refermé la vis de purge, complétez le niveau dans le bocal, puis revissez soigneusement le couvercle. Le travail est maintenant terminé, il ne nous reste plus qu’à remettre la roue en place.
11 - Vous aurez besoin d’un bout de tuyau souple et transparent du diamètre des vis de purge et d’un vieux bocal en verre. Munissez-vous de chiffons, car le liquide de frein est très agressif envers la peinture de la carrosserie et agit aussi vite qu’un décapant. Si vous en laissez tomber ne serait-ce qu’une goutte, essuyez-la immédiatement. Enfin et surtout, il faudra demander l’aide d’un ou, mieux, de deux amis. D’autre part, pendant l’opération de purge, il faut à tout moment observer très scrupuleusement toutes les conditions suivantes :
- Le bocal de réservoir du maître-cylindre doit être gardé rempli au moins à moitié, pendant toute la purge, avec du liquide de frein de la marque et conforme à la norme indiquée par le constructeur. La plupart des voitures allemandes, françaises, excepté notamment les Citroën à suspension hydropneumatique, utilisent du liquide de frein « Lockheed » Par contre, les voitures étrangères ont chacune leurs spécifications propres qu’il faut rigoureusement respecter. À défaut de toute indication, utilisez du « Lockheed » 55 universel ou un liquide conforme à la norme DOT 3- SAE J 1703. DOT 4 - SAE 1704. - Norme ISO 4925.
- La séquence des opérations de purge dépend directement du genre de circuit qui est monté sur votre voiture : circuit simple, double, en croix, double avant/arrière. Vous pourrez l’identifier en observant le maître cylindre.
- Ne laissez pas tomber de liquide sur la peinture de la carrosserie : c’est un décapant très efficace.
- NE RÉUTILISEZ JAMAIS le vieux liquide qui sort par les vis de purge. Même s’il semble parfaitement propre, il contient certainement de l’eau.
- Enlevez le tapis, tapis-brosse et moquette qui limite la course libre de la pédale de frein ou d’embrayage.
- Les différents types de circuit :
- Profitez de ce que la voiture est levée pour régler les excentriques de rattrapage de jeu des mâchoires de freins à tambours aux roues arrière.
- Comme indiqué précédemment lors des opérations de purge des freins, il est vivement recommandé de vérifier l’intégralité du circuit. Ici, voici comment contrôler l’état d’une Durit souple de raccordement aux freins avant. Elle ne doit pas être fendillée au niveau du raccord, aussi bien du côté roue que du côté circuit.
- Si l’étrier présente des suintements ou des traces de U gras, il est plus sage de le déposer afin de vérifier l’état du cache-poussière et du joint d’étanchéité du piston. Si lorsque vous soulevez le cache-poussière vous trouvez des traces de liquide de frein, il est indispensable de démonter complètement l’étrier en sortant le piston.
- Ouvrez le capot et repérez le maître cylindre, qui se trouve en regard de la pédale de frein sur le tablier de la cloison pare-feu et qui est surmonté le plus souvent par le bocal de liquide. Si le servofrein n’est pas fixé dessus, c’est le maître cylindre du servo qu’il faut observer. Vous le trouverez en suivant le tuyau partant du maître cylindre de la pédale. Si un seul tuyau en part, il s’agit d’un simple circuit. Si deux tuyaux en partent, c’est un système à double circuit : chacun dessert deux des quatre freins. Il faut suivre chaque tuyau et repérer quelles roues il dessert. Il faudra purger en même temps deux freins un de chaque circuit (de chaque tuyau du maître cylindre) Vous aurez besoin dans ce cas de l’aide de deux amis.
- L’opération de purge :
- Il y a trois façons de réaliser une purge des freins. La première, que l’on va appeler purge à la pédale où il faut deux opérateurs, un qui actionne la pédale de freins et un autre qui ouvre et ferme les purgeurs et les deux autres que l’on va nommer respectivement purge sous pression et purge par aspiration où on aura besoin d’un appareil spécifique mais pas d’un autre opérateur. Dans les trois cas, il faudra avoir sous la main un tube transparent et un récipient propre pour récupérer l’ancien liquide.- Toute intervention sur le circuit hydraulique fera entrer de l'air dans les canalisations entraînant une inefficacité du système de freinage.
Lorsqu’il y a présence d’air dans le circuit de freinage, la pédale est molle et sa course est plus importante que la normale.
C’est pourquoi il faut purger cet air à chaque fois que l’on intervient sur le circuit hydraulique des freins.
- L’ordre de la purge doit se faire sur les roues arrière situées le plus loin du bocal.
- Exemple : Commencer la purge par la roue arrière droite, puis la roue arrière gauche. Ensuite faire la purge à la roue avant droite puis la roue avant gauche.
- A défaut, l’ordre le plus courant est :
1) Arrière gauche.
2) Avant droit.
3) Arrière droit.
4) Avant gauche.
- La purge doit être faite dans l’ordre et de préférence avec le moteur et le contact coupé surtout sur les systèmes avec ABS.- Nettoyez le couvercle et le bocal du maître-cylindre. Ouvrez le couvercle en faisant bien attention à ne pas introduire d’impuretés dans le bocal. Remplissez-le avec du liquide neuf et maintenez-le plein, sinon le circuit va se désamorcer, de l’air va entrer et il faudra refaire la purge.
- En commençant par la roue la plus éloignée du maître cylindre, branchez le tuyau souple transparent sur la vis de purge que vous aurez nettoyée et plongez l’autre extrémité du tuyau dans un peu de liquide au fond du vieux bocal en verre, afin que l’air ne remonte pas dans le circuit lorsque vous relâchez la pédale de frein. Puis, avec une clé plate, ouvrez la vis de purge de deux tours environ. Dans le cas d’un double circuit, purgez deux freins en même temps : un de chaque circuit.
- Purge des freins à la pédale :
- Calez la pédale de frein. Pour ce faire, servez-vous d’un morceau de bois de charpente faisant 100 mm × 25 mm. Vous pouvez aussi employer une cale. L’objectif est d’empêcher la pédale de se rapprocher excessivement du plancher pendant la purge du circuit de freinage. Sinon, le piston du maître-cylindre risque d’aller trop bas et provoquer une fuite interne.
- C’est la façon de faire la plus usuelle mais elle n’est pas sans risque et il faut être deux pour la réaliser. Cette méthode est déconseillée pour les systèmes avec ABS.
Maître cylindre de frein arrive parfois et plus souvent qu’on ne le croit que les coupelles (joints de piston) du maître-cylindre se retournent lorsqu’on appuie sur la pédale et qu’on ouvre un purgeur.
- Quand cela arrive, même après plusieurs purges successives, la pédale de frein reste spongieuse et le freinage inefficace. Votre ami va alors appuyer à fond. Marquer un léger temps d’arrêt, puis relâcher la pédale complètement en soulevant même légèrement le pied, et ainsi de suite jusqu’à ce que du liquide de frein parfaitement propre et clair, et sans bulles microscopiques en suspension, apparaissent dans votre bocal. À chaque roue, lorsque le liquide est clair, fermez la vis de purge pendant que votre ami appuie lentement sur la pédale et non pas lorsqu’elle est relâchée ou en bout de course. Puis répétez l’opération pour les autres roues, toujours en maintenant le niveau dans le bocal du maître cylindre.
- Le retournement des coupelles imposera le remplacement du maître cylindre.
- La procédure de purge à la pédale :
- Appuyer sur la pédale de frein.
- Ouvrir le purgeur.
- Maintenir la pédale en appui à fond de course.
- Fermer le purgeur.
- Relâcher lentement la pédale jusqu’en butée haute.
Répéter l’opération jusqu’à ce que le liquide de frein s’écoule propre et exempt de bulles d’air tout en veillant au maintien du niveau de liquide de frein dans le réservoir.
Répéter cette procédure pour les autres roues dans l’ordre préconisé.
Ajuster le niveau dans le réservoir et remettre en place le bouchon d’origine.
- Si la pédale n’est pas assez ferme, recommencez l’opération en ouvrant la purge lorsque la pédale a déjà commencé d’être enfoncée et en la fermant lorsque la pédale est arrivée au plancher, et ainsi de suite. Vous pouvez également tenter de pomper très vite ou aussi d’enlever le tuyau et de placer votre doigt sur la purge en appuyant légèrement pour faire « clapet » et laisser sortir le liquide en empêchant l’air d’entrer, après avoir bien ouvert les purges. Puis refermez-les.
-------------------
- Manuel de réparation OPEL
- Revenons à nos anciennes Opel des années 1950/1960
- La Purge du circuit sous pression :
(Olympia Rekord, Olympia, Caravan, Fourgonnette de livraison, Kapitän)
1- Emplir le réservoir de l’appareil avec du liquide de frein jusqu’au niveau préconisé, et pomper de l’air dans le réservoir jusqu’à une pression de 1.1/2 à 2 atmosphères, 21 à 28 p.s.i.
2- Nettoyer l’extérieur du réservoir de liquide de la voiture et retirer son bouchon de remplissage.
3- Brancher le tuyau souple du réservoir de pression sur le réservoir de liquide de frein de la voiture en s’assurant bien que le raccord soit parfaitement étanche. Utiliser le raccord souple S-730.
4- Ouvrir lentement la vanne du réservoir sous pression de façon à mettre en pression le circuit de commande des freins.
5- Purger les freins dans l’ordre suivant :
1° Arrière gauche
2° Arrière droit
3° Avant droit
4° Avant gauche
6- Nettoyer la vis de purge puis retirer son capuchon de caoutchouc.
7- Adapter le tuyau de purge sur la vis de purge et laisser plonger l’extrémité libre du tuyau de purge dans un récipient transparent contenant déjà un peu de liquide de frein.
8- Desserrer la vis de purge de ½ tour environ et à laisser l’ouverture jusqu’à ce qu’il n’apparaisse plus aucune bulle d’air à l’extrémité du tuyau de purge et que le liquide s’écoule en un flot régulier et ininterrompu.
- Important :
- Lorsqu’on purge les freins avant, laisser la vis de purge ouverte pendant un temps un peu plus long pour être sûr que l’air qui peut se trouver dans le deuxième cylindre récepteur a le temps de s’évacuer aussi.
9- Fermer la vis de purge, retirer le tuyau de purge et réinstaller le capuchon de caoutchouc de la vis.
10- Purger chacun des freins de roue dans l’ordre indiqué plus haut.
11- Soumettre l’ensemble du circuit de freinage à une pression stable de 2 Kg environ et s’assurer que, dans ces conditions, il n’y a nulle part de fuite de liquide.
12- Débrancher le tuyau souple aboutissant au réservoir de liquide de la voiture et remettre le bouchon de réservoir en place.
-------------------
- Manuel de réparation OPEL
- Purge des freins à la pédale.
(Olympia Rekord, Olympia, Caravan, Fourgonnette de livraison, Kapitän)
1- Contrôler et, si nécessaire, compléter le niveau du liquide de frein, dans le réservoir de la voiture.
2- Effectuer la purge, des freins de roues dans l’ordre suivant :
1° Arrière gauche
2° Arrière droit
3° Avant droit
4° Avant gauche
3- Retirer soigneusement toutes les impuretés qui ont pu s’accumuler autour de la vis de purge, puis retirer le capuchon de caoutchouc de celle-ci.
4- Coiffer la vis de purge avec une extrémité du tuyau plongé dans un récipient de verre.
5- Ouvrir la vis de purge de ½ tour environ. Enfoncer vigoureusement la pédale de frein, la maintenir enfoncée un court instant, et la laisser revenir lentement à sa position de repos. Répéter cette opération de pompage jusqu’à ce que le liquide s’écoule en un flot régulier et ininterrompu à l’extrémité du tuyau de purge. Maintenant alors la pédale enfoncée et resserrer la vis de purge.
6- Retirer le tuyau de purge, et réinstaller à sa place le capuchon de caoutchouc de la vis de purge.
7- Purger successivement chacun des freins de roue en observant l’ordre préconisé.
- Réglage des mâchoires de freins avant :
8- Régler isolément chaque mâchoire de frein par les orifices pratiqués à cet effet dans le plateau de frein. Faire tourner la roue dans le sens de la marche avant, et faire tourner l’excentrique de réglage jusqu’à ce que la garniture vienne toucher le tambour, faire ensuite tourner l’excentrique de réglage en sens inverse jusqu’à ce que le tambour se trouve à nouveau complètement libre de tourner.
- Freins des roues arrière :
9- Le réglage s’effectue de la même façon que pour les freins avant, à la seule exception que chaque excentrique assure à la fois le réglage des deux mâchoires qui comporte le frein de roue.
Course morte de la pédale avant que son poussoir ne vienne toucher le piston du maître cylindre : approx : 5 mm
- Réglage du frein à main :
10- (Olympia Rekord, Olympia, Caravan, Fourgonnette de livraison)- Résistance normale lorsqu’on tire la poignée jusqu’au deuxième cran de la crémaillère.
(Kapitän)
- Résistance normale lorsqu’on tire la poignée jusqu’au quatrième cran de la crémaillère.
- Publicité de la brochure : (1955/1958)
- GENERAL MOTORS CONTINAL Antwerpen
- Pour votre OPEL rien ne vaut les produits d’entretien OPEL
- Liquide de freins Delco Super II with HTD Heavy Duty conçu pour un service intensif, protège la canalisation et organes de freinage. Il conserve toute sa fluidité, même sous basse température.
- Fin de l’extrait du manuel OPEL GM FRANCE
----------------------
- Suite :
- Vérifications finales :
- Si la pédale est bien dure, appuyez très fort dessus pendant deux minutes : la pédale doit rester parfaitement ferme et ne doit absolument pas s’enfoncer vers le plancher. Vous pourrez alors déceler toute fuite dans le circuit par une inspection visuelle détaillée de tous les éléments, tuyauteries rigides, Durits souples (surtout celles des roues avant, et tous les raccords vissés) Si elle ramollit ou qu’elle s’enfonce doucement au plancher quelque chose ne va pas et il est indispensable d’en trouver la cause. NE ROULEZ PAS TANT QUE LA PÉDALE N’EST PAS PARFAITEMENT FERME ET LA COURSE NORMALE ! Enfin, bloquez bien les vis de purge, refaire le niveau dans le bocal. Vous pouvez effectuer un essai sur une route peu fréquentée en regardant bien si personne ne vous suit. Si l’essai n’est pas concluant, recommencez la purge après avoir vérifié le reste du système de frein (plaquettes, garnitures)
- Attention : toutes les opérations concernant les dispositifs de freinage sont très sérieuses et peuvent présenter un grand danger si elles ne sont pas exécutées parfaitement. En cas de doute sur vos compétences, n’hésitez pas à confier votre voiture à un garagiste, surtout si vous n’êtes pas certain de votre travail.
- Purge des freins sous pression
- C’est la façon de procéder qui est préconisée par les constructeurs d’automobiles pour tous les systèmes de freinage et spécialement ceux avec ABS.
- Sur certain véhicule équipé de l’ABS, il peut être, en plus, obligatoire de connecter une valise de diagnostic au calculateur ABS s’il dispose d’un programme spécifique pour purger les électrovannes.
- Le principe de cette méthode est d’envoyer du liquide de frein sous pression par le bouchon du bocal pour le pousser jusqu’aux purgeurs.
- La pression conseillée est d’environ 1.5 bars sans jamais dépasser 2 bars au maximum.
- Appareil purge freins sous pression : Pour purger sous pression, les professionnels se servent d’une station de purge, manuelle ou automatique, mais cet outillage onéreux n’a aucun intérêt pour un particulier qui ne s’en servira qu’occasionnellement.
- Heureusement, il existe sur le marché, un petit appareil de purge très pratique et abordable pour un particulier qui se sert de la pression d’une roue, la roue de secours est l’idéal, pour pressuriser le bocal de frein.
- Cet appareil est livré avec plusieurs bouchons de bocal pour les véhicules les plus courant mais qui ne conviendrons pas pour tous les véhicules.
- Si aucun bouchon ne convient pour votre véhicule, la solution est de vous procurez un deuxième bouchon d’origine (neuf ou d’occasion), de le percer au centre et de placer une valve de pneu dans l’orifice.
- Procédure de purge des freins sous pression
- Remplir l’appareil de liquide de frein neuf.
- Mettre en place le bouchon adapté sur le bocal et connecter le tuyau de l’appareil.
- Mettre l’appareil sous pression.
- Ouvrir un par un chaque purgeur dans l’ordre préconisé jusqu’à ce que le liquide de frein s’écoule propre et exempt de bulles d’air.
- Ajuster le niveau dans le réservoir et remettre en place le bouchon d’origine.
- Purge des freins par aspiration
- Appareil purge freins par aspiration :Comme pour la méthode sous pression, la purge par aspiration nécessite un appareillage spécifique.
- Le principe de cette méthode et de créer une dépression par le purgeur pour aspirer le liquide. Cette dépression peut être créée avec une pompe manuelle ou par vacuum avec de l’air comprimé (nécessite un compresseur).
- Pour un particulier, cet appareil à pompe manuelle semble être un bon compromis entre prix et facilité d’utilisation.
- Procédure de purge des freins par aspiration
- Brancher le tuyau au purgeur.
- Créer la dépression sur l’appareil.
- Ouvrir le purgeur jusqu’à ce que le liquide de frein s’écoule propre et exempt de bulles d’air tout en veillant au maintien du niveau de liquide de frein dans le réservoir.
- Resserrez la vis de purge à la fin de l’écoulement. Il suffit de la tourner d’un quart de tour, mais vers la droite, pour la fermer et empêcher toute entrée d’air dans le circuit lorsque le frein sera relâché - Fermer le purgeur.
- Répéter cette procédure pour les autres roues dans l’ordre préconisé.
- Ajuster le niveau dans le réservoir et remettre en place le bouchon d’origine.
- Répétez l’opération. Vous devrez le faire autant de fois que nécessaire. Le but est d’obtenir un écoulement de fluide propre à l’autre extrémité du tube de purge. Généralement, il suffit d’ajouter du fluide neuf dans le réservoir 5 ou 6 fois par cycle. Ne laissez jamais le niveau tomber trop bas dans le réservoir, sinon vous risquez d’avoir une entrée d’air dans le maître-cylindre.
- Protection de l’environnement :
- Le liquide de frein est très nocif pour l’environnement. Il est donc obligatoire de le recycler à la déchetterie ou chez un réparateur professionnel.
- Les accessoires de purges depuis 22 Euros.
- Les accessoires de purges avec manomètre depuis 50 Euros.
- Les accessoires de purges de frein pneumatique, air comprimé, avec différents adaptateurs, depuis 100 Euros.
- Liquide de frein : de 4 Euros à 16 Euros.
- Liquide de frein universel ENV6 Bosch 1 L remplace le DOT 3, 4, 5.1 : 16,35 Euros le litre.
- Liquide de frein Bendix (55) = DOT 3
- J’ai acheté récemment un :
OBD2 Stylo Testeur Test Liquide de Frein Voiture Diagnostic 5 LED
- Vérification simple et rapide de la qualité du liquide de frein.
- Ce testeur identifie le pourcentage d'eau dans le liquide de frein.
- Insérez le testeur dans le réservoir pendant une seconde, le résultat du test s'affiche immédiatement par LED.
Le testeur s’éteindra automatiquement après 12 secondes d'inactivité.
- Un outil indispensable pour votre sécurité : une manière simple et rapide de vérifier la qualité du liquide de frein.
- Fonctionne pour du liquide DOT3, DOT4 et DOT5.1.
- Alimentation: 1.5 V Pile "AAA" (Pile non incluse)
- Ne fonctionne pas pour le liquide DOT5 à base de silicone.
- Fonctionnement LED :
Le vert = teneur en eau dans le liquide de frein H2O < 1.5%, liquide de frein qualifié : OK
Le jaune = liquide de frein à faible teneur en eau H2O = 1.5% à 3%, peut continuer à être utilisé, testez à nouveau six mois plus tard – 2 LED jaune OK
Le rouge = teneur en eau dans le liquide de frein H2O > 3%, ne peut pas continuer à être utilisé, le liquide de frein doit être remplacé. - 1 LED rouge H2O > 3%, une 2e LED rouge H2O > 4%
- Avec ce testeur j’ai put comparer le niveau de l’eau dans le liquide de frein. Surprise sur une voiture qui avait un taux élevé en eau. 1 LED rouge allumée = H2O > 3%
- Facile d'utilisation, un rinçage avant rangement et votre outil peut être réutilisé !
- Prix : Stylo testeur en vente depuis 6 Euros … (sauf DOT 5)
: Testeur de liquide de frein numérique : + de 20 Euros (sauf DOT 5)
- Pour les PROS :
- Testeur de liquide de frein Facom LCD : 512 Euros (sauf DOT 5) - Testeur de liquide de frein ATE : 750 Euros (sauf DOT 5)
- KS TOOLS 150.2198 Testeur de liquide de frein digital avec imprimante : 1365 Euros (sauf DOT 5)
- Le DOT 3 point d’ébullition : 220°C
- Le DOT 4 point d’ébullition : 240°C
- Le DOT 5.1 a un point humide d'ébullition d'environ 185 ° De plus le DOT 5.1 est deux fois moins visqueux que le DOT 4. En pratique, cela signifie qu'un système de freinage utilisant du DOT 5.1 aura un temps de réponse plus rapide, une meilleure modulation de freinage et une rétraction plus rapide des plaquettes. Le DOT 3, 4, 5.1 : Il s'agit d'une huile synthétique, à base de polyglycols.
- Bases les plus répandues, on y trouve les DOT 3, DOT 4, DOT 5.1. Ce sont des fluides de couleur ambre, qui présentent l'avantage d'être miscibles entre eux, et de ne pas être corrosifs pour les joints caoutchouc des étriers et des cylindres de frein. Ils sont généralement à base de glycol.
- DOT 5 liquide de freinage et d’embrayage à base de silicone. Le liquide de frein à base de silicone TRW DOT 5 permet une puissance de freinage optimale et garantie, produit de haute performance.
Spécialement recommandé pour les véhicules de collection et de compétition.
- Tout véhicule susceptible d'affronter des taux d'humidité importants.
- LIQUIDE DE FREIN DOT 5 SILICONE a pour propriétés :
- Insensible à l'humidité.
- Non miscible aux liquides de freins synthétiques (DOT 4 et DOT 5.1) et minéraux (LHM)
- Excellente compatibilité avec les joints et matières plastiques présents dans les circuits de freinage.
- Il n’endommage pas la peinture ni les surfaces imprimées.
- Point d’ébullition : 260°C
- Ne pas utiliser avec les systèmes fonctionnant d’origine avec des liquides à base minérale. Il est préférable de changer tous les joints du circuit de freinage lors du passage au DOT 5 silicone.
- Les dénominations DOT 5 et DOT 5.1 prêtent à équivoque. Il est impératif de ne jamais mélanger du DOT 5 (silicone) ou du DOT 2 avec les autres types, car il y a risque de détérioration des joints. Couleur violette.
Prix : 40 à 58 Euros le litre. Made in USA.
- Bases minérales :
- Elles sont réservées à certains modèles spécifiques de véhicules :
Citroën LHM et Rolls-Royce, le LHS Citroën dans les DS19 et ID, etc. … rouges ou verts. - Ces produits sont strictement réservés à quelques voitures (équipées de centrales hydrauliques) et ne sont pas miscibles avec d’autres liquides de freins. - Les liquides de freins sont classés en différentes catégories, spécifiées par le Department Of Transportation américain (d’où le sigle DOT utilisé)
- Bases synthétiques :
- Bases les plus répandues, on y trouve les DOT 3, DOT 4, DOT 5.1. Ce sont des fluides de couleur ambre, qui présentent l'avantage d'être miscibles entre eux, et de ne pas être corrosifs pour les joints caoutchouc des étriers et des cylindres de frein. Ils sont généralement à base de glycol.
- Bases silicone :
- Concerne le DOT 5. Les bases silicone présentent l'avantage d'être hydrophobes et donc d'être moins concernées par les problèmes de vieillissement.
Les dénominations DOT 5 et DOT 5.1 prêtent à équivoque. Il est impératif de ne jamais mélanger du DOT 5 (silicone) ou du DOT 2 avec les autres types, car il y a risque de détérioration des joints. Le liquide DOT 5.1 est normalement réservé à certains usages (compétition, contraintes thermiques élevées, etc.). Le liquide DOT 5 a cependant l'avantage de ne pas absorber d'humidité, ce pourquoi on l'utilise souvent aussi avec des joints adaptés dans les véhicules de collection qui ne roulent que rarement. L'appellation DOT 5.1 peut-être trompeuse par rapport aux qualités du DOT 4+ aussi appelé Super DOT 4 ou DOT 4 ESP. En effet, le tableau montre les caractéristiques qualitatives supérieures de ce dernier contrairement à ce que la numérotation pourrait suggérer. On constate que ce liquide est deux fois moins visqueux que le simple DOT 4.
- Utilisation du DOT 4 +
- Fluide destiné aux circuits de freins à disque ou à tambour ainsi qu’à la plupart des systèmes
d’embrayages des véhicules.
- Il convient aux régimes sévères d’utilisations (freins à disque atteignant des températures
élevées) et est particulièrement recommandé pour les véhicules équipés de systèmes
d’assistance de conduite tels que ESP (programme de stabilisation électronique), l’EBS
(système de freinage électronique), l’ABS (système antiblocage), l’ARS (accélération anti- dérapage),…destiné à améliorer le contrôle de trajectoire des véhicules automobiles et à
améliorer la sécurité routière.
- Propriétés et avantages :
- Haut point d’ébullition, évitant la formation de tampons de vapeur (« vapor lock ») dans
les circuits lors de l’utilisation intensive des freins.
- Faible viscosité à basse température pour une parfaite compatibilité avec les systèmes
d’assistance de conduite. Miscible à tous les autres liquides de freins DOT 5.1, DOT 4 et DOT 3. Compatible avec les différents types de joints et matériaux utilisés dans les circuits de
freinage et modulateurs hydrauliques. Haut pouvoir anticorrosion répondant aux exigences les plus sévères.
- Précautions d’emploi :
- Ne convient pas pour les circuits recommandant l’emploi d’un liquide hydraulique
minérale ou l’emploi d’un liquide de frein siliconé (norme DOT 5)
Voici quelques caractéristiques des principaux liquides de frein :
DOT 3 Norme ISO 4925 : grade 3 Viscosité cinématique maximale à −40 °C (en mm2 s−1) = 1500 - Température d'ébullition = 205° C - Température d'ébullition avec 3,7 % d'eau 140° C
DOT 4 Norme ISO 4925 : grade 4 Viscosité cinématique maximale à −40 °C (en mm2 s−1) = 1800 - Température d'ébullition = 230° C - Température d'ébullition avec 3,7 % d'eau 155° C
DOT 5 Norme ISO 4925 : grade 5 Viscosité cinématique maximale à −40 °C (en mm2 s−1) = < 700 - Température d'ébullition = 260° C - Température d'ébullition avec 3,7 % d'eau 185° C
DOT 5.1 Norme ISO 4925 : grade 5.1 Viscosité cinématique maximale à −40 °C (en mm2 s−1) = 900 - Température d'ébullition = 270° C - Température d'ébullition avec 3,7 % d'eau 191° C
DOT 4 + Norme ISO 4925 : grade 6 Viscosité cinématique maximale à −40 °C (en mm2 s−1) = 750 - Température d'ébullition = 300° C - Température d'ébullition avec 3,7 % d'eau 195° C
Daniel- Messages : 544
Date d'inscription : 22/04/2012
Age : 81
Localisation : Paris Ouest
Opeldel aime ce message
Re: restauration moteur ancien opel des années 60
- Compétition :
- En compétition, les liquides de frein subissant des températures encore plus élevées, des liquides différents sont utilisés.
- Tableau comparatif de quelques liquides de frein utilisés spécifiquement en compétition
AP 550 Racing : Point d'ébullition « sec » pour un liquide neuf 295 °C Point d'ébullition « humide » (chargé en eau à 3,5 %) 145 °C - Miscibilité DOT 3, DOT 4, DOT 5.1 : Oui
- AP 600 Racing : Point d'ébullition « sec » pour un liquide neuf 315 °C Point d'ébullition « humide » (chargé en eau à 3,5 %) 210 °C - Miscibilité DOT 3, DOT 4, DOT 5.1 : Non
- Castrol SFR Racing : Point d'ébullition « sec » pour un liquide neuf 310 °C Point d'ébullition « humide » (chargé en eau à 3,5 %) 270 °C - Miscibilité DOT 3, DOT 4, DOT 5.1 : Non
- Castrol RBF 600 : Point d'ébullition « sec » pour un liquide neuf 312 °C Point d'ébullition « humide » (chargé en eau à 3,5 %) 205 °C - Miscibilité DOT 3, DOT 4, DOT 5.1 : Oui
- Castrol RBF 660 : Point d'ébullition « sec » pour un liquide neuf 325 °C Point d'ébullition « humide » (chargé en eau à 3,5 %) 205 °C - Miscibilité DOT 3, DOT 4, DOT 5.1 : Non
- ABS :
- Les véhicules équipés d'ABS sont systématiquement montés avec des indices DOT supérieurs ou égaux à 4
- Entretien :
- Le liquide de frein doit être changé tous les deux ans ou 50 000 km environ.
- Corrosivité :
- Les liquides de frein sont généralement corrosifs7, et peuvent, notamment, attaquer les peintures utilisées en automobile.
- Le freinage hydraulique :
- Il est inventé en 1919 par la firme américaine Lockheed (frère d'Allan, tous deux cofondateurs de Lockheed) en 1919, ce dernier fonde la Lockheed Hydraulic Brake Company à Detroit et les véhicules Chrysler seront les premiers équipés en 1924. La Lockheed Hydraulic Brake Company deviendra Bendix en 1932. Avec le passage à une liaison hydraulique, la force appliquée a pu être beaucoup plus importante, rendant les freins plus efficaces, mais aussi plus sollicités.. La première auto à en bénéficier était une Rolland-Pilain (1905/1932) Grand Prix de l'ACF, 1914 à Lyon.
- Fini les câbles ... La transmission de l'effort à la pédale de frein se fait avec de l'huile (le Lockheed) dans des petits tuyaux jusqu'aux tambours ou aux disques.
Derrière la pédale, un maître cylindre distribue aux cylindres récepteurs grâce à de l'huile très fluide, la pression de la pédale de frein. Cette distribution est répartie, environ 70% à l'avant et 30% à l'arrière, suivant la charge du véhicule, par l'intermédiaire d'un répartiteur de freinage situé sur l'essieu arrière.
- Historique -
- Les grandes dates de l’histoire du frein :
- 1822 : Les premiers systèmes de freins sur les véhicules hippomobiles dates de 1822 surnommé ‘’l’enrayoir Leclerc ‘’ pour bloquer la calèche dans la descente d’une montagne, etc. Exemple : par une chaîne dans les rais de la roue. Il devint obligatoire en 1827 pour les voitures publiques. Puis vint le système avec un sabot. Le sabot « consiste en une pièce de fer recourbée en avant et portant deux oreilles latérales… Lorsque qu’on veut enrayer la roue, il suffit de placer le sabot en avant de la roue de telle sorte que celle-ci monte d’elle-même sur ce petit traîneau qui continuera le mouvement de la roue en le transformant en glissement. »
- En 1879, Binder proposa de remplacer volant ou manivelle par un frein à levier, crémaillère et cliquet. Vers cette époque, d’autres systèmes agissant sur le moyeu par l’enroulement de cordes sont proposés.
- A l’origine, le freinage d’une voiture consistait à passer une barre de bois entre les rayons pour bloquer les roues et donc ralentir la voiture en la faisant glisser sur les jantes.
«Enrayer : arrêter une roue par les rais en sorte qu’elle ne tourne point, mais qu’elle ne fasse que glisser…., passer une pièce de bois entre les deux roues…ou les enlier avec une corde pour empêcher qu’elles ne roulent et retarder leur mouvement à la descente d’une montagne » -Furetière- 1697.
- Mettre ainsi une « perche » (nommée « enrayoir ») agissant sur les rais, a donné naissance au terme ; enrayer ( le terme se trouve déjà dans les textes de R Estienne, en 1552, et J Thierry, en 1564) Par la suite, "enrayer" est devenu, dans un premier temps, le terme générique de tout mode de retenue d’une voiture hippomobile s'élargissant ensuite progressivement au freinage de divers dispositifs mécaniques.
- Ce moyen radical pouvait entraîner la détérioration des rais ce qui amena l'invention d’autres innovations moins fragilisantes pour la roue, par exemple lier, par une chaîne, la jante de la roue à la caisse.
- Freins à tambour (hippomobiles)
- La seule solution d’enraiement pendant des siècles fut la mise en place de sabots sous les roues. En 1851, un carrossier anglais Bascomb présenta une voiture équipée d’un système de frein à patin actionné par un volant, à l’Exposition universelle de Londres. En 1852, Mühlbacher frères (grand carrossier) obtint une médaille d’honneur à l’Exposition Universelle de Paris pour un break équipé d’une machine à enrayer. En 1879, Binder proposa de remplacer volant ou manivelle par un frein à levier, crémaillère et cliquet.
- Vers cette époque, d’autres systèmes agissant sur le moyeu par l’enroulement de cordes sont proposés.
- La maison « Mülhbacher » est qualifiée par le guide du carrossier en 1889 comme la maison «la plus ancienne…. la plus grande de Paris ». Elle fut créée en 1797 par Godefroy (Georges-Geoffroy) Mühlbacher, né à Strasbourg en 1767, d’une famille originaire du duché de Wurtemberg. Il s’installa à Paris comme charron, au 14, rue de la planche, à partir de 1814. Pendant prés de 120 ans, cette maison fut un des fleurons de la carrosserie parisienne. La maison ¨Mühlbacher fut rachetée par "Belvalette" (1804-1933) En 1845, l’écossais William Thomson dépose un brevet de « roue à air », confectionnée à partir de plusieurs épaisseurs de toile de caoutchouc recouvertes de cuir et fixées par des boulons sur une jante de bois. Cette roue ne sera pas opérationnelle. Il fallut attendre 1871 pour voir la fabrication de tuyaux en caoutchouc par Continental, et en 1872 par Pirelli. En 1888, John Boyd Dunlop (1840-1921) invente un pneumatique pour vélo (chambre de caoutchouc avec une enveloppe de coton, elle est gonflée d’air et « collée » sur une jante en bois) Elle sera utilisée dans les compétitions cyclistes dés 1889. Le premier fiacre à roue à bandage pneumatique roule à Paris en 1896.
- Autre système à enroulement, le "Frein automatique stop" fixé sur les traits. La détente de ceux ci dans les descentes mettait en action le dispositif.
- Il faudra attendre le début du XXe siècle pour voir apparaître le frein à tambour, dont l’invention en France est attribuée à Louis Renault (1877-1944) en 1902.
- Avec l'apparition du bandage caoutchouc (1888), puis du pneumatique, le patin de freinage intègre la roue arrière dans un tambour.
- D'abord monté sur l'essieu arrière, le tambour gagnera rapidement les roues avants.
- L'automobile naissante du début du siècle freinait comme les "carrioles" et les trains c'est à dire, un patin de bois serré sur le cerclage métallique d'une roue en bois !
- Le bandage caoutchouc sur une roue en fer, puis, le pneu, ont rejeté le frein dans un tambour, nettement plus efficace, au point qu'il existe encore à l'arrière d'une majorité de voitures. Ces véhicules étaient juste pourvus de 2 freins arrière à tambours. Ceux-ci étaient très petits. (Ford T (1908-1927) par exemple)
- Deux demi-segments en métal à l'intérieur du tambour étaient actionnés par un câble relié à une pédale, voire un simple levier manuel. Il n'y avait bien entendu aucune obligation ni législation! ...
- Très vite, la vitesse des véhicules évoluant avec la puissance des moteurs, ce freinage devint obsolète. Les ingénieurs de l'époque, après quelques nuits blanches et quelques incidents, ont mis au point le freinage hydraulique sur les 4 roues, toujours avec des tambours, mais avec un matériau composite métal/amiante/ bf (toile bakélisée) pour les demi- segments.
- Bf : Beaucoup plus connue sous l'appellation commerciale CELORON, il s'agit d'un matériau composite qui est une combinaison d'une matrice : résine phénolique (bakélite) et d'un support : toile coton. Il existe d'autres nuances en fonction du support : papier, bois, qualité de la toile coton.
- Caractéristiques principales du céloron :
- Bonne résistance mécanique.
- Résistant à l'usure avec une bonne élasticité.
- Absence de grippage même à sec.
- Diminution du bruit (engrenages)
- Bon isolant électrique.
- ( Dans le domaine d'expression anglo-saxon, ce matériau est connu sous le nom de Tufnol en 1924 (Parfois orthographié Tuphnol ou encore novotext) - Usine à Birmingham Royaume-Uni.
- Fin 1923, lancement en série du freinage hydraulique sur les 4 roues, généralement sur 6 cylindres Chrysler ; puis adoption se généralisant au cours des années 20 (freins Lockheed - Tracta 1928) Le freinage s'effectuait par l'intermédiaire de tambours aux 4 roues. Ceux-ci grossissaient jusqu'à remplir totalement la roue. Ils étaient souvent en alliage et comportaient des ailettes de refroidissement.
- Tracta : 1927-1958- J.-A. Grégoire. (1899-1992) - Le joint Tracta est un double cardan sphérique breveté le 8 décembre 1926 par Pierre Fenaille, associé de J.-A. Grégoire, puis industrialisé par la société Tracta. - C'est un joint homocinétique (adjectif inventé à cette occasion) qui fut utilisé dans la construction des premières automobiles européennes à traction avant.
- Le joint Tracta a été adopté par différentes marques, dont DKW entre 1929 et 1936 et Adler de 1932 à 1939, ainsi que sur la plupart des voitures conçues par J.-A. Grégoire. On le retrouve dans de nombreux véhicules militaires de la Seconde Guerre mondiale : Laffly et Panhard en France, Alvis et Daimler au Royaume-Uni et Willys aux États-Unis qui monta le joint Tracta dans un quart de million de jeeps et nombreux autres véhicules. Ce succès se confirma après la guerre, dans les premiers modèles de Land Rover.
- Freins pour les voitures : Les grandes dates du freinage.
* 1902 : Freins à tambour – Attribué à Louis Renault
* 1902 : Freins à disque brevetés par F.W. Lanschester- 1868-1946 - (G.B)
* 1903 : freins sur roues avant (VAN HOOYDONK)
* 1904 : 1ère voiture à pétrole pourvu de freins (à air comprimé) sur les 4 roues (voiture Charley sur châssis Mercedes)
* 1910 : brevet du frein hydraulique (WEIGHT)
* 1911 : 1er freinage sur les 4 roues.
* 1912 : frein à main sur Isetta Fraschini.
* 1919 : 1er frein à commande hydraulique : Lockheed.
* 1921 : Dépôt du brevet de servo-frein par Renault
* 1923 : (fin 1923) Lancement des freins hydrauliques sur les 4 roues.
* 1926 : Les freins à tambours Adoption universelle après 1926 ...
* 193* : Début des années 30 les freins auto-serreurs Bendix
* 1936 : les prémices de l’ABS. Agit sur les freins en évitant leur blocage par légers freinages successifs. Un dispositif dont les prémices remontent à 1936
* 1951 : Apparition du frein à disque sur Jaguar en compétition
* 1953 : Apparition du frein à disque (lancé en série sur la DS 19 CITROËN en 1955) Course : 24 Heures du Mans en 1953- sur Type C (britannique) 1ère place et la 2e place en 1954
* 1960 : Montage en série des freins hydrauliques à tambours sur les 4 roues.
* 1969 : Honda CB 750 Four de 1969, qui a imposé le disque à commande hydraulique puis en compétition.
* 1973 : L'invention de l'ABS par Bosch
* 2000 : Vers les années 2000, la suppression de l'amiante contenu dans les plaquettes.
* 2003 : Mercedes Benz innove en proposant des disques de freins en céramique.
* 20** : Bosch prévoit prochainement un freinage électrique, une réponse plus rapide au freinage, sans l’utilisation du DOT très corrosif…Concrètement, le frein ne serait plus actionné par un circuit hydraulique et par des maître cylindres, mais par une commande électrique reliée à un système informatique, qui pourrait même être paramétrable, laissant ainsi le choix du "ressenti" à la pédale.
- Frein à bande :
- C’est un système extrêmement simple de construction. Au début, il est constitué d’une bande de feuillard d’acier entourant la jante d’une poulie en fonte. A partir des années 1910, cette bande est recouverte d’une garniture de friction. Le gros avantage du frein à bande est que, dans sa grande simplicité, la poulie en tournant a tendance à entraîner la bande dès que, par la commande, on applique cette dernière sur la poulie. Plus la poulie tourne, plus la bande est entraînée et plus elle serre. C’est de que l’on appelle un frein auto-serreur.
- Un des inconvénients est un certain manque de progressivité et dans le freinage. Il apparaît également une usure assez rapide de l’ensemble. De plus, il existe une presque totale inefficacité en marche arrière, le phénomène d’auto-serrage jouant en sens inverse. Cependant le frein à bande a le gros avantage d’assez bien évacuer la chaleur dans l’atmosphère. Des systèmes archaïques inadaptés à des puissances élevées. C'est pour cela que des constructeurs, comme Ford, ont créé sur la Model T un système de ruban s'enroulant sur un tambour dans la transmission. Mais là encore, l'endurance du freinage manquait, tout comme le mordant. La transition vers un système plus fiable était inéluctable et devait être mise au point.
- Correct pour l’époque - entretien facile – peut coûteux
- Inconvénients : Freinage médiocre – Usure rapide – Dangereux-
- Freins à tambours :
- Du plus simple (frein ordinaire) au plus sophistiqué :
- D'abord monté sur l'essieu arrière, soit par des tambours et segments agissant directement sur le moyeu des roues, soit par un simple tambour muni de segments placés sur l’arbre secondaire de la boîte de vitesses et freinant la transmission. Il gagnera rapidement les roues avants. Son adoption sera universelle après 1926. Dès les débuts, la commande de freinage se fait par des câbles, une simple tringle, actionnés à la main ou par une pédale. Les freins à tambours grossiront jusqu'à remplir totalement l'intérieur de la roue, s'équiperont d'ailettes de refroidissement et seront en fonte, en alliage.
- Types de frein à tambour:
- Frein ordinaire :
- Combien de mécaniciens se sont acharnés pour régler des freins datant des années d’avant 1950. Je veux parler des freins dont les segments pivotaient sur des axes non réglables. Avec ce système même après avoir remplacé les garnitures et rectifier les tambours, le freinage n’était pas amélioré ou n’était efficace que sous une action énergique du conducteur. C’est en corrigeant les deux défauts de centrage des segments et conception de la came que les constructeurs sont parvenus à concevoir les freins actuels qui, bien réglés et en état, sont merveilleux.
- Il est composé de plusieurs éléments :
- 2 segments de freins, 2 garnitures, 1 tambour, 1 plateau, 2 points d’articulation, 1 came double ou appelée aussi tournevis, 1 ressort de rappel.
- Les freins à tambours genre Renault et Ford :
- Ces deux montages ne diffèrent l’un de l’autre par le système de commande et le procédé d’écartement des segments.
- Dans le système Renault, la came st constituée par un doigt en acier rond, dont les extrémités sont usinées en forme de came, et ces doigts sont montés libres dans un axe. Ce montage permet l’équilibrage des deux segments.
- Dans le système Ford, la came est remplacée par une came en forme de coin monté libre entre les segments. Cette pièce permet également l’équilibrage des segments.
- Dans les deux systèmes les points fixes inférieurs sont supprimés et les segments sont articulés sur des chapes reposant sur une vis de réglage. L’extrémité de la vis de réglage se termine par un cône cannelé. En déplaçant cette vis dans un sens ou dans l’autre, on obtient le rapprochement ou l’écartement des segments par rapport au tambour. Etc…
- Il est composé de plusieurs éléments :
- 2 segments, 2 garnitures, 1 tambour,1 plateau, 2 chapes d’articulation, 4 vis conique et dentée réglable, tournevis ou porte came, 1 came double flottante, 2 galets, 2 axes de galets tournant butée de centrage des segments, ressort de rappel.
- Pour gagner en efficacité, beaucoup de solutions furent imaginées, Duo-servo, twin-plex, Hcsf, etc… ......
- De nos jours tous les freins à tambours montés sur nos autos sont de type "Segments flottants" et équipés de rattrapage automatique de l'usure.
Ce montage permet un auto-centrage des segments lors du freinage, un nombre de pièces limité, une facilité de montage-démontage sans oublier une répartition des forces de freinages la plus favorable. On parlera de segment "Comprimé" et de segment "Tendu" nommés ainsi en fonction du sens de rotation de la roue.
- Fonctionnement :
- Le frein à tambour est solidaire de la roue mais la différence c'est que le système est encapsulé et inaccessible. Il se compose de 2 mâchoires -ou segments- qui s'écartent. Sur leur face extérieure se trouve la garniture qui vient frotter contre l'intérieur du tambour.
Les segments sont actionnés par l'intermédiaire d'un cylindre hydraulique de réception. Le fameux cylindre de roue!. Le frein à tambour a une efficacité élevée - Coefficient d'auto- serrage dès la mise en pression, mais celui-ci chute très rapidement sous l'influence de la vitesse. Pour augmenter l’efficacité du freinage, les segments sont garnis, sur leur diamètre extérieur, d’une bande frottement en matière spéciale à base d’amiante tressée avec du fil de laiton ou de plomb.
- Freins à tambours :
- Ses avantages - - Ses inconvénients -
Efficacité : Déformation :
Coût Manque de progressivité
Rayon frotté important Refroidissement insuffisant
Protection à l'eau, à la boue Ventilation faible (poussière)
Flux thermique (faible usure) Manque de stabilité
- Le gros inconvénient du frein à tambour est qu’il est conçu comme un véritable four et qu’il dissipe très mal la chaleur. Sa partie la plus chaude étant la partie interne, la chaleur dégagée par le freinage doit traverser la paroi du tambour pour pouvoir se dissiper dans l’atmosphère. Les tambours à ailettes tentent de remédier à cet inconvénient.
- Une température excessive du système amène tout d’abord une grande diminution du coefficient de frottement des garnitures. Il en résulte une diminution de plus en plus importante de l’efficacité du freinage. Si l’on insiste encore plus, les organes de freinage peuvent passer au rouge avec des conséquences graves. On peut alors constater des déformations des tambours, des grillages des garnitures et même la détérioration des joints à lèvres des moyeux. On peut même en arriver à la vaporisation de la graisse et l’usure prématurée des roulements. Ce scénario était souvent constaté dans la descente de cols alpins au cours d’épreuves sportives dans les années 50.
- Avec ses qualités et ses défauts, le tambour présente aujourd'hui une solution satisfaisante. Ce qui explique que l'on en trouve sur la grande majorité des petites autos, même équipées de système ABS, le frein à main est intégré au tambour. Ces mêmes défauts expliquent aussi pourquoi les freins à tambours ont été détrônés rapidement par les freins à disques pour l'essieu avant.
- Frein auto-serreur Bendix :
- Au début des années 30 apparurent les freins auto-serreurs Bendix. Ils se répandirent rapidement sur les Matford (1934/1940), Citroën, Peugeot, jusqu’à la génération de la commande hydraulique. Les 4 freins sont commandés par câbles.
- Le principe de ce type de frein est qu’une seule mâchoire est plaquée contre le tambour par la came de serrage. Cette mâchoire a tendance a être entraînée par le tambour. C’est ce déplacement minime qui provoque le serrage de la seconde mâchoire dont la dernière extrémité s’appuie sur un point fixe.
- Les avantages de ce système sont multiples : Tout d’abord, il y a un très bon phénomène d’auto-serrage diminuant beaucoup l’effort demandé au pilote. Mais également, le mécanicien trouve avec une très grande facilité un centrage correct pour les garnitures. N’ayant qu’un seul point fixe, le réglage est nettement plus rapide. Le démontage de ces freins s’effectue, à très peu de choses près. Seulement, ici, lorsque que les 3 ressorts de rappel et ceux de positionnement sont enlevés, plus rien ne retient les mâchoires. Faire attention au remontage les ressorts sont de longueurs et de forces différentes, la came de commande est formée d’un levier ouvert en forme de chape se montant à cheval sur un point fixe. Bien repérer le sens de montage des différents éléments. L’ensemble se comportait alors, comme un frein à 4 mâchoires, ce qui provoquait également un phénomène d’auto-serrage. Ces freins pouvaient être très puissants même si, très souvent, ils étaient difficiles à équilibrer avec des commandes par câbles.
- Il est composé de plusieurs éléments :
- 1 tambour de frein, 1 plateau, 2 demi segments, 2 demi-segments auto-serreur, garnitures, 1 point fixe repos commun des segments, 1 levier de commande formant came double flottante, 1 câble, 1 chape de réglage filetée à droite, 1 chape filetée à gauche, 1 écrou denté, ressort de rappel, 1 ressort faible de rappel du segment auto-serreur, ressort fort du segment de serrage, excentrique de centrage de l’ensemble du mécanisme.
- Le réglage est assez pointu, il faut régler en mettant une cale de bois de 2 à 3 cm d’épaisseur sous la pédale. Régler les mâchoires pour quelles viennent lécher les tambours avec l’aide des molettes, sur les 4 roues. Détendre les câbles de freins pour qu’ils soient uniformément serrés, etc. Le serrage doit être uniforme dans les deux sens en tournant la roue à la main. Il faut mieux avoir les câbles lâches, du moment qu’ils sont réglés à la même longueur et que les segments doivent être le plus rapprochés possibles des tambours. 9 fois sur dix ces freins accrochent par ce que les câbles sont trop tendus au moment du réglage. Faire un essai routier et corriger si besoin est. Le problème principal est : Les câbles ont toujours tendances à s’allonger ce qui provoquera un certain déséquilibre dans le freinage. Ce problème était récurant sur la Rosalie C4/C6G de 1932.
( Matford : Accor de Mathis (Alsacien) et de Ford SAF. Production française du V8 à soupapes latérales, donc pas de culbuteurs de 60 ch SAE)
- Recommandation : (extrait du manuel)
- Pour conserver la souplesse à ces freins, il est indispensable que les câbles coulissent très librement dans leur gaine. Au cours d’une révision, vous devez appliquer au nettoyage et aux graissages des câbles, même ceux dont les gaines sont munies d’un graisseur. Pour cela, débranchez-les, et tirez-les le plus possible en dehors de leurs gaines. Pour bien les nettoyer, faites-les marcher plusieurs fois avec du pétrole et remontez-les très largement huilés. Etc…
- Le freinage hydraulique :
- Ce nouveau mode de commande fut inventé en 1919 par la firme américaine Lockeed. La première auto à en bénéficier était une Rolland-Pilain (1905-1932), préparée pour le Grand Prix de l'ACF, 1914 à Lyon.
- Fini les câbles ... la transmission de l'effort à la pédale de frein se fait avec de l'huile (le Lockeed) dans des petits tuyaux jusqu'aux tambours ou aux disques.
- Derrière la pédale, un maître cylindre distribue aux cylindres récepteurs grâce à de l'huile très fluide, la pression de la pédale de frein. Cette distribution est répartie, environ 70% à l'avant et 30% à l'arrière, suivant la charge du véhicule, par l'intermédiaire d'un répartiteur de freinage situé sur l'essieu arrière.
- Le circuit est composé d’une pompe commandé par la pédale de frein. A la sortie de la pompe sont branchées quatre canalisations qui amènent le liquide dans les cylindres, placé sur chaque roue. Ces cylindres commandent les segments de frein par l’intermédiaire de deux pistons indépendants. Le maître cylindre ou pompe se compose d’un cylindre ou corps de pompe, dans lequel un piston actionné par la pédale comprime le liquide au travers des canalisations simultanément dans les quatre cylindres. Le maître cylindre est alimenté par un réservoir à liquide qui est en communication avec lui, lorsque le piston est au repos. Ce réservoir sert de détente au liquide en cas de dilatation, etc.
- Le maître cylindre de frein d’une Opel Rekord ( 1954-1955) est composé de :
- Chape, contre-écrou, tige poussoir, soufflets de caoutchouc, corps du maître-cylindre, orifice d’alimentation, bouchon, joint d’étanchéité, orifice de compensation,boîtier du clapet de pression résiduelle, filetage destiné à recevoir l’écrou qui fixe le corps du maître-cylindre sur la traverse de soubassement de carrosserie, siège du clapet de pression résiduelle, coupelle de caoutchouc pour le clapet de pression résiduelle, ressort du piston et du clapet, siège du ressort, coupelle primaire du piston, plaquette formant clapet du piston, piston, coupelle secondaire du piston, rondelle de butée, jonc d’arrêt.
- Le tambour de frein :
- Il est composé de plusieurs éléments :
- 1 tambour, 1 plateau, 2 garnitures, 2 segments, 2 bagues excentrées, 1 ressort de rappel, 2 excentriques de réglage, cylindre composé de 2 pistons, de 2 poussoirs, 1 arrivée du liquide, 1 vis de purge avec son capuchon de caoutchouc.
- L'assistance de freinage ou servo-frein :
- Son rôle est d'amplifier l'effort de freinage.
- Première application commerciale sur la Renault 40 en 1921. Il a été "vulgarisé" progressivement (servo-frein à dépression) à partir de 1961 (Mercedes) D'autres modes d'amplification avaient été inventés auparavant mais la simplicité et le faible coût du servo à dépression lui donneront l'avantage.
- Le frein auto-serreur Bendix sera amélioré en passant du frein à câble au frein hydraulique. Il sera monté sur les voitures de luxe : Delage (1905-1953), etc.
- Fonctionnement :
- Le système utilise la dépression située dans la pipe d'admission du moteur pour accentuer l'effort du freinage, par l'intermédiaire d'une petite bombonne (mastervac) située derrière le maître cylindre. Cette capacité est constituée de 2 demi-coquilles métalliques assemblées hermétiquement.
- Dans cet ensemble on trouve : le piston moteur, le diaphragme et le ressort. Le maître-cylindre est fixé sur la face extérieure du servo-frein et assure l'étanchéité de l'ensemble. Le piston moteur est soit directement actionné par la pédale de frein (Mastervac) soit par l'intermédiaire d'une canalisation hydraulique (Hydrovac) Tous les véhicules actuels utilisent des Mastervac. L'amplification est fixée par le constructeur après calculs et essais des divers composants du système de freinage. On le nomme "Ratio"ou Rapport d'amplification.
- Aujourd'hui d'autres formes d'assistance voient le jour, le freinage EHB par ex. (Electro-Hydraulic Brake) système commercialisé sur la Mercedes classe E.
- La principale évolution du servo-frein est survenue très récemment avec l'arrivée des AFU, BAS, DBC etc… et autres appellations barbares. Le principe de base est d'utiliser toute la puissance disponible du servo-frein le plus rapidement possible en cas de freinage d'urgence et tout ça grâce à l'électronique qui détectera un appui rapide sur la pédale.
- La disparition de l'amplification de freinage telle que nous la connaissons est programmée, car l'avènement du freinage électrique et électronique (Brake By Wire) est pour bientôt.
- Freins à disques :
- Toutes sortes de matériaux peuvent être utilisées.
- Pour les disques :
- Acier inoxydable (assez cher, peu accrocheur)
- Fonte (le plus économique, rouille aisément, le plus lourd, le plus utilisé)
- Carbone (cher, extrêmement léger, particulièrement endurant, efficace principalement à haute température, réservé à la compétition ou sur des véhicules de sport de particulièrement haut de gamme)
- Les plaquettes sont le plus souvent constituées d'un support en acier, assurant la fixation dans les étriers, sur lequel est fixé par collage un patin en matériau composite, s'usant progressivement au cours de l'usage. La composition du patin fluctue suivant le matériau du disque et suivant les fabricants. L'amiante a été longtemps utilisé dans la composition de ces patins et elle y est désormais interdite.
- Types d'étriers :
- Fixe :
2, 4, 6 voire à 8 pistons. L'étrier est fixé solidairement à la fusée, est composé d'une seule pièce. C'est le mouvement des pistons (poussés par le liquide hydraulique), qui permettent aux plaquettes de venir serrer le rotor.
- Flottant :
- 1 ou 2 pistons L'étrier se compose de deux pièces. La chape fixée sur la fusée et la pince articulée sur la chape par l'intermédiaire de colonnettes. Lors d'un freinage, le piston est poussé par le liquide contre la plaquette intérieure et par réaction d'équilibre, la pince coulisse sur les colonnettes et vient à son tour appuyer la plaquette extérieure sur le rotor.
- Dans chaque configuration d'étrier, on trouve deux types de disques : Plein ou Ventilé Le disque ventilé comme son nom l'indique permet un meilleur refroidissement et du coup une plus grande endurance. Dans certains cas, la forme des ailettes internes est optimisée pour accroître encore le refroidissement.
- L'évolution vers le disque en céramique est déjà prête, puisque quelques voitures de prestige en sont équipées (Porsche, Mercedes) Cette technologie accroît la résistance à la chaleur, 1400°C pour 900 / 1000°c actuels, reste insensible à la corrosion, de plus le coefficient de frottement reste stable.
Avantages/Inconvénients :
- Comparer au frein à tambour, le frein à disque a l'avantage d'être plus progressif car il n'est pas auto-serrant. Par contre, il nécessite une plus grande pression pour être efficace, la pression du conducteur est transmise par un dispositif hydraulique fréquemment assisté (c'est pourquoi la commande en est rarement mécanique, car il est malcommode d'obtenir une démultiplication suffisante par un dispositif de leviers)
Sensibilité à l'eau :
- Le disque est perforé, l'étrier est à double piston. La commande est hydraulique.
Généralement, le frein à disque fonctionne à l'air libre, ce qui lui permet d'évacuer les calories du freinage par ses deux faces. Par contre, cela l'expose aux projections d'eau, ce qui provoque un retard au freinage quand il est mouillé (obligation de le sécher en quelques tours avant de récupérer le mordant) Pour contrer cet ennui, il est habituel de perforer les disques des motos de nombreux trous conçus pour rompre le film liquide.
- L'ABS :
- L'anti-blocage des roues dans un freinage d'urgence, est mis au point par Bosch en 1973, puis est monté sur les voitures de haute gamme en 1978 (sur la classe S de Mercedes) et petit à petit sur les voitures de série vers 1990.
- C'est un système électronique constitué d'un calculateur relié électriquement à un répartiteur de freinage hydraulique et de 4 petits capteurs situés sur les tambours ou les disques. Ils contrôlent la rotation de la roue. Si, dans un freinage brutal, la roue vient à bloquer, le capteur transmet immédiatement l'information au calculateur qui relâche la puissance du freinage hydraulique sur cette roue ... On ressent à la pédale des petits à-coups.
- Les matériaux modernes :
- Le remplacement systématique de l'amiante dans les freins sera obligatoire après le 1er janvier 2003 et vous ne pourrez plus changer de carte grise sans montrer "patte blanche" . . .
- Pour bien freiner :
- Un bon freinage se construit dès les premiers dixièmes de seconde. En pratique d'urgence, on freine "fort" d'abord, et on régule ensuite et JAMAIS l'inverse.
- N'oublions pas que le système de freinage requiert une attention particulière pour être toujours efficace, liquide propre, pièces d'origines du constructeur, particulièrement les plaquettes de freins.
- Évitez les plaquettes adaptables :
- Il existe deux types de plaquettes de frein sur le marché : les originales et adaptables. Les secondes coûtant deux fois moins cher que les premières sont néanmoins conçues en matériaux de qualité inférieure. A contrario, les plaquettes originales fabriquées par un fournisseur reconnu ont le mérite de respecter les normes et assurent une sécurité bien plus sûre. Autrement dit, il est primordial d'éviter les plaquettes au prix excessivement bas.
Les plaquettes adaptables ont des caractéristiques techniques légèrement inférieures à celles des pièces d'origine. Ces plaquettes sont moins onéreuses, tout en offrant une performance de freinage convenable. Toutefois, ces plaquettes adaptables sont faites avec des matériaux de qualité inférieure. D'une façon générale, ces plaquettes ne sont pas soumises aux essais nécessaires et ne répondent pas aux normes courantes. Il est essentiel d'éviter les erreurs lors du choix de vos plaquettes: un prix trop bas doit vous alerter.
- Il est indispensable de choisir des plaquettes de frein de bonne qualité et en fonction de votre système de freinage. Nous vous proposons ici un guide pour vous permettre de choisir les meilleures plaquettes de frein en fonction de vos besoins et votre budget. Vous pourrez trouver sur le marché un large éventail de possibilités : pas chers, pour frein arrière, à disque, anti-corrosion... et pour tous les modèles de voiture. Attention à bien vous renseigner avant de changer vos plaquettes de frein.
- Une fois le changement effectué, mieux vaut « rôder » les plaquettes en faisant des freinages modérés pendant quelques dizaines de kilomètres : il y a en effet un risque de « vitrification » des plaquettes. De plus cela permet de bien remettre tout le système de freinage en pression et de laisser le temps aux plaquettes de bien se positionner dans les étriers.
- Bien qu’il soit possible de changer soi-même les plaquettes de frein, mieux vaut faire appel à un professionnel de la réparation automobile. C’est en effet un élément de sécurité très important, mieux vaut éviter un mauvais montage.
Les meilleurs fabricants de plaquettes de frein
- Paramètres principaux des plaquettes de frein
- Température de fonctionnement. Les plaquettes de frein qui résistent à des températures de 300 à 350°C doivent suffire pour une conduite citadine et des vitesses pas trop élevées. Les voitures de sport sont équipées de plaquettes de frein qui peuvent fonctionner à 900°C, mais n'assurent un freinage efficace qu'à partir de 100°C.
- Coefficient de frottement. Les plaquettes avec un coefficient de frottement de 0,25 - 0,35 sont suffisantes pour arrêter un véhicule lors d'une conduite souple. Ce sont les valeurs typiques des pièces équivalentes aux pièces d'origine. Le coefficient de frottement des plaquettes de frein d'origine est légèrement plus élevé, de 0,3 à 0,5. Les plaquettes de frein de sport ont une température de fonctionnement de 150 °C et ont un coefficient de frottement faible - 0,2. Lorsqu'elles sont chaudes, ce coefficient peut atteindre 0,5.
- Durée de vie. La résistance à l'usure des plaquettes dépend des matériaux qui les composent. Les garnitures tendres s'usent plus rapidement, mais des garnitures trop dures provoquent une usure prématurée du disque de frein.
- Les principaux fabricants de plaquettes de frein sont :
- Brembo : Bergame - Italie 1961; Ferodo - chapel-en-le-frith- G.B 1897; Bosch (Robert) Gerlingen- De - 1886 ; ATE -De -1906 ; TRW- 1901 USA – rachète Lucas G.B puis rachetée par en 2002 par Northrop- Grumman ; STARK- De - 2013 ; Textar - De - 1913; Lucas 1874 - GB devient TRW 1999 ; JURID - USA, siège : De - Düsseldorf - 1915 ; Remsa – Corella - Spain –1970, rachetée par TRW en 2000 ; PAGID créée en 1925 - De (Hella Padig Brake systems - Hella De : créée en 1899) Bendix 1927- 2015.
- Les produits de ces fournisseurs diffèrent en prix et en caractéristiques techniques. Les fabricants BREMBO et FERODO produisent des plaquettes de frein pour voitures de sport. Les pièces de l'entreprise ATE sont également capables de supporter de températures d'utilisation pouvant aller jusqu'à 800°C.
- Les plaquettes de frein de TRW, LUCAS, BOSCH, REMSA et STARK sont plus adaptées pour la conduite en ville. Elles ont des spécifications techniques inférieures, mais sont considérablement moins chères. L'entreprise PAGID fabrique des pièces pour voitures de luxe.
- Le fournisseur américain JURID ( Southfield, Michigan, depuis 1899) produit des plaquettes qui sont utilisées par les constructeurs automobiles, mais peuvent également être achetées comme plaquettes adaptables pour des véhicules d'autres marques. Les produits de ce fournisseur sont également commercialisés sous les marques BENDIX-R Pennsylvanie- USA, FRAM-R et PRESTONE -R.
- BREMBO : Un leader en compétition
- Les compétences technologiques exceptionnelles de Brembo sont consacrées en 1975,
lorsque le patron de Maranello, Enzo Ferrari, fait confiance à l’entreprise de Bergame pour
s’occuper des systèmes de freinage de la plus prestigieuse des Formules 1. Brembo devient
alors très vite leader dans les systèmes de freinage en compétition. Depuis, les écuries
équipées de freins Brembo ont gagné des centaines de championnats du monde de course
auto et moto.
- Innovation et stratégie : étriers de freins en aluminium
- Dans le cadre d’une stratégie d’expansion ciblant des marchés de niche – voitures et motos
de compétition – Brembo commence, au début des années 80, à développer des produits et
des procédés technologiques innovants. En 1980, la société ajoute à sa gamme un étrier de
frein disposant d’un design particulièrement innovant et fabriqué dans un nouveau matériel –
l’aluminium. Progressivement, ces nouveaux étriers en aluminium sont adoptés par des
Fabriquant de voitures sportives, tels que Porsche (aujourd’hui encore fourni à 100% par
Brembo), Mercedes, Lancia, BMW, Nissan, et Chrysler.
Au milieu des années 80, Brembo décide d’entrer sur le segment des disques de frein pour
véhicules industriels, et devient rapidement un fournisseur stratégique d’Iveco, Renault,
Trucks et Mercedes.
2013 - Brembo remporte pour la septième fois le trophée de Meilleure Marque de Motorrad,
Auto Motor und Sport, Auto Bild et PS Magazin.
Brembo est récompensé pour les meilleurs standards de qualité de l’industrie automobile
par le trophée 2013 de Supplier Quality Excellence de General Motor’s.
De plus, à l’occasion de la première edition du Sustainability Supplier of the Year Award de
Fiat-Chrysler, Brembo est reconnu fournisseur durable de l’année 2012. Etc…
- Rappel : - Lorsque vous devez choisir des plaquettes de frein, il est essentiel de prendre en compte non seulement la popularité de la marque, mais aussi les spécifications techniques qui doivent être adaptées à votre style de conduite et aux conditions d'utilisation du véhicule. Ce n'est qu'en faisant attention à tous ces détails que vous pourrez choisir des pièces fiables et durables.
- LD
- En compétition, les liquides de frein subissant des températures encore plus élevées, des liquides différents sont utilisés.
- Tableau comparatif de quelques liquides de frein utilisés spécifiquement en compétition
AP 550 Racing : Point d'ébullition « sec » pour un liquide neuf 295 °C Point d'ébullition « humide » (chargé en eau à 3,5 %) 145 °C - Miscibilité DOT 3, DOT 4, DOT 5.1 : Oui
- AP 600 Racing : Point d'ébullition « sec » pour un liquide neuf 315 °C Point d'ébullition « humide » (chargé en eau à 3,5 %) 210 °C - Miscibilité DOT 3, DOT 4, DOT 5.1 : Non
- Castrol SFR Racing : Point d'ébullition « sec » pour un liquide neuf 310 °C Point d'ébullition « humide » (chargé en eau à 3,5 %) 270 °C - Miscibilité DOT 3, DOT 4, DOT 5.1 : Non
- Castrol RBF 600 : Point d'ébullition « sec » pour un liquide neuf 312 °C Point d'ébullition « humide » (chargé en eau à 3,5 %) 205 °C - Miscibilité DOT 3, DOT 4, DOT 5.1 : Oui
- Castrol RBF 660 : Point d'ébullition « sec » pour un liquide neuf 325 °C Point d'ébullition « humide » (chargé en eau à 3,5 %) 205 °C - Miscibilité DOT 3, DOT 4, DOT 5.1 : Non
- ABS :
- Les véhicules équipés d'ABS sont systématiquement montés avec des indices DOT supérieurs ou égaux à 4
- Entretien :
- Le liquide de frein doit être changé tous les deux ans ou 50 000 km environ.
- Corrosivité :
- Les liquides de frein sont généralement corrosifs7, et peuvent, notamment, attaquer les peintures utilisées en automobile.
- Le freinage hydraulique :
- Il est inventé en 1919 par la firme américaine Lockheed (frère d'Allan, tous deux cofondateurs de Lockheed) en 1919, ce dernier fonde la Lockheed Hydraulic Brake Company à Detroit et les véhicules Chrysler seront les premiers équipés en 1924. La Lockheed Hydraulic Brake Company deviendra Bendix en 1932. Avec le passage à une liaison hydraulique, la force appliquée a pu être beaucoup plus importante, rendant les freins plus efficaces, mais aussi plus sollicités.. La première auto à en bénéficier était une Rolland-Pilain (1905/1932) Grand Prix de l'ACF, 1914 à Lyon.
- Fini les câbles ... La transmission de l'effort à la pédale de frein se fait avec de l'huile (le Lockheed) dans des petits tuyaux jusqu'aux tambours ou aux disques.
Derrière la pédale, un maître cylindre distribue aux cylindres récepteurs grâce à de l'huile très fluide, la pression de la pédale de frein. Cette distribution est répartie, environ 70% à l'avant et 30% à l'arrière, suivant la charge du véhicule, par l'intermédiaire d'un répartiteur de freinage situé sur l'essieu arrière.
- Historique -
- Les grandes dates de l’histoire du frein :
- 1822 : Les premiers systèmes de freins sur les véhicules hippomobiles dates de 1822 surnommé ‘’l’enrayoir Leclerc ‘’ pour bloquer la calèche dans la descente d’une montagne, etc. Exemple : par une chaîne dans les rais de la roue. Il devint obligatoire en 1827 pour les voitures publiques. Puis vint le système avec un sabot. Le sabot « consiste en une pièce de fer recourbée en avant et portant deux oreilles latérales… Lorsque qu’on veut enrayer la roue, il suffit de placer le sabot en avant de la roue de telle sorte que celle-ci monte d’elle-même sur ce petit traîneau qui continuera le mouvement de la roue en le transformant en glissement. »
- En 1879, Binder proposa de remplacer volant ou manivelle par un frein à levier, crémaillère et cliquet. Vers cette époque, d’autres systèmes agissant sur le moyeu par l’enroulement de cordes sont proposés.
- A l’origine, le freinage d’une voiture consistait à passer une barre de bois entre les rayons pour bloquer les roues et donc ralentir la voiture en la faisant glisser sur les jantes.
«Enrayer : arrêter une roue par les rais en sorte qu’elle ne tourne point, mais qu’elle ne fasse que glisser…., passer une pièce de bois entre les deux roues…ou les enlier avec une corde pour empêcher qu’elles ne roulent et retarder leur mouvement à la descente d’une montagne » -Furetière- 1697.
- Mettre ainsi une « perche » (nommée « enrayoir ») agissant sur les rais, a donné naissance au terme ; enrayer ( le terme se trouve déjà dans les textes de R Estienne, en 1552, et J Thierry, en 1564) Par la suite, "enrayer" est devenu, dans un premier temps, le terme générique de tout mode de retenue d’une voiture hippomobile s'élargissant ensuite progressivement au freinage de divers dispositifs mécaniques.
- Ce moyen radical pouvait entraîner la détérioration des rais ce qui amena l'invention d’autres innovations moins fragilisantes pour la roue, par exemple lier, par une chaîne, la jante de la roue à la caisse.
- Freins à tambour (hippomobiles)
- La seule solution d’enraiement pendant des siècles fut la mise en place de sabots sous les roues. En 1851, un carrossier anglais Bascomb présenta une voiture équipée d’un système de frein à patin actionné par un volant, à l’Exposition universelle de Londres. En 1852, Mühlbacher frères (grand carrossier) obtint une médaille d’honneur à l’Exposition Universelle de Paris pour un break équipé d’une machine à enrayer. En 1879, Binder proposa de remplacer volant ou manivelle par un frein à levier, crémaillère et cliquet.
- Vers cette époque, d’autres systèmes agissant sur le moyeu par l’enroulement de cordes sont proposés.
- La maison « Mülhbacher » est qualifiée par le guide du carrossier en 1889 comme la maison «la plus ancienne…. la plus grande de Paris ». Elle fut créée en 1797 par Godefroy (Georges-Geoffroy) Mühlbacher, né à Strasbourg en 1767, d’une famille originaire du duché de Wurtemberg. Il s’installa à Paris comme charron, au 14, rue de la planche, à partir de 1814. Pendant prés de 120 ans, cette maison fut un des fleurons de la carrosserie parisienne. La maison ¨Mühlbacher fut rachetée par "Belvalette" (1804-1933) En 1845, l’écossais William Thomson dépose un brevet de « roue à air », confectionnée à partir de plusieurs épaisseurs de toile de caoutchouc recouvertes de cuir et fixées par des boulons sur une jante de bois. Cette roue ne sera pas opérationnelle. Il fallut attendre 1871 pour voir la fabrication de tuyaux en caoutchouc par Continental, et en 1872 par Pirelli. En 1888, John Boyd Dunlop (1840-1921) invente un pneumatique pour vélo (chambre de caoutchouc avec une enveloppe de coton, elle est gonflée d’air et « collée » sur une jante en bois) Elle sera utilisée dans les compétitions cyclistes dés 1889. Le premier fiacre à roue à bandage pneumatique roule à Paris en 1896.
- Autre système à enroulement, le "Frein automatique stop" fixé sur les traits. La détente de ceux ci dans les descentes mettait en action le dispositif.
- Il faudra attendre le début du XXe siècle pour voir apparaître le frein à tambour, dont l’invention en France est attribuée à Louis Renault (1877-1944) en 1902.
- Avec l'apparition du bandage caoutchouc (1888), puis du pneumatique, le patin de freinage intègre la roue arrière dans un tambour.
- D'abord monté sur l'essieu arrière, le tambour gagnera rapidement les roues avants.
- L'automobile naissante du début du siècle freinait comme les "carrioles" et les trains c'est à dire, un patin de bois serré sur le cerclage métallique d'une roue en bois !
- Le bandage caoutchouc sur une roue en fer, puis, le pneu, ont rejeté le frein dans un tambour, nettement plus efficace, au point qu'il existe encore à l'arrière d'une majorité de voitures. Ces véhicules étaient juste pourvus de 2 freins arrière à tambours. Ceux-ci étaient très petits. (Ford T (1908-1927) par exemple)
- Deux demi-segments en métal à l'intérieur du tambour étaient actionnés par un câble relié à une pédale, voire un simple levier manuel. Il n'y avait bien entendu aucune obligation ni législation! ...
- Très vite, la vitesse des véhicules évoluant avec la puissance des moteurs, ce freinage devint obsolète. Les ingénieurs de l'époque, après quelques nuits blanches et quelques incidents, ont mis au point le freinage hydraulique sur les 4 roues, toujours avec des tambours, mais avec un matériau composite métal/amiante/ bf (toile bakélisée) pour les demi- segments.
- Bf : Beaucoup plus connue sous l'appellation commerciale CELORON, il s'agit d'un matériau composite qui est une combinaison d'une matrice : résine phénolique (bakélite) et d'un support : toile coton. Il existe d'autres nuances en fonction du support : papier, bois, qualité de la toile coton.
- Caractéristiques principales du céloron :
- Bonne résistance mécanique.
- Résistant à l'usure avec une bonne élasticité.
- Absence de grippage même à sec.
- Diminution du bruit (engrenages)
- Bon isolant électrique.
- ( Dans le domaine d'expression anglo-saxon, ce matériau est connu sous le nom de Tufnol en 1924 (Parfois orthographié Tuphnol ou encore novotext) - Usine à Birmingham Royaume-Uni.
- Fin 1923, lancement en série du freinage hydraulique sur les 4 roues, généralement sur 6 cylindres Chrysler ; puis adoption se généralisant au cours des années 20 (freins Lockheed - Tracta 1928) Le freinage s'effectuait par l'intermédiaire de tambours aux 4 roues. Ceux-ci grossissaient jusqu'à remplir totalement la roue. Ils étaient souvent en alliage et comportaient des ailettes de refroidissement.
- Tracta : 1927-1958- J.-A. Grégoire. (1899-1992) - Le joint Tracta est un double cardan sphérique breveté le 8 décembre 1926 par Pierre Fenaille, associé de J.-A. Grégoire, puis industrialisé par la société Tracta. - C'est un joint homocinétique (adjectif inventé à cette occasion) qui fut utilisé dans la construction des premières automobiles européennes à traction avant.
- Le joint Tracta a été adopté par différentes marques, dont DKW entre 1929 et 1936 et Adler de 1932 à 1939, ainsi que sur la plupart des voitures conçues par J.-A. Grégoire. On le retrouve dans de nombreux véhicules militaires de la Seconde Guerre mondiale : Laffly et Panhard en France, Alvis et Daimler au Royaume-Uni et Willys aux États-Unis qui monta le joint Tracta dans un quart de million de jeeps et nombreux autres véhicules. Ce succès se confirma après la guerre, dans les premiers modèles de Land Rover.
- Freins pour les voitures : Les grandes dates du freinage.
* 1902 : Freins à tambour – Attribué à Louis Renault
* 1902 : Freins à disque brevetés par F.W. Lanschester- 1868-1946 - (G.B)
* 1903 : freins sur roues avant (VAN HOOYDONK)
* 1904 : 1ère voiture à pétrole pourvu de freins (à air comprimé) sur les 4 roues (voiture Charley sur châssis Mercedes)
* 1910 : brevet du frein hydraulique (WEIGHT)
* 1911 : 1er freinage sur les 4 roues.
* 1912 : frein à main sur Isetta Fraschini.
* 1919 : 1er frein à commande hydraulique : Lockheed.
* 1921 : Dépôt du brevet de servo-frein par Renault
* 1923 : (fin 1923) Lancement des freins hydrauliques sur les 4 roues.
* 1926 : Les freins à tambours Adoption universelle après 1926 ...
* 193* : Début des années 30 les freins auto-serreurs Bendix
* 1936 : les prémices de l’ABS. Agit sur les freins en évitant leur blocage par légers freinages successifs. Un dispositif dont les prémices remontent à 1936
* 1951 : Apparition du frein à disque sur Jaguar en compétition
* 1953 : Apparition du frein à disque (lancé en série sur la DS 19 CITROËN en 1955) Course : 24 Heures du Mans en 1953- sur Type C (britannique) 1ère place et la 2e place en 1954
* 1960 : Montage en série des freins hydrauliques à tambours sur les 4 roues.
* 1969 : Honda CB 750 Four de 1969, qui a imposé le disque à commande hydraulique puis en compétition.
* 1973 : L'invention de l'ABS par Bosch
* 2000 : Vers les années 2000, la suppression de l'amiante contenu dans les plaquettes.
* 2003 : Mercedes Benz innove en proposant des disques de freins en céramique.
* 20** : Bosch prévoit prochainement un freinage électrique, une réponse plus rapide au freinage, sans l’utilisation du DOT très corrosif…Concrètement, le frein ne serait plus actionné par un circuit hydraulique et par des maître cylindres, mais par une commande électrique reliée à un système informatique, qui pourrait même être paramétrable, laissant ainsi le choix du "ressenti" à la pédale.
- Frein à bande :
- C’est un système extrêmement simple de construction. Au début, il est constitué d’une bande de feuillard d’acier entourant la jante d’une poulie en fonte. A partir des années 1910, cette bande est recouverte d’une garniture de friction. Le gros avantage du frein à bande est que, dans sa grande simplicité, la poulie en tournant a tendance à entraîner la bande dès que, par la commande, on applique cette dernière sur la poulie. Plus la poulie tourne, plus la bande est entraînée et plus elle serre. C’est de que l’on appelle un frein auto-serreur.
- Un des inconvénients est un certain manque de progressivité et dans le freinage. Il apparaît également une usure assez rapide de l’ensemble. De plus, il existe une presque totale inefficacité en marche arrière, le phénomène d’auto-serrage jouant en sens inverse. Cependant le frein à bande a le gros avantage d’assez bien évacuer la chaleur dans l’atmosphère. Des systèmes archaïques inadaptés à des puissances élevées. C'est pour cela que des constructeurs, comme Ford, ont créé sur la Model T un système de ruban s'enroulant sur un tambour dans la transmission. Mais là encore, l'endurance du freinage manquait, tout comme le mordant. La transition vers un système plus fiable était inéluctable et devait être mise au point.
- Correct pour l’époque - entretien facile – peut coûteux
- Inconvénients : Freinage médiocre – Usure rapide – Dangereux-
- Freins à tambours :
- Du plus simple (frein ordinaire) au plus sophistiqué :
- D'abord monté sur l'essieu arrière, soit par des tambours et segments agissant directement sur le moyeu des roues, soit par un simple tambour muni de segments placés sur l’arbre secondaire de la boîte de vitesses et freinant la transmission. Il gagnera rapidement les roues avants. Son adoption sera universelle après 1926. Dès les débuts, la commande de freinage se fait par des câbles, une simple tringle, actionnés à la main ou par une pédale. Les freins à tambours grossiront jusqu'à remplir totalement l'intérieur de la roue, s'équiperont d'ailettes de refroidissement et seront en fonte, en alliage.
- Types de frein à tambour:
- Frein ordinaire :
- Combien de mécaniciens se sont acharnés pour régler des freins datant des années d’avant 1950. Je veux parler des freins dont les segments pivotaient sur des axes non réglables. Avec ce système même après avoir remplacé les garnitures et rectifier les tambours, le freinage n’était pas amélioré ou n’était efficace que sous une action énergique du conducteur. C’est en corrigeant les deux défauts de centrage des segments et conception de la came que les constructeurs sont parvenus à concevoir les freins actuels qui, bien réglés et en état, sont merveilleux.
- Il est composé de plusieurs éléments :
- 2 segments de freins, 2 garnitures, 1 tambour, 1 plateau, 2 points d’articulation, 1 came double ou appelée aussi tournevis, 1 ressort de rappel.
- Les freins à tambours genre Renault et Ford :
- Ces deux montages ne diffèrent l’un de l’autre par le système de commande et le procédé d’écartement des segments.
- Dans le système Renault, la came st constituée par un doigt en acier rond, dont les extrémités sont usinées en forme de came, et ces doigts sont montés libres dans un axe. Ce montage permet l’équilibrage des deux segments.
- Dans le système Ford, la came est remplacée par une came en forme de coin monté libre entre les segments. Cette pièce permet également l’équilibrage des segments.
- Dans les deux systèmes les points fixes inférieurs sont supprimés et les segments sont articulés sur des chapes reposant sur une vis de réglage. L’extrémité de la vis de réglage se termine par un cône cannelé. En déplaçant cette vis dans un sens ou dans l’autre, on obtient le rapprochement ou l’écartement des segments par rapport au tambour. Etc…
- Il est composé de plusieurs éléments :
- 2 segments, 2 garnitures, 1 tambour,1 plateau, 2 chapes d’articulation, 4 vis conique et dentée réglable, tournevis ou porte came, 1 came double flottante, 2 galets, 2 axes de galets tournant butée de centrage des segments, ressort de rappel.
- Pour gagner en efficacité, beaucoup de solutions furent imaginées, Duo-servo, twin-plex, Hcsf, etc… ......
- De nos jours tous les freins à tambours montés sur nos autos sont de type "Segments flottants" et équipés de rattrapage automatique de l'usure.
Ce montage permet un auto-centrage des segments lors du freinage, un nombre de pièces limité, une facilité de montage-démontage sans oublier une répartition des forces de freinages la plus favorable. On parlera de segment "Comprimé" et de segment "Tendu" nommés ainsi en fonction du sens de rotation de la roue.
- Fonctionnement :
- Le frein à tambour est solidaire de la roue mais la différence c'est que le système est encapsulé et inaccessible. Il se compose de 2 mâchoires -ou segments- qui s'écartent. Sur leur face extérieure se trouve la garniture qui vient frotter contre l'intérieur du tambour.
Les segments sont actionnés par l'intermédiaire d'un cylindre hydraulique de réception. Le fameux cylindre de roue!. Le frein à tambour a une efficacité élevée - Coefficient d'auto- serrage dès la mise en pression, mais celui-ci chute très rapidement sous l'influence de la vitesse. Pour augmenter l’efficacité du freinage, les segments sont garnis, sur leur diamètre extérieur, d’une bande frottement en matière spéciale à base d’amiante tressée avec du fil de laiton ou de plomb.
- Freins à tambours :
- Ses avantages - - Ses inconvénients -
Efficacité : Déformation :
Coût Manque de progressivité
Rayon frotté important Refroidissement insuffisant
Protection à l'eau, à la boue Ventilation faible (poussière)
Flux thermique (faible usure) Manque de stabilité
- Le gros inconvénient du frein à tambour est qu’il est conçu comme un véritable four et qu’il dissipe très mal la chaleur. Sa partie la plus chaude étant la partie interne, la chaleur dégagée par le freinage doit traverser la paroi du tambour pour pouvoir se dissiper dans l’atmosphère. Les tambours à ailettes tentent de remédier à cet inconvénient.
- Une température excessive du système amène tout d’abord une grande diminution du coefficient de frottement des garnitures. Il en résulte une diminution de plus en plus importante de l’efficacité du freinage. Si l’on insiste encore plus, les organes de freinage peuvent passer au rouge avec des conséquences graves. On peut alors constater des déformations des tambours, des grillages des garnitures et même la détérioration des joints à lèvres des moyeux. On peut même en arriver à la vaporisation de la graisse et l’usure prématurée des roulements. Ce scénario était souvent constaté dans la descente de cols alpins au cours d’épreuves sportives dans les années 50.
- Avec ses qualités et ses défauts, le tambour présente aujourd'hui une solution satisfaisante. Ce qui explique que l'on en trouve sur la grande majorité des petites autos, même équipées de système ABS, le frein à main est intégré au tambour. Ces mêmes défauts expliquent aussi pourquoi les freins à tambours ont été détrônés rapidement par les freins à disques pour l'essieu avant.
- Frein auto-serreur Bendix :
- Au début des années 30 apparurent les freins auto-serreurs Bendix. Ils se répandirent rapidement sur les Matford (1934/1940), Citroën, Peugeot, jusqu’à la génération de la commande hydraulique. Les 4 freins sont commandés par câbles.
- Le principe de ce type de frein est qu’une seule mâchoire est plaquée contre le tambour par la came de serrage. Cette mâchoire a tendance a être entraînée par le tambour. C’est ce déplacement minime qui provoque le serrage de la seconde mâchoire dont la dernière extrémité s’appuie sur un point fixe.
- Les avantages de ce système sont multiples : Tout d’abord, il y a un très bon phénomène d’auto-serrage diminuant beaucoup l’effort demandé au pilote. Mais également, le mécanicien trouve avec une très grande facilité un centrage correct pour les garnitures. N’ayant qu’un seul point fixe, le réglage est nettement plus rapide. Le démontage de ces freins s’effectue, à très peu de choses près. Seulement, ici, lorsque que les 3 ressorts de rappel et ceux de positionnement sont enlevés, plus rien ne retient les mâchoires. Faire attention au remontage les ressorts sont de longueurs et de forces différentes, la came de commande est formée d’un levier ouvert en forme de chape se montant à cheval sur un point fixe. Bien repérer le sens de montage des différents éléments. L’ensemble se comportait alors, comme un frein à 4 mâchoires, ce qui provoquait également un phénomène d’auto-serrage. Ces freins pouvaient être très puissants même si, très souvent, ils étaient difficiles à équilibrer avec des commandes par câbles.
- Il est composé de plusieurs éléments :
- 1 tambour de frein, 1 plateau, 2 demi segments, 2 demi-segments auto-serreur, garnitures, 1 point fixe repos commun des segments, 1 levier de commande formant came double flottante, 1 câble, 1 chape de réglage filetée à droite, 1 chape filetée à gauche, 1 écrou denté, ressort de rappel, 1 ressort faible de rappel du segment auto-serreur, ressort fort du segment de serrage, excentrique de centrage de l’ensemble du mécanisme.
- Le réglage est assez pointu, il faut régler en mettant une cale de bois de 2 à 3 cm d’épaisseur sous la pédale. Régler les mâchoires pour quelles viennent lécher les tambours avec l’aide des molettes, sur les 4 roues. Détendre les câbles de freins pour qu’ils soient uniformément serrés, etc. Le serrage doit être uniforme dans les deux sens en tournant la roue à la main. Il faut mieux avoir les câbles lâches, du moment qu’ils sont réglés à la même longueur et que les segments doivent être le plus rapprochés possibles des tambours. 9 fois sur dix ces freins accrochent par ce que les câbles sont trop tendus au moment du réglage. Faire un essai routier et corriger si besoin est. Le problème principal est : Les câbles ont toujours tendances à s’allonger ce qui provoquera un certain déséquilibre dans le freinage. Ce problème était récurant sur la Rosalie C4/C6G de 1932.
( Matford : Accor de Mathis (Alsacien) et de Ford SAF. Production française du V8 à soupapes latérales, donc pas de culbuteurs de 60 ch SAE)
- Recommandation : (extrait du manuel)
- Pour conserver la souplesse à ces freins, il est indispensable que les câbles coulissent très librement dans leur gaine. Au cours d’une révision, vous devez appliquer au nettoyage et aux graissages des câbles, même ceux dont les gaines sont munies d’un graisseur. Pour cela, débranchez-les, et tirez-les le plus possible en dehors de leurs gaines. Pour bien les nettoyer, faites-les marcher plusieurs fois avec du pétrole et remontez-les très largement huilés. Etc…
- Le freinage hydraulique :
- Ce nouveau mode de commande fut inventé en 1919 par la firme américaine Lockeed. La première auto à en bénéficier était une Rolland-Pilain (1905-1932), préparée pour le Grand Prix de l'ACF, 1914 à Lyon.
- Fini les câbles ... la transmission de l'effort à la pédale de frein se fait avec de l'huile (le Lockeed) dans des petits tuyaux jusqu'aux tambours ou aux disques.
- Derrière la pédale, un maître cylindre distribue aux cylindres récepteurs grâce à de l'huile très fluide, la pression de la pédale de frein. Cette distribution est répartie, environ 70% à l'avant et 30% à l'arrière, suivant la charge du véhicule, par l'intermédiaire d'un répartiteur de freinage situé sur l'essieu arrière.
- Le circuit est composé d’une pompe commandé par la pédale de frein. A la sortie de la pompe sont branchées quatre canalisations qui amènent le liquide dans les cylindres, placé sur chaque roue. Ces cylindres commandent les segments de frein par l’intermédiaire de deux pistons indépendants. Le maître cylindre ou pompe se compose d’un cylindre ou corps de pompe, dans lequel un piston actionné par la pédale comprime le liquide au travers des canalisations simultanément dans les quatre cylindres. Le maître cylindre est alimenté par un réservoir à liquide qui est en communication avec lui, lorsque le piston est au repos. Ce réservoir sert de détente au liquide en cas de dilatation, etc.
- Le maître cylindre de frein d’une Opel Rekord ( 1954-1955) est composé de :
- Chape, contre-écrou, tige poussoir, soufflets de caoutchouc, corps du maître-cylindre, orifice d’alimentation, bouchon, joint d’étanchéité, orifice de compensation,boîtier du clapet de pression résiduelle, filetage destiné à recevoir l’écrou qui fixe le corps du maître-cylindre sur la traverse de soubassement de carrosserie, siège du clapet de pression résiduelle, coupelle de caoutchouc pour le clapet de pression résiduelle, ressort du piston et du clapet, siège du ressort, coupelle primaire du piston, plaquette formant clapet du piston, piston, coupelle secondaire du piston, rondelle de butée, jonc d’arrêt.
- Le tambour de frein :
- Il est composé de plusieurs éléments :
- 1 tambour, 1 plateau, 2 garnitures, 2 segments, 2 bagues excentrées, 1 ressort de rappel, 2 excentriques de réglage, cylindre composé de 2 pistons, de 2 poussoirs, 1 arrivée du liquide, 1 vis de purge avec son capuchon de caoutchouc.
- L'assistance de freinage ou servo-frein :
- Son rôle est d'amplifier l'effort de freinage.
- Première application commerciale sur la Renault 40 en 1921. Il a été "vulgarisé" progressivement (servo-frein à dépression) à partir de 1961 (Mercedes) D'autres modes d'amplification avaient été inventés auparavant mais la simplicité et le faible coût du servo à dépression lui donneront l'avantage.
- Le frein auto-serreur Bendix sera amélioré en passant du frein à câble au frein hydraulique. Il sera monté sur les voitures de luxe : Delage (1905-1953), etc.
- Fonctionnement :
- Le système utilise la dépression située dans la pipe d'admission du moteur pour accentuer l'effort du freinage, par l'intermédiaire d'une petite bombonne (mastervac) située derrière le maître cylindre. Cette capacité est constituée de 2 demi-coquilles métalliques assemblées hermétiquement.
- Dans cet ensemble on trouve : le piston moteur, le diaphragme et le ressort. Le maître-cylindre est fixé sur la face extérieure du servo-frein et assure l'étanchéité de l'ensemble. Le piston moteur est soit directement actionné par la pédale de frein (Mastervac) soit par l'intermédiaire d'une canalisation hydraulique (Hydrovac) Tous les véhicules actuels utilisent des Mastervac. L'amplification est fixée par le constructeur après calculs et essais des divers composants du système de freinage. On le nomme "Ratio"ou Rapport d'amplification.
- Aujourd'hui d'autres formes d'assistance voient le jour, le freinage EHB par ex. (Electro-Hydraulic Brake) système commercialisé sur la Mercedes classe E.
- La principale évolution du servo-frein est survenue très récemment avec l'arrivée des AFU, BAS, DBC etc… et autres appellations barbares. Le principe de base est d'utiliser toute la puissance disponible du servo-frein le plus rapidement possible en cas de freinage d'urgence et tout ça grâce à l'électronique qui détectera un appui rapide sur la pédale.
- La disparition de l'amplification de freinage telle que nous la connaissons est programmée, car l'avènement du freinage électrique et électronique (Brake By Wire) est pour bientôt.
- Freins à disques :
- Toutes sortes de matériaux peuvent être utilisées.
- Pour les disques :
- Acier inoxydable (assez cher, peu accrocheur)
- Fonte (le plus économique, rouille aisément, le plus lourd, le plus utilisé)
- Carbone (cher, extrêmement léger, particulièrement endurant, efficace principalement à haute température, réservé à la compétition ou sur des véhicules de sport de particulièrement haut de gamme)
- Les plaquettes sont le plus souvent constituées d'un support en acier, assurant la fixation dans les étriers, sur lequel est fixé par collage un patin en matériau composite, s'usant progressivement au cours de l'usage. La composition du patin fluctue suivant le matériau du disque et suivant les fabricants. L'amiante a été longtemps utilisé dans la composition de ces patins et elle y est désormais interdite.
- Types d'étriers :
- Fixe :
2, 4, 6 voire à 8 pistons. L'étrier est fixé solidairement à la fusée, est composé d'une seule pièce. C'est le mouvement des pistons (poussés par le liquide hydraulique), qui permettent aux plaquettes de venir serrer le rotor.
- Flottant :
- 1 ou 2 pistons L'étrier se compose de deux pièces. La chape fixée sur la fusée et la pince articulée sur la chape par l'intermédiaire de colonnettes. Lors d'un freinage, le piston est poussé par le liquide contre la plaquette intérieure et par réaction d'équilibre, la pince coulisse sur les colonnettes et vient à son tour appuyer la plaquette extérieure sur le rotor.
- Dans chaque configuration d'étrier, on trouve deux types de disques : Plein ou Ventilé Le disque ventilé comme son nom l'indique permet un meilleur refroidissement et du coup une plus grande endurance. Dans certains cas, la forme des ailettes internes est optimisée pour accroître encore le refroidissement.
- L'évolution vers le disque en céramique est déjà prête, puisque quelques voitures de prestige en sont équipées (Porsche, Mercedes) Cette technologie accroît la résistance à la chaleur, 1400°C pour 900 / 1000°c actuels, reste insensible à la corrosion, de plus le coefficient de frottement reste stable.
Avantages/Inconvénients :
- Comparer au frein à tambour, le frein à disque a l'avantage d'être plus progressif car il n'est pas auto-serrant. Par contre, il nécessite une plus grande pression pour être efficace, la pression du conducteur est transmise par un dispositif hydraulique fréquemment assisté (c'est pourquoi la commande en est rarement mécanique, car il est malcommode d'obtenir une démultiplication suffisante par un dispositif de leviers)
Sensibilité à l'eau :
- Le disque est perforé, l'étrier est à double piston. La commande est hydraulique.
Généralement, le frein à disque fonctionne à l'air libre, ce qui lui permet d'évacuer les calories du freinage par ses deux faces. Par contre, cela l'expose aux projections d'eau, ce qui provoque un retard au freinage quand il est mouillé (obligation de le sécher en quelques tours avant de récupérer le mordant) Pour contrer cet ennui, il est habituel de perforer les disques des motos de nombreux trous conçus pour rompre le film liquide.
- L'ABS :
- L'anti-blocage des roues dans un freinage d'urgence, est mis au point par Bosch en 1973, puis est monté sur les voitures de haute gamme en 1978 (sur la classe S de Mercedes) et petit à petit sur les voitures de série vers 1990.
- C'est un système électronique constitué d'un calculateur relié électriquement à un répartiteur de freinage hydraulique et de 4 petits capteurs situés sur les tambours ou les disques. Ils contrôlent la rotation de la roue. Si, dans un freinage brutal, la roue vient à bloquer, le capteur transmet immédiatement l'information au calculateur qui relâche la puissance du freinage hydraulique sur cette roue ... On ressent à la pédale des petits à-coups.
- Les matériaux modernes :
- Le remplacement systématique de l'amiante dans les freins sera obligatoire après le 1er janvier 2003 et vous ne pourrez plus changer de carte grise sans montrer "patte blanche" . . .
- Pour bien freiner :
- Un bon freinage se construit dès les premiers dixièmes de seconde. En pratique d'urgence, on freine "fort" d'abord, et on régule ensuite et JAMAIS l'inverse.
- N'oublions pas que le système de freinage requiert une attention particulière pour être toujours efficace, liquide propre, pièces d'origines du constructeur, particulièrement les plaquettes de freins.
- Évitez les plaquettes adaptables :
- Il existe deux types de plaquettes de frein sur le marché : les originales et adaptables. Les secondes coûtant deux fois moins cher que les premières sont néanmoins conçues en matériaux de qualité inférieure. A contrario, les plaquettes originales fabriquées par un fournisseur reconnu ont le mérite de respecter les normes et assurent une sécurité bien plus sûre. Autrement dit, il est primordial d'éviter les plaquettes au prix excessivement bas.
Les plaquettes adaptables ont des caractéristiques techniques légèrement inférieures à celles des pièces d'origine. Ces plaquettes sont moins onéreuses, tout en offrant une performance de freinage convenable. Toutefois, ces plaquettes adaptables sont faites avec des matériaux de qualité inférieure. D'une façon générale, ces plaquettes ne sont pas soumises aux essais nécessaires et ne répondent pas aux normes courantes. Il est essentiel d'éviter les erreurs lors du choix de vos plaquettes: un prix trop bas doit vous alerter.
- Il est indispensable de choisir des plaquettes de frein de bonne qualité et en fonction de votre système de freinage. Nous vous proposons ici un guide pour vous permettre de choisir les meilleures plaquettes de frein en fonction de vos besoins et votre budget. Vous pourrez trouver sur le marché un large éventail de possibilités : pas chers, pour frein arrière, à disque, anti-corrosion... et pour tous les modèles de voiture. Attention à bien vous renseigner avant de changer vos plaquettes de frein.
- Une fois le changement effectué, mieux vaut « rôder » les plaquettes en faisant des freinages modérés pendant quelques dizaines de kilomètres : il y a en effet un risque de « vitrification » des plaquettes. De plus cela permet de bien remettre tout le système de freinage en pression et de laisser le temps aux plaquettes de bien se positionner dans les étriers.
- Bien qu’il soit possible de changer soi-même les plaquettes de frein, mieux vaut faire appel à un professionnel de la réparation automobile. C’est en effet un élément de sécurité très important, mieux vaut éviter un mauvais montage.
Les meilleurs fabricants de plaquettes de frein
- Paramètres principaux des plaquettes de frein
- Température de fonctionnement. Les plaquettes de frein qui résistent à des températures de 300 à 350°C doivent suffire pour une conduite citadine et des vitesses pas trop élevées. Les voitures de sport sont équipées de plaquettes de frein qui peuvent fonctionner à 900°C, mais n'assurent un freinage efficace qu'à partir de 100°C.
- Coefficient de frottement. Les plaquettes avec un coefficient de frottement de 0,25 - 0,35 sont suffisantes pour arrêter un véhicule lors d'une conduite souple. Ce sont les valeurs typiques des pièces équivalentes aux pièces d'origine. Le coefficient de frottement des plaquettes de frein d'origine est légèrement plus élevé, de 0,3 à 0,5. Les plaquettes de frein de sport ont une température de fonctionnement de 150 °C et ont un coefficient de frottement faible - 0,2. Lorsqu'elles sont chaudes, ce coefficient peut atteindre 0,5.
- Durée de vie. La résistance à l'usure des plaquettes dépend des matériaux qui les composent. Les garnitures tendres s'usent plus rapidement, mais des garnitures trop dures provoquent une usure prématurée du disque de frein.
- Les principaux fabricants de plaquettes de frein sont :
- Brembo : Bergame - Italie 1961; Ferodo - chapel-en-le-frith- G.B 1897; Bosch (Robert) Gerlingen- De - 1886 ; ATE -De -1906 ; TRW- 1901 USA – rachète Lucas G.B puis rachetée par en 2002 par Northrop- Grumman ; STARK- De - 2013 ; Textar - De - 1913; Lucas 1874 - GB devient TRW 1999 ; JURID - USA, siège : De - Düsseldorf - 1915 ; Remsa – Corella - Spain –1970, rachetée par TRW en 2000 ; PAGID créée en 1925 - De (Hella Padig Brake systems - Hella De : créée en 1899) Bendix 1927- 2015.
- Les produits de ces fournisseurs diffèrent en prix et en caractéristiques techniques. Les fabricants BREMBO et FERODO produisent des plaquettes de frein pour voitures de sport. Les pièces de l'entreprise ATE sont également capables de supporter de températures d'utilisation pouvant aller jusqu'à 800°C.
- Les plaquettes de frein de TRW, LUCAS, BOSCH, REMSA et STARK sont plus adaptées pour la conduite en ville. Elles ont des spécifications techniques inférieures, mais sont considérablement moins chères. L'entreprise PAGID fabrique des pièces pour voitures de luxe.
- Le fournisseur américain JURID ( Southfield, Michigan, depuis 1899) produit des plaquettes qui sont utilisées par les constructeurs automobiles, mais peuvent également être achetées comme plaquettes adaptables pour des véhicules d'autres marques. Les produits de ce fournisseur sont également commercialisés sous les marques BENDIX-R Pennsylvanie- USA, FRAM-R et PRESTONE -R.
- BREMBO : Un leader en compétition
- Les compétences technologiques exceptionnelles de Brembo sont consacrées en 1975,
lorsque le patron de Maranello, Enzo Ferrari, fait confiance à l’entreprise de Bergame pour
s’occuper des systèmes de freinage de la plus prestigieuse des Formules 1. Brembo devient
alors très vite leader dans les systèmes de freinage en compétition. Depuis, les écuries
équipées de freins Brembo ont gagné des centaines de championnats du monde de course
auto et moto.
- Innovation et stratégie : étriers de freins en aluminium
- Dans le cadre d’une stratégie d’expansion ciblant des marchés de niche – voitures et motos
de compétition – Brembo commence, au début des années 80, à développer des produits et
des procédés technologiques innovants. En 1980, la société ajoute à sa gamme un étrier de
frein disposant d’un design particulièrement innovant et fabriqué dans un nouveau matériel –
l’aluminium. Progressivement, ces nouveaux étriers en aluminium sont adoptés par des
Fabriquant de voitures sportives, tels que Porsche (aujourd’hui encore fourni à 100% par
Brembo), Mercedes, Lancia, BMW, Nissan, et Chrysler.
Au milieu des années 80, Brembo décide d’entrer sur le segment des disques de frein pour
véhicules industriels, et devient rapidement un fournisseur stratégique d’Iveco, Renault,
Trucks et Mercedes.
2013 - Brembo remporte pour la septième fois le trophée de Meilleure Marque de Motorrad,
Auto Motor und Sport, Auto Bild et PS Magazin.
Brembo est récompensé pour les meilleurs standards de qualité de l’industrie automobile
par le trophée 2013 de Supplier Quality Excellence de General Motor’s.
De plus, à l’occasion de la première edition du Sustainability Supplier of the Year Award de
Fiat-Chrysler, Brembo est reconnu fournisseur durable de l’année 2012. Etc…
- Rappel : - Lorsque vous devez choisir des plaquettes de frein, il est essentiel de prendre en compte non seulement la popularité de la marque, mais aussi les spécifications techniques qui doivent être adaptées à votre style de conduite et aux conditions d'utilisation du véhicule. Ce n'est qu'en faisant attention à tous ces détails que vous pourrez choisir des pièces fiables et durables.
- LD
Daniel- Messages : 544
Date d'inscription : 22/04/2012
Age : 81
Localisation : Paris Ouest
Opeldel aime ce message
Re: restauration moteur ancien opel des années 60
Bonjour
Vous allez dans le forum ‘’Atelier’’ restauration moteurs anciens Opel des années 60
(8397 vues) Je vous explique en 7 pages une grande partie des réparations des Opel en 4 et 6 cylindres. Ceci d’après les manuels d’ateliers d’OPEL.
Si vous avez voir ou revoir la voiture vérifier les faux longerons avant la tôle recouvrant le longeron en forme de U pourrit facilement, l’eau pénètre et continu son chemin jusqu’au niveau du pont et faire pourrir le bas de caisse. Classique, le plancher avant se perce dans une multitude d’endroits. Prévoir un plancher. Dans le coffre vérifier les passages des roues qui sont bouffées par l’eau. Dans la poutre avant supportant le train tous les caoutchoucs sont à changer, il n’existe plus en pièces services depuis 1994. Il faudra les refabriquer vous-même. J’ai donné une façon des les réaliser par vos propres moyens. Vous verrez en même temps que les axes des pistons ne sont pas centrés ! voir explication. Il faudra prévoir un kit complet de restauration moteur, pont boîte, etc. Si le moteur n’a pas tourné depuis des lustres, n’essayez pas de le remettre en route : la crépine du filtre à huile est sûrement bouchée ainsi que les transferts. L’arbre supportant les culbuteurs sont bouchés, plus de graissage, etc. Les 3 moteurs que j’ai récupéré étaient bouchés par l’huile figée, plus de graissage des culbuteurs, certains arrivent à se souder sur l’arbre : Le moteur est donc bloqué. Il faut déculasser pour voir s’il y a la rotation des pistons. Ce que vous pouvez faire c’est juste de voir si le moteur n’est pas bloqué. Pour les freins très, très fragile, ils sont HS : Coupelles maître cylindre,durits, (compter 1.000 Euros) 1 An de non fonctionnement des freins et les fuites sont assurées. Un pignon en céloron + le pignon en métal pour l’arbre à cames (il faut impérativement changer les 2 sans quoi l’un détruira l’autre rapidement ) 350 Euros. Voir le jeu dans les fusées, 2 roulements spéciaux, 250 Euros pièce, les 2 autres moins chères. Rotules de direction, 150 Euros pièce. Faites baisser le prix au maximum si vous l’acheter en lui expliquant les problèmes que vous allez trouver de suite. Avec cela vous avez assez d’arguments en votre faveur. La cote en état de marche et passé au contrôle technique est de 7000 Euros, sans corrosion perforante. Si le moteur est bloqué c’est 200 à 300 Euros maximum. Tout dépend aussi du niveau de restaurations, le suivi de la voiture, si c’est une première main, factures depuis l’achat du véhicule, s’il y a eu un expert qui lui en a fixé le prix !… En Allemagne le prix d’occasion en parfait état capable de partir pour toutes distances : Le prix vari de 20.000 à + 40.000 Euros en parfait état (concours) Si votre vendeur possède les factures vérifier le compteur kilomètres – 6 chiffres seulement : il repasse à zéro à 99.999. Donc le compteur peut avoir passé plusieurs fois la remise à zéro. Voir l’usure du caoutchouc des pédales et son usure de la pédale en soulevant le caoutchouc, bas des portières, etc …
LD – Bonne chance -
Vous allez dans le forum ‘’Atelier’’ restauration moteurs anciens Opel des années 60
(8397 vues) Je vous explique en 7 pages une grande partie des réparations des Opel en 4 et 6 cylindres. Ceci d’après les manuels d’ateliers d’OPEL.
Si vous avez voir ou revoir la voiture vérifier les faux longerons avant la tôle recouvrant le longeron en forme de U pourrit facilement, l’eau pénètre et continu son chemin jusqu’au niveau du pont et faire pourrir le bas de caisse. Classique, le plancher avant se perce dans une multitude d’endroits. Prévoir un plancher. Dans le coffre vérifier les passages des roues qui sont bouffées par l’eau. Dans la poutre avant supportant le train tous les caoutchoucs sont à changer, il n’existe plus en pièces services depuis 1994. Il faudra les refabriquer vous-même. J’ai donné une façon des les réaliser par vos propres moyens. Vous verrez en même temps que les axes des pistons ne sont pas centrés ! voir explication. Il faudra prévoir un kit complet de restauration moteur, pont boîte, etc. Si le moteur n’a pas tourné depuis des lustres, n’essayez pas de le remettre en route : la crépine du filtre à huile est sûrement bouchée ainsi que les transferts. L’arbre supportant les culbuteurs sont bouchés, plus de graissage, etc. Les 3 moteurs que j’ai récupéré étaient bouchés par l’huile figée, plus de graissage des culbuteurs, certains arrivent à se souder sur l’arbre : Le moteur est donc bloqué. Il faut déculasser pour voir s’il y a la rotation des pistons. Ce que vous pouvez faire c’est juste de voir si le moteur n’est pas bloqué. Pour les freins très, très fragile, ils sont HS : Coupelles maître cylindre,durits, (compter 1.000 Euros) 1 An de non fonctionnement des freins et les fuites sont assurées. Un pignon en céloron + le pignon en métal pour l’arbre à cames (il faut impérativement changer les 2 sans quoi l’un détruira l’autre rapidement ) 350 Euros. Voir le jeu dans les fusées, 2 roulements spéciaux, 250 Euros pièce, les 2 autres moins chères. Rotules de direction, 150 Euros pièce. Faites baisser le prix au maximum si vous l’acheter en lui expliquant les problèmes que vous allez trouver de suite. Avec cela vous avez assez d’arguments en votre faveur. La cote en état de marche et passé au contrôle technique est de 7000 Euros, sans corrosion perforante. Si le moteur est bloqué c’est 200 à 300 Euros maximum. Tout dépend aussi du niveau de restaurations, le suivi de la voiture, si c’est une première main, factures depuis l’achat du véhicule, s’il y a eu un expert qui lui en a fixé le prix !… En Allemagne le prix d’occasion en parfait état capable de partir pour toutes distances : Le prix vari de 20.000 à + 40.000 Euros en parfait état (concours) Si votre vendeur possède les factures vérifier le compteur kilomètres – 6 chiffres seulement : il repasse à zéro à 99.999. Donc le compteur peut avoir passé plusieurs fois la remise à zéro. Voir l’usure du caoutchouc des pédales et son usure de la pédale en soulevant le caoutchouc, bas des portières, etc …
LD – Bonne chance -
Daniel- Messages : 544
Date d'inscription : 22/04/2012
Age : 81
Localisation : Paris Ouest
Opeldel aime ce message
Re: restauration moteur ancien opel des années 60
- Bonjour
- Pour la fabrication des joints à découper pour nos anciennes.
- Il existe des feuilles en Burasil de différentes épaisseurs de 1 mm et de 1,5 mm, 500x300 mm, 37 Euros. Du feutre, et du liège Nitrile de 1mm à 10 mm, 1000 x 1000 mm, de 5 Euros à X …; du papier pour la membrane rouge en 0,38 mm d’épaisseur, en 20x300 mm, 24 Euros ; du papier indéchirable en 0,5 mm et 1 mm 500x300 mm de 6 Euros à 18 Euros en 500 x600 mm
- Joint plat en liège : Feuille de joint plat en liège caoutchouc (mélange de liège et nitrile) de haute qualité, à découper pour réaliser vos propres joints de pièces moteurs, carburateur, de carter, bouchon de réservoir etc. Le liège mélangé au caoutchouc nitrile donne un joint d'excellente propriété, qui n'absorbe pas, reste souple et résistant.
- Applications : huile, hydrocarbures- Format de la feuille : 475x210 mm - 1 feuille épaisseur 2 mm, 6 Euros - Température maxi : 100 °C - Pression de serrage : basse et moyenne
- Les prix varient suivant les revendeurs, ils peuvent être dégressifs suivant la quantité…
-. Feuille en liège et caoutchouc : Mélanges spéciaux de liège en vrac et un caoutchouc sélectionné sont les matériaux dont nous produisons nos joints en liège-caoutchouc pour tous types de jointures et isolations contre vibrations. Le matériau obtenu est extrêmement souple, résistant mécaniquement et aussi tout à fait résistant à l’action de lubrifiants, huiles, combustibles, gaz et beaucoup d’autres substances chimiques. Il est employé surtout dans la production de joints pour machines, outils et véhicules. L’application de liège-caoutchouc rend possible l’utilisation du pourcentage le plus grand possible de la surface de contact, ainsi que fait augmenter le coefficient de compression ce qui, à son tour, constitue une protection effective contre éventuelles déformations, fuites ou manque d’étanchéité. Les joints en liège-caoutchouc sont conçues, confectionnées et testées en sorte qu’ils remplissent toutes les exigences pour une utilisation donnée tout en restant hautement économiques et rentables. Le liège-caoutchouc est très résistant en comparaison avec matériaux utilisés dans l’industrie tels que combustibles, lubrifiants, réfrigérants et gaz. Les joints en liège-caoutchouc NC710, NC711, NC711G et UL157 sont notamment dédiés pour les utilisations les plus exigeantes.
- Feuille de joint de liège entoilé pour réservoir d’essence pour joint de carter d'huile - joint de couvre culbuteurs - joints de pompe à essence et de carburateur. Existe en 2, 2,5, 3, 4 mm, 500 x 600 mm, 34 Euros.
- Dans les pochettes d’origine, du constructeur ou repros, que vous trouvez chez des marchands, pour refaire tous les joints de votre moteur, il arrive que les joints en liège deviennent tellement friables en vieillissant, secs, qu’il vous reste dans les mains lors de leur pose. Certains joints sont quasiment introuvables sur le marché. C’est le système ‘’D’’ qu’il faut mettre en œuvre. Emporte-pièce de 2 mm à + de 10 mm, le cutter ou le scalpel, la feuille en papier Kraft, le collant double-face, petit marteau pour en délimiter les contours (empreintes), la bille pour marquer l’emplacement des trous, etc.
LD.
- Pour la fabrication des joints à découper pour nos anciennes.
- Il existe des feuilles en Burasil de différentes épaisseurs de 1 mm et de 1,5 mm, 500x300 mm, 37 Euros. Du feutre, et du liège Nitrile de 1mm à 10 mm, 1000 x 1000 mm, de 5 Euros à X …; du papier pour la membrane rouge en 0,38 mm d’épaisseur, en 20x300 mm, 24 Euros ; du papier indéchirable en 0,5 mm et 1 mm 500x300 mm de 6 Euros à 18 Euros en 500 x600 mm
- Joint plat en liège : Feuille de joint plat en liège caoutchouc (mélange de liège et nitrile) de haute qualité, à découper pour réaliser vos propres joints de pièces moteurs, carburateur, de carter, bouchon de réservoir etc. Le liège mélangé au caoutchouc nitrile donne un joint d'excellente propriété, qui n'absorbe pas, reste souple et résistant.
- Applications : huile, hydrocarbures- Format de la feuille : 475x210 mm - 1 feuille épaisseur 2 mm, 6 Euros - Température maxi : 100 °C - Pression de serrage : basse et moyenne
- Les prix varient suivant les revendeurs, ils peuvent être dégressifs suivant la quantité…
-. Feuille en liège et caoutchouc : Mélanges spéciaux de liège en vrac et un caoutchouc sélectionné sont les matériaux dont nous produisons nos joints en liège-caoutchouc pour tous types de jointures et isolations contre vibrations. Le matériau obtenu est extrêmement souple, résistant mécaniquement et aussi tout à fait résistant à l’action de lubrifiants, huiles, combustibles, gaz et beaucoup d’autres substances chimiques. Il est employé surtout dans la production de joints pour machines, outils et véhicules. L’application de liège-caoutchouc rend possible l’utilisation du pourcentage le plus grand possible de la surface de contact, ainsi que fait augmenter le coefficient de compression ce qui, à son tour, constitue une protection effective contre éventuelles déformations, fuites ou manque d’étanchéité. Les joints en liège-caoutchouc sont conçues, confectionnées et testées en sorte qu’ils remplissent toutes les exigences pour une utilisation donnée tout en restant hautement économiques et rentables. Le liège-caoutchouc est très résistant en comparaison avec matériaux utilisés dans l’industrie tels que combustibles, lubrifiants, réfrigérants et gaz. Les joints en liège-caoutchouc NC710, NC711, NC711G et UL157 sont notamment dédiés pour les utilisations les plus exigeantes.
- Feuille de joint de liège entoilé pour réservoir d’essence pour joint de carter d'huile - joint de couvre culbuteurs - joints de pompe à essence et de carburateur. Existe en 2, 2,5, 3, 4 mm, 500 x 600 mm, 34 Euros.
- Dans les pochettes d’origine, du constructeur ou repros, que vous trouvez chez des marchands, pour refaire tous les joints de votre moteur, il arrive que les joints en liège deviennent tellement friables en vieillissant, secs, qu’il vous reste dans les mains lors de leur pose. Certains joints sont quasiment introuvables sur le marché. C’est le système ‘’D’’ qu’il faut mettre en œuvre. Emporte-pièce de 2 mm à + de 10 mm, le cutter ou le scalpel, la feuille en papier Kraft, le collant double-face, petit marteau pour en délimiter les contours (empreintes), la bille pour marquer l’emplacement des trous, etc.
LD.
Daniel- Messages : 544
Date d'inscription : 22/04/2012
Age : 81
Localisation : Paris Ouest
Opeldel aime ce message
Re: restauration moteur ancien opel des années 60
Bonjour
- D’après le N° inscrit sur le moteur 2,6L jusqu’au N° 26-115545, puis du N° 26-115546 il y a eu plusieurs modifications dans la distribution. L’arbre portant les culbuteurs passe d’un diamètre de 19 mm à un diamètre de 21 mm. Ceci augmente le graissage de tous les culbuteurs. Les trous graissant les culbuteurs sont plus grands en diamètre et les culbuteurs sont renforcés. Donc la rampe de culbuteurs a été changée dans son intégralité. Ceci correspond bien au même phénomène rencontré : mauvais graissage du cylindre 5 et 6. Le culbuteur n’étant plus graissé, il se grippe et le ou les tiges de commande des culbuteurs se torde, les soupapes reste ouverte et brûle, etc. L’huile de sortie de l’arbre allant graissée l’arbre à cames n’est plus lubrifiée. Dans les 2 cas il faut faire sauter les 2 pastilles de l’arbre, soit en 19 mm soit en 21 mm, supportant les culbuteurs car dans 90% des cas elles sont bouchées. Le pignon en celoron rend l’âme. La vie du pignon est moins de 100.000 km
- Jusqu’au N° 26-115545 l’arbre portant les culbuteurs a été monté sur le moteur 2,5L et sur le moteur 2,6L. diamètre de 19 mm
A partir du N° 26-115546 l’arbre portant les culbuteurs a été monté uniquement sur le moteur 2,6L. diamètre de 21 mm
- Le contrôle préconisé pour l’huile du moteur doit être fait tous les 500 km et le changement tous les 3.000 km SAE 20
- Avec le pignon en celoron il n’y a in si dire pas de bruit. Le celoron se détruira au niveau denture s’il y a un blocage lors d’une soupape grillée ‘ qui reste légèrement ouverte. Le celoron est donc le ‘’fusible ‘’ en cas de blocage mécanique. Ce que j’ai constaté sur les 3 moteurs de Kapitän que j’ai démonté. Le problème venait toujours du manque de graissage du tube graissant les culbuteurs sur le cylindre N° 5 ou 6, qui eux se trouvent en fin de course. Le culbuteur s’est grippé sur l’axe. Il n’y a qu ‘une fois ou les tiges du ou des culbuteurs étaient tordus. Circuit d’huile bouché. Le circuit de retour d’huile vers le moteur ne se faisant plus…
- Maintenant il faut voir le problème de diélectrique, galvanique, électrolytique (différence de potentiel), qui va se produire entre le pignon de remplacement (aluminium spécial) et le pignon en métal qui se trouve sur l’axe du vilebrequin. Deux métaux différents = une poudre d’alumine qui va se produire immanquablement. C’est pour cela, que sur les bateaux, coque en métal, In bord, on met une anode en magnésium pour éviter que votre bateau à moteur soit dégradé rapidement, phénomène d’électrolyte, galvanique. Votre bateau servira d’anode sacrificielle, etc.
- N’oublions pas qu’il faut changer les 2 pignons à la fois – Denture droite hélicoïdale. Le pignon en métal en porte les stigmates lors de la rupture + de son usure normale. A chaque fois, les gens oublis de changer les deux, et rapidement, le pignon en celoron sera détruit.
- Il faut donc voir le prix d’usinage des pièces par un spécialiste ! Il faut que le pignon soit usiné et percer, aux même cotes, pour la clavette, et 2 trous pour pouvoir visser la patte fixant l’arbre à cames. Pour la rupture du pignon en aluminium, s’il résiste, la casse peut être dévastatrice…
- Je viens de découvrir que plusieurs pignons Opel, en celoron, ont la même forme, le même nombre de dents (46) La différence se trouve dans la découpe circulaire, de la face interne, une partie concave qui varie de 10 mm à 19 mm en épaisseur. Sur les celoron de fabrications, disons adaptables, le point de calage n’est pas marqué. En plus, il est difficile de trouver le repère « 0 » pour le faire coïncider avec le zéro du pignon en métal. Il faut tracer une ligne droite en partant du centre de l’axe de l’arbre à cames en passant par le milieu de l’encoche de la clavette qui vous donnera le 1er repère sur la pointe d’une dent. De cette dent il faudra compter 8 creux de chaque dent. Arriver à cet endroit (8e creux : base de la dent) vous pourrez marquer votre repère ‘’0’’ pour le calage avec le pignon métallique.
- Vous pouvez vérifier si vous ne vous êtes pas tromper, avec une règle en partant de votre référence ‘’0’’. Il y a 2 gros trous qui servent à boulonner la bride de butée de l’arbre à cames. En partant du creux de la 8e dent ( passant par votre référence ‘’0’’) votre ligne doit passer sur le haut du trou (côté clavette), puis passant par le centre de l’axe de l’arbre à cames, votre ligne doit passer par le bas du trou de gauche qui sert à boulonner la bride de butée de l’arbre à cames.. L’alignement doit être parfait entre ces 4 points. Si non il faut recommencer le processus.
- Pour le pignon métallique il faut faire le même procédé du centre de l’axe du vilebrequin en passant par le milieu de l’encoche de la clavette. Ce qui arrivera sur le creux d’une dent. Vous allez compter, mais, maintenant, dans le sens de rotation anti-horaire, le haut de la dent sera votre point de départ pour le comptage. Vous allez compter 5 dents, la pointe de la dent deviendra le point ‘’0’’. Le repère ‘’0’’ sur les pignons d’arbre à cames et du vilebrequin. Il se peut aussi que les repères soient effacés.
- Suivant les modèles : Olympia – Rekord – Caravan- Delvan- Deivery Van la référence du pignon en celoron est : 636302 de 1953-1958 ‘’P’’
Kapitän : 636302 (kit) Tout modèle 1954 jusqu’au moteur N° 2,5L-54-18961
RP 636-03 (kit)Tout modèle (1954-1958) ‘’P’’ moteur N° 2,5 L-54- 18962 A
Truck R.P 636-02 (kit)
Kapitän ‘’ P’’1 et ‘’ P’’2 limousine et Kapitän – L-P modèle LV 2,5 et 2,6 L - LVL (1958 -1964) et la Kapitän A (1964-1965) en 2,6L R.P 636-03 (Kit) = pignon en celoron + pignon métal + joints
Olympia Rekord LZ - CZ Kit RP.636-04
Kapitän - P modèle LV châssis N° 2.5l 21-831-380 to 1200508 châssis N° 2,6 L 21-1200509 to 2741072
préfixe et sufixe * 2,5 L from engine N° 2.5 -4651*
préfixe et sufixe * 2,6 L from engine N° 2.6 –001* 4 Door Sedan
Kapitän – L-P modèle LVL châssis N° 2,5 l 22-825937 to 1191631
Châssis N° 22-1191632 to 27410
préfixe et sufixe * 2.5 from engine N° *2.5-4651*
préfixe et sufixe * 2.6 from engine N° 26-001* 4- Door de Luxe
- Pour le style de la voiture, c’est autre chose, c’est un autre look incontournable. Le pare brise panoramique qui rentre dans les portières c’est superbe. Genre Chevrolet des années 50, etc…C’est pour cela que je l’ai acheté…sur photos…
- En espérant que ces quelques explications, vous serons utiles.
LD
- D’après le N° inscrit sur le moteur 2,6L jusqu’au N° 26-115545, puis du N° 26-115546 il y a eu plusieurs modifications dans la distribution. L’arbre portant les culbuteurs passe d’un diamètre de 19 mm à un diamètre de 21 mm. Ceci augmente le graissage de tous les culbuteurs. Les trous graissant les culbuteurs sont plus grands en diamètre et les culbuteurs sont renforcés. Donc la rampe de culbuteurs a été changée dans son intégralité. Ceci correspond bien au même phénomène rencontré : mauvais graissage du cylindre 5 et 6. Le culbuteur n’étant plus graissé, il se grippe et le ou les tiges de commande des culbuteurs se torde, les soupapes reste ouverte et brûle, etc. L’huile de sortie de l’arbre allant graissée l’arbre à cames n’est plus lubrifiée. Dans les 2 cas il faut faire sauter les 2 pastilles de l’arbre, soit en 19 mm soit en 21 mm, supportant les culbuteurs car dans 90% des cas elles sont bouchées. Le pignon en celoron rend l’âme. La vie du pignon est moins de 100.000 km
- Jusqu’au N° 26-115545 l’arbre portant les culbuteurs a été monté sur le moteur 2,5L et sur le moteur 2,6L. diamètre de 19 mm
A partir du N° 26-115546 l’arbre portant les culbuteurs a été monté uniquement sur le moteur 2,6L. diamètre de 21 mm
- Le contrôle préconisé pour l’huile du moteur doit être fait tous les 500 km et le changement tous les 3.000 km SAE 20
- Avec le pignon en celoron il n’y a in si dire pas de bruit. Le celoron se détruira au niveau denture s’il y a un blocage lors d’une soupape grillée ‘ qui reste légèrement ouverte. Le celoron est donc le ‘’fusible ‘’ en cas de blocage mécanique. Ce que j’ai constaté sur les 3 moteurs de Kapitän que j’ai démonté. Le problème venait toujours du manque de graissage du tube graissant les culbuteurs sur le cylindre N° 5 ou 6, qui eux se trouvent en fin de course. Le culbuteur s’est grippé sur l’axe. Il n’y a qu ‘une fois ou les tiges du ou des culbuteurs étaient tordus. Circuit d’huile bouché. Le circuit de retour d’huile vers le moteur ne se faisant plus…
- Maintenant il faut voir le problème de diélectrique, galvanique, électrolytique (différence de potentiel), qui va se produire entre le pignon de remplacement (aluminium spécial) et le pignon en métal qui se trouve sur l’axe du vilebrequin. Deux métaux différents = une poudre d’alumine qui va se produire immanquablement. C’est pour cela, que sur les bateaux, coque en métal, In bord, on met une anode en magnésium pour éviter que votre bateau à moteur soit dégradé rapidement, phénomène d’électrolyte, galvanique. Votre bateau servira d’anode sacrificielle, etc.
- N’oublions pas qu’il faut changer les 2 pignons à la fois – Denture droite hélicoïdale. Le pignon en métal en porte les stigmates lors de la rupture + de son usure normale. A chaque fois, les gens oublis de changer les deux, et rapidement, le pignon en celoron sera détruit.
- Il faut donc voir le prix d’usinage des pièces par un spécialiste ! Il faut que le pignon soit usiné et percer, aux même cotes, pour la clavette, et 2 trous pour pouvoir visser la patte fixant l’arbre à cames. Pour la rupture du pignon en aluminium, s’il résiste, la casse peut être dévastatrice…
- Je viens de découvrir que plusieurs pignons Opel, en celoron, ont la même forme, le même nombre de dents (46) La différence se trouve dans la découpe circulaire, de la face interne, une partie concave qui varie de 10 mm à 19 mm en épaisseur. Sur les celoron de fabrications, disons adaptables, le point de calage n’est pas marqué. En plus, il est difficile de trouver le repère « 0 » pour le faire coïncider avec le zéro du pignon en métal. Il faut tracer une ligne droite en partant du centre de l’axe de l’arbre à cames en passant par le milieu de l’encoche de la clavette qui vous donnera le 1er repère sur la pointe d’une dent. De cette dent il faudra compter 8 creux de chaque dent. Arriver à cet endroit (8e creux : base de la dent) vous pourrez marquer votre repère ‘’0’’ pour le calage avec le pignon métallique.
- Vous pouvez vérifier si vous ne vous êtes pas tromper, avec une règle en partant de votre référence ‘’0’’. Il y a 2 gros trous qui servent à boulonner la bride de butée de l’arbre à cames. En partant du creux de la 8e dent ( passant par votre référence ‘’0’’) votre ligne doit passer sur le haut du trou (côté clavette), puis passant par le centre de l’axe de l’arbre à cames, votre ligne doit passer par le bas du trou de gauche qui sert à boulonner la bride de butée de l’arbre à cames.. L’alignement doit être parfait entre ces 4 points. Si non il faut recommencer le processus.
- Pour le pignon métallique il faut faire le même procédé du centre de l’axe du vilebrequin en passant par le milieu de l’encoche de la clavette. Ce qui arrivera sur le creux d’une dent. Vous allez compter, mais, maintenant, dans le sens de rotation anti-horaire, le haut de la dent sera votre point de départ pour le comptage. Vous allez compter 5 dents, la pointe de la dent deviendra le point ‘’0’’. Le repère ‘’0’’ sur les pignons d’arbre à cames et du vilebrequin. Il se peut aussi que les repères soient effacés.
- Suivant les modèles : Olympia – Rekord – Caravan- Delvan- Deivery Van la référence du pignon en celoron est : 636302 de 1953-1958 ‘’P’’
Kapitän : 636302 (kit) Tout modèle 1954 jusqu’au moteur N° 2,5L-54-18961
RP 636-03 (kit)Tout modèle (1954-1958) ‘’P’’ moteur N° 2,5 L-54- 18962 A
Truck R.P 636-02 (kit)
Kapitän ‘’ P’’1 et ‘’ P’’2 limousine et Kapitän – L-P modèle LV 2,5 et 2,6 L - LVL (1958 -1964) et la Kapitän A (1964-1965) en 2,6L R.P 636-03 (Kit) = pignon en celoron + pignon métal + joints
Olympia Rekord LZ - CZ Kit RP.636-04
Kapitän - P modèle LV châssis N° 2.5l 21-831-380 to 1200508 châssis N° 2,6 L 21-1200509 to 2741072
préfixe et sufixe * 2,5 L from engine N° 2.5 -4651*
préfixe et sufixe * 2,6 L from engine N° 2.6 –001* 4 Door Sedan
Kapitän – L-P modèle LVL châssis N° 2,5 l 22-825937 to 1191631
Châssis N° 22-1191632 to 27410
préfixe et sufixe * 2.5 from engine N° *2.5-4651*
préfixe et sufixe * 2.6 from engine N° 26-001* 4- Door de Luxe
- Pour le style de la voiture, c’est autre chose, c’est un autre look incontournable. Le pare brise panoramique qui rentre dans les portières c’est superbe. Genre Chevrolet des années 50, etc…C’est pour cela que je l’ai acheté…sur photos…
- En espérant que ces quelques explications, vous serons utiles.
LD
Daniel- Messages : 544
Date d'inscription : 22/04/2012
Age : 81
Localisation : Paris Ouest
Opeldel aime ce message
Re: restauration moteur ancien opel des années 60
- Etudes sur le freinage -

- Principe de fonctionnement d’un maître cylindre simple :
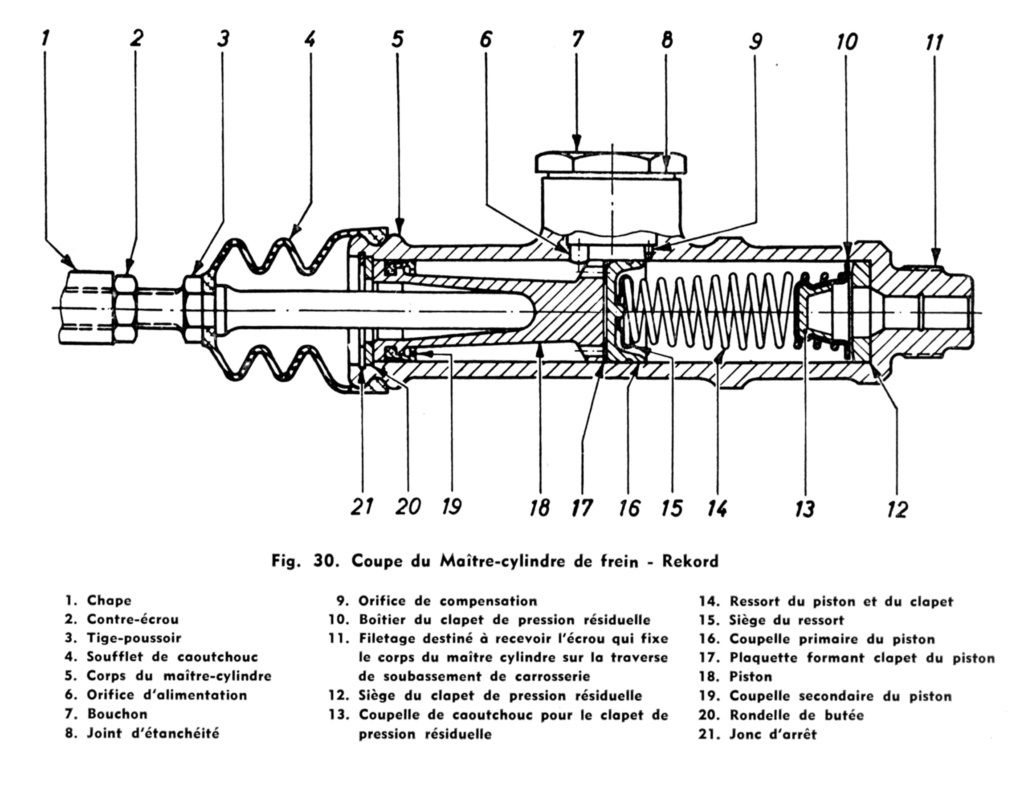





- Le principe de fonctionnement est basé sur le principe de théorème de Pascal : Tout fluide est considéré comme étant incompressible. Toute variation de pression en un point du circuit entraîne la même variation de pression en tout point du circuit. La pression dépend de la force et de la surface sur laquelle est exercée cette force.
- L’INCOMPRESSIBILITÉ DU LIQUIDE
- Si le liquide est compressible, le levier devient spongieux au point d’arriver en butée sans transmettre l’effort aux pistons.
- Lubrification :
- Le liquide utilisé doit participer à la lubrification des pièces mobiles du circuit de freinage (pistons & joints)
- La protection anticorrosion :
C’est le point faible des liquides de freins classiques qui ont tendance à se charger en eau. Les risques sont alors l’oxydation et le grippage des pièces (étriers frein, pistons, etc …). Les formulations intègrent généralement des inhibiteurs de corrosion et d’oxydation.
- Comment le liquide de frein peut-il se contaminer ?
- Le liquide se contamine dés lors que la bouteille est dévissée et ouverte. Le liquide peut donc être contaminé avant même son entrée dans le circuit de freinage. C’est pourquoi, il est nécessaire de conserver le liquide dans un flacon hermétiquement fermé lorsqu’il n’est pas utilisé, l’idéal étant de ne pas réutiliser le flacon ouvert. Privilégiez pour cela l’achat de petits conditionnements.
- L’humidité peut entrer dans le circuit dés lors que le réservoir ou maître cylindre est ouvert.
Les joints et les durites n’étant jamais complètement étanches, l’humidité en infime quantité va être absorbée et c’est pourquoi les fabricants automobiles préconisent la purge du système de freinage tous les deux ans.
- Olympia Rekord, Olympia, Caravan, Fourgonnette de livraison, et Kapitän –
- Le maître cylindre des modèles Olympia et Kapitän sont tous identiques, à la seule exception du raccordement sur le maître cylindre du tuyau d’alimentation en provenance du réservoir de liquide de frein. Sur le modèle Olympia, le tuyau se brancher sur un orifice pratiqué directement dans le corps du maître cylindre. Dans le cas de la Kapitän, ce tuyau aboutit au bouchon fileté. Cette différence n’entraîne pas de modification du procédé à employer pour la révision du maître cylindre, de telle sorte que les instructions valables pour les modèles Olympia le sont aussi pour le modèle Kapitän.
- Sur la Kapitän P il existe une autre forme de maître cylindre. D’autres accessoires peuvent être montés en dérivations : prise sur le bouchon du réservoir transparent, robinet d’arrêt, etc.

- Le fonctionnement : position repos :

- Les trous de dilatation et d’alimentation sont ouverts. La pression est identique dans les deux chambres, le ressort maintien le piston en position repos.
- Le fonctionnement : position freinage :

- L’action du conducteur sur la pédale de frein provoque le déplacement du piston et des coupelles.
- Des que la coupelle primaire obture le trou de dilatation, la chambre de pression devient étanche et la pression peut se créer. Celle-ci dépend de la force du conducteur et de la surface du piston. Le liquide étant incompressible, la pression se retrouve au niveau des récepteurs.
- Le fonctionnement : position de relâchement :

- Le conducteur cesse son action sur la pédale. Le ressort repousse le piston vers sa position de repos. La pression chute dans la chambre de pression.
- La compensation à l’usure :

- Lors du recule du piston, la pression chute dans la chambre de pression (le volume augmente) et augmente dans la chambre d’alimentation (le volume diminue)
- Cette différence de pression entraîne la courbure de la coupelle primaire et le passage du liquide à travers les trous de compression du piston. La quantité de liquide transféré permet de compenser l’usure des (plaquettes) et garnitures de frein.
- A chaque freinage, le niveau de liquide chute dans le réservoir. Un niveau faible peut indiquer une usure importante des freins, il ne faut pas refaire le niveau car lors du remplacement des plaquettes ou garnitures, le fait de repousser les pistons fait remonter le niveau. S’il est trop élevé au départ, il y a risque de fuite (trop plein)
- Inspection interne du maître cylindre.
- Une fois le mécanisme démonté, vous pouvez vérifier que les 2 trous correspondant avec une des chambres ne sont pas obstrués ( 15 et 16, voir sur l’éclaté si-dessous) : La chambre d’alimentation ou la chambre de pression (2 trous d’environ 1mm) avec l’aide d’une lampe torche d’inspection à LED ou en fabriquer une avec une ampoule de tableau de bord (1,5 W) que vous aurez soudé à l’aide de 2 fils.
- Maître cylindre Kapitän P2 avec récipient transparent

.


- Les différents circuits de freinages :
- Depuis 1977 la législation impose l’utilisation de deux circuits indépendants :
- Le circuit en « H »
- Le circuit en « X »
- Les circuits en « H » :

- Les circuits avant et arrière sont séparés.
- Avantage :
- Simplicité du système, la stabilité du véhicule n’est que très peu affectée.
- Les circuits en « X »

- Avantage :
- La perte d’efficacité est de 50%, quelque soit le circuit défaillant.
- Inconvénient :
- En cas de défaillance, la stabilité du véhicule est très affectée
- Il est nécessaire d’utiliser un maître cylindre en tandem avec double réservoir.
- Planches- Frein : Parts catalog - Opel Kapitän P - 2,5 L – 2,6 L - révision décembre 1974-
- Kapitän Panoramique P2 :
- Eclatés pièces détachées, circuit de freinage :


- Tous les éléments marqués d’un astérisque correspondent à des modèles en Kapitän Panoramique P, soit 2,5 L ou en 2,6L d’entrée de gamme.
- Double pistons uniquement sur le train avant de la Kapitän P2
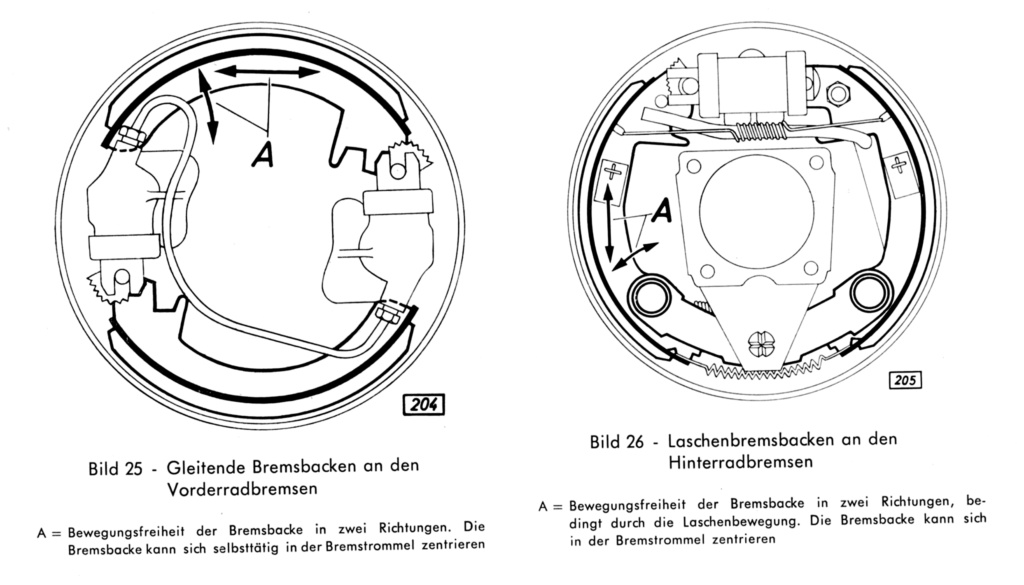


- Train avant frein à tambour : 2 cylindres à 1 piston à simple effet relié par une tubulure.
- Train arrière frein à tambour: 1 cylindre à double pistons.
Photo, image (Bild) : bild 29, escargots de réglage des mâchoires (2) - bild 59 : escargot remplacé par une molette de réglage de l’écartement des mâchoires sur Kapitän P1 et P2 en 2,5 L.
- PS : Les cylindres des freins à tambours (Kapitän 2,6L) sont plus gros en diamètre que sur la Rekord P2
- Non compatible –
-Bild 62- Réglage des mâchoires par l’excentrique sur la Kapitän –P- 2 2,6L






- Pour les tubes hydrauliques il existe 4 modèles d’emporte - pièces (matrices) dont les diamètres sont 2 de 8 mm et 2 de diamètre de 5 mm. Il faut donc 2 matrices pour la forme intérieure en 8 et en 5 mm. 2 matrices en 8 et en 5 mm pour les lèvres externes. Cela dépend de la forme de la vis, raccord, vis de purge, dérivation en Té, etc.
- Comme cadeau de NOËL :
- Pour ne pas abîmer les vis des tuyaux de freins, il est conseillé d’utiliser des clés polygonales ouvertes pour tuyau de frein de 8 à 19mm. Kit de 6 clés plates pour tuyau de frein HASKYY - Assortiment de clés polygonales ouvertes pour tuyau de frein :
- Conception mince. Angle de tête facilitant les interventions aux endroits difficiles d’accès
- Pour raccords hydrauliques, de tuyau de frein, servofrein, etc. Chrome vanadium Qualité industrielle
- Tailles incluses : 8 x 9 / 10 x 11 / 12 x 13 / 14 x 15 / 16x17 / 18x19 - Housse de rangement compact en Tetron
- Garantie HASKYY de 2 ans - 18,99 Euros - Il en existe aussi en pouces inclinés à 15°, vendue en kit ou à l’unité.
- Circuit du frein à main : verrouillage, palonnier, ressort de rappel, câbles, tendeur, levier intérieur actionnant les mâchoires, support de gaines, etc.

- LD -

- Principe de fonctionnement d’un maître cylindre simple :
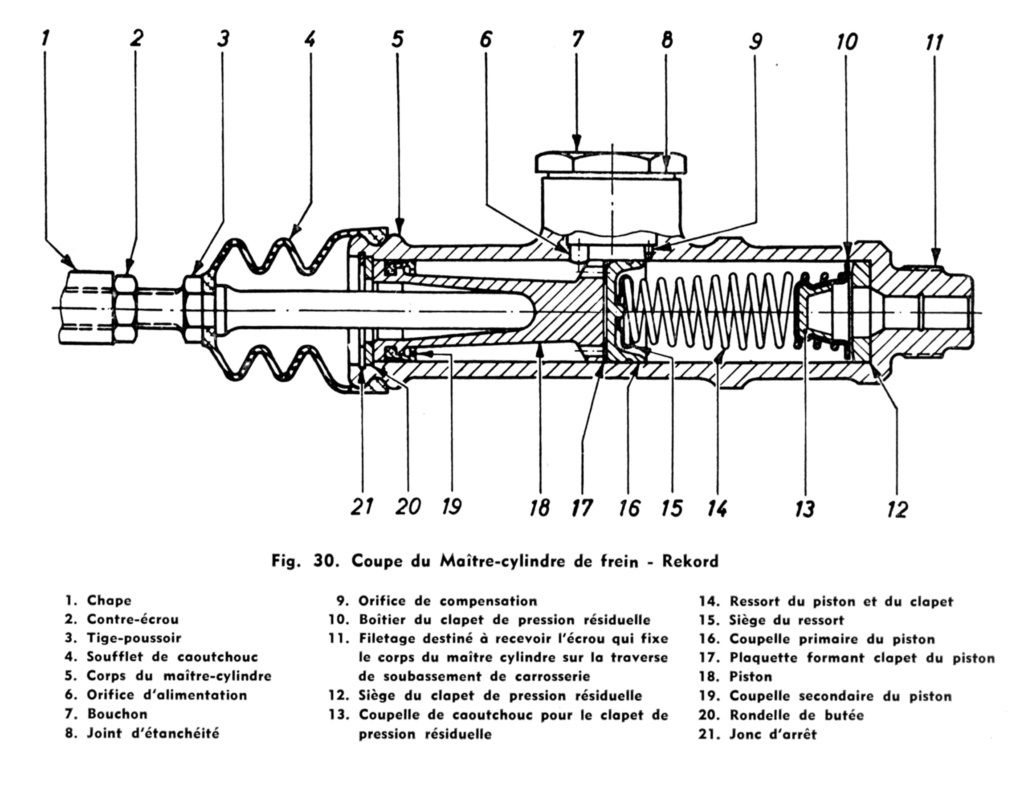





- Le principe de fonctionnement est basé sur le principe de théorème de Pascal : Tout fluide est considéré comme étant incompressible. Toute variation de pression en un point du circuit entraîne la même variation de pression en tout point du circuit. La pression dépend de la force et de la surface sur laquelle est exercée cette force.
- L’INCOMPRESSIBILITÉ DU LIQUIDE
- Si le liquide est compressible, le levier devient spongieux au point d’arriver en butée sans transmettre l’effort aux pistons.
- Lubrification :
- Le liquide utilisé doit participer à la lubrification des pièces mobiles du circuit de freinage (pistons & joints)
- La protection anticorrosion :
C’est le point faible des liquides de freins classiques qui ont tendance à se charger en eau. Les risques sont alors l’oxydation et le grippage des pièces (étriers frein, pistons, etc …). Les formulations intègrent généralement des inhibiteurs de corrosion et d’oxydation.
- Comment le liquide de frein peut-il se contaminer ?
- Le liquide se contamine dés lors que la bouteille est dévissée et ouverte. Le liquide peut donc être contaminé avant même son entrée dans le circuit de freinage. C’est pourquoi, il est nécessaire de conserver le liquide dans un flacon hermétiquement fermé lorsqu’il n’est pas utilisé, l’idéal étant de ne pas réutiliser le flacon ouvert. Privilégiez pour cela l’achat de petits conditionnements.
- L’humidité peut entrer dans le circuit dés lors que le réservoir ou maître cylindre est ouvert.
Les joints et les durites n’étant jamais complètement étanches, l’humidité en infime quantité va être absorbée et c’est pourquoi les fabricants automobiles préconisent la purge du système de freinage tous les deux ans.
- Olympia Rekord, Olympia, Caravan, Fourgonnette de livraison, et Kapitän –
- Le maître cylindre des modèles Olympia et Kapitän sont tous identiques, à la seule exception du raccordement sur le maître cylindre du tuyau d’alimentation en provenance du réservoir de liquide de frein. Sur le modèle Olympia, le tuyau se brancher sur un orifice pratiqué directement dans le corps du maître cylindre. Dans le cas de la Kapitän, ce tuyau aboutit au bouchon fileté. Cette différence n’entraîne pas de modification du procédé à employer pour la révision du maître cylindre, de telle sorte que les instructions valables pour les modèles Olympia le sont aussi pour le modèle Kapitän.
- Sur la Kapitän P il existe une autre forme de maître cylindre. D’autres accessoires peuvent être montés en dérivations : prise sur le bouchon du réservoir transparent, robinet d’arrêt, etc.

- Le fonctionnement : position repos :

- Les trous de dilatation et d’alimentation sont ouverts. La pression est identique dans les deux chambres, le ressort maintien le piston en position repos.
- Le fonctionnement : position freinage :

- L’action du conducteur sur la pédale de frein provoque le déplacement du piston et des coupelles.
- Des que la coupelle primaire obture le trou de dilatation, la chambre de pression devient étanche et la pression peut se créer. Celle-ci dépend de la force du conducteur et de la surface du piston. Le liquide étant incompressible, la pression se retrouve au niveau des récepteurs.
- Le fonctionnement : position de relâchement :

- Le conducteur cesse son action sur la pédale. Le ressort repousse le piston vers sa position de repos. La pression chute dans la chambre de pression.
- La compensation à l’usure :

- Lors du recule du piston, la pression chute dans la chambre de pression (le volume augmente) et augmente dans la chambre d’alimentation (le volume diminue)
- Cette différence de pression entraîne la courbure de la coupelle primaire et le passage du liquide à travers les trous de compression du piston. La quantité de liquide transféré permet de compenser l’usure des (plaquettes) et garnitures de frein.
- A chaque freinage, le niveau de liquide chute dans le réservoir. Un niveau faible peut indiquer une usure importante des freins, il ne faut pas refaire le niveau car lors du remplacement des plaquettes ou garnitures, le fait de repousser les pistons fait remonter le niveau. S’il est trop élevé au départ, il y a risque de fuite (trop plein)
- Inspection interne du maître cylindre.
- Une fois le mécanisme démonté, vous pouvez vérifier que les 2 trous correspondant avec une des chambres ne sont pas obstrués ( 15 et 16, voir sur l’éclaté si-dessous) : La chambre d’alimentation ou la chambre de pression (2 trous d’environ 1mm) avec l’aide d’une lampe torche d’inspection à LED ou en fabriquer une avec une ampoule de tableau de bord (1,5 W) que vous aurez soudé à l’aide de 2 fils.
- Maître cylindre Kapitän P2 avec récipient transparent

.


- Les différents circuits de freinages :
- Depuis 1977 la législation impose l’utilisation de deux circuits indépendants :
- Le circuit en « H »
- Le circuit en « X »
- Les circuits en « H » :

- Les circuits avant et arrière sont séparés.
- Avantage :
- Simplicité du système, la stabilité du véhicule n’est que très peu affectée.
- Les circuits en « X »

- Avantage :
- La perte d’efficacité est de 50%, quelque soit le circuit défaillant.
- Inconvénient :
- En cas de défaillance, la stabilité du véhicule est très affectée
- Il est nécessaire d’utiliser un maître cylindre en tandem avec double réservoir.
- Planches- Frein : Parts catalog - Opel Kapitän P - 2,5 L – 2,6 L - révision décembre 1974-
- Kapitän Panoramique P2 :
- Eclatés pièces détachées, circuit de freinage :


- Tous les éléments marqués d’un astérisque correspondent à des modèles en Kapitän Panoramique P, soit 2,5 L ou en 2,6L d’entrée de gamme.
- Double pistons uniquement sur le train avant de la Kapitän P2
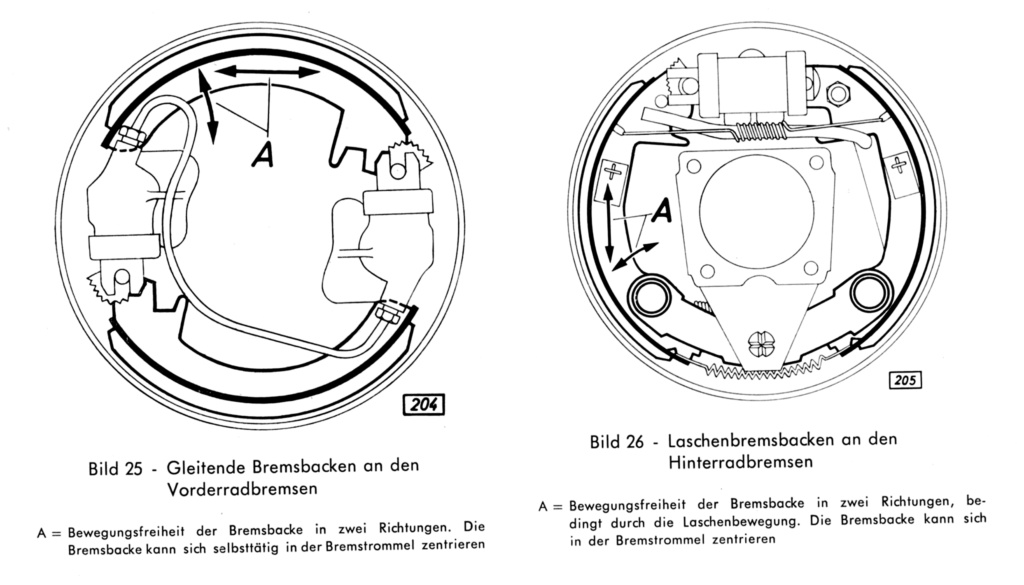


- Train avant frein à tambour : 2 cylindres à 1 piston à simple effet relié par une tubulure.
- Train arrière frein à tambour: 1 cylindre à double pistons.
Photo, image (Bild) : bild 29, escargots de réglage des mâchoires (2) - bild 59 : escargot remplacé par une molette de réglage de l’écartement des mâchoires sur Kapitän P1 et P2 en 2,5 L.
- PS : Les cylindres des freins à tambours (Kapitän 2,6L) sont plus gros en diamètre que sur la Rekord P2
- Non compatible –
-Bild 62- Réglage des mâchoires par l’excentrique sur la Kapitän –P- 2 2,6L






- Pour les tubes hydrauliques il existe 4 modèles d’emporte - pièces (matrices) dont les diamètres sont 2 de 8 mm et 2 de diamètre de 5 mm. Il faut donc 2 matrices pour la forme intérieure en 8 et en 5 mm. 2 matrices en 8 et en 5 mm pour les lèvres externes. Cela dépend de la forme de la vis, raccord, vis de purge, dérivation en Té, etc.
- Comme cadeau de NOËL :
- Pour ne pas abîmer les vis des tuyaux de freins, il est conseillé d’utiliser des clés polygonales ouvertes pour tuyau de frein de 8 à 19mm. Kit de 6 clés plates pour tuyau de frein HASKYY - Assortiment de clés polygonales ouvertes pour tuyau de frein :
- Conception mince. Angle de tête facilitant les interventions aux endroits difficiles d’accès
- Pour raccords hydrauliques, de tuyau de frein, servofrein, etc. Chrome vanadium Qualité industrielle
- Tailles incluses : 8 x 9 / 10 x 11 / 12 x 13 / 14 x 15 / 16x17 / 18x19 - Housse de rangement compact en Tetron
- Garantie HASKYY de 2 ans - 18,99 Euros - Il en existe aussi en pouces inclinés à 15°, vendue en kit ou à l’unité.
- Circuit du frein à main : verrouillage, palonnier, ressort de rappel, câbles, tendeur, levier intérieur actionnant les mâchoires, support de gaines, etc.

- LD -
Daniel- Messages : 544
Date d'inscription : 22/04/2012
Age : 81
Localisation : Paris Ouest
Opeldel aime ce message
Re: restauration moteur ancien opel des années 60
Sur la Kapitän Panoramique P2 - 2,6L :
En revisitant mon stock d’amortisseurs avant et arrière j’ai fait un petit montage rapide ( à blanc) entre la plaque en acier (4 mm d’épaisseur) qui est fixée sur l’avant du moteur. Elle reçoit donc les 2 amortisseurs en caoutchouc sur sa base ( grandes dimensions : 95 x 85 x 40 mm) fixés par 2 écrous. La grosse poutre, qui elle est fixée sur le châssis de la voiture (niveau cylindre N°1) En voulant faire assemblage avec les 2 boulons et les repères (pointes) qui se trouvent sous l’amortisseur en caoutchouc il y avait une différence de 1 cm des trous percés dans la poutre avant.
Toutes les pièces détachées comportent normalement un code de fabrication et là, pas de code ! .
Si vous présentez la plaque en acier sur le bloc moteur tous les trous de perçages sont rigoureusement identiques. Dimensions suivant le modèle : 47 x 22,5 cm x 4 mm
Les 2 oreilles recevant les 2 amortisseurs en caoutchouc, sur la plaque en acier de 4 mm ont le même écartement. C’est juste que l’assemblage entre les 2 caoutchoucs montés sur la plaque en acier qui devient impossible. Pour éviter l’inversion de la poutre avant (180°) il y a un détrompeur un trou rond et une demi-lune ‘inclinaison de la poutre’.
- Encore un problème à qui il faut faire très attention ! . Il y a 2 références de plaques en acier et 2 références pour le support moteur. ( Suivant le N° de série et production ! ) 608015 et 608016. Pour les 2 amortisseurs : Avants et arrières, qui sont différents, se sont les mêmes pour les deux versions : référence pour les 2 avants : 684257- Référence pour les 2 arrières : 684757 –
Poutre avant : 684151- et 684… !
Les écrous de fixation (même produit) : vous pouvez les trouver sous différentes références (codes OPEL très ancien, ancien, moderne 1974) : Référence en N-16640 ; en 2018102, en 608181.
Erreur à ne pas commettre lors du remontage : L’inversion d’un modèle ( en tôle d’acier de 4 mm d’épaisseur) par rapport à l’autre modèle. Vous ne vous en apercevrez que lorsque vous descendrez le moteur sur son berceau.
Vous aurez placé tous les joints moteurs, sur la face avant, le pignon en acier du vilebrequin, le pignon en céloron avec son arbre à cames, le carter en tôle face avant, peut-être le moteur complètement remonté, etc. La galère… moteur à ressortir, etc…
- LD-
En revisitant mon stock d’amortisseurs avant et arrière j’ai fait un petit montage rapide ( à blanc) entre la plaque en acier (4 mm d’épaisseur) qui est fixée sur l’avant du moteur. Elle reçoit donc les 2 amortisseurs en caoutchouc sur sa base ( grandes dimensions : 95 x 85 x 40 mm) fixés par 2 écrous. La grosse poutre, qui elle est fixée sur le châssis de la voiture (niveau cylindre N°1) En voulant faire assemblage avec les 2 boulons et les repères (pointes) qui se trouvent sous l’amortisseur en caoutchouc il y avait une différence de 1 cm des trous percés dans la poutre avant.
Toutes les pièces détachées comportent normalement un code de fabrication et là, pas de code ! .
Si vous présentez la plaque en acier sur le bloc moteur tous les trous de perçages sont rigoureusement identiques. Dimensions suivant le modèle : 47 x 22,5 cm x 4 mm
Les 2 oreilles recevant les 2 amortisseurs en caoutchouc, sur la plaque en acier de 4 mm ont le même écartement. C’est juste que l’assemblage entre les 2 caoutchoucs montés sur la plaque en acier qui devient impossible. Pour éviter l’inversion de la poutre avant (180°) il y a un détrompeur un trou rond et une demi-lune ‘inclinaison de la poutre’.
- Encore un problème à qui il faut faire très attention ! . Il y a 2 références de plaques en acier et 2 références pour le support moteur. ( Suivant le N° de série et production ! ) 608015 et 608016. Pour les 2 amortisseurs : Avants et arrières, qui sont différents, se sont les mêmes pour les deux versions : référence pour les 2 avants : 684257- Référence pour les 2 arrières : 684757 –
Poutre avant : 684151- et 684… !
Les écrous de fixation (même produit) : vous pouvez les trouver sous différentes références (codes OPEL très ancien, ancien, moderne 1974) : Référence en N-16640 ; en 2018102, en 608181.
Erreur à ne pas commettre lors du remontage : L’inversion d’un modèle ( en tôle d’acier de 4 mm d’épaisseur) par rapport à l’autre modèle. Vous ne vous en apercevrez que lorsque vous descendrez le moteur sur son berceau.
Vous aurez placé tous les joints moteurs, sur la face avant, le pignon en acier du vilebrequin, le pignon en céloron avec son arbre à cames, le carter en tôle face avant, peut-être le moteur complètement remonté, etc. La galère… moteur à ressortir, etc…
- LD-
Daniel- Messages : 544
Date d'inscription : 22/04/2012
Age : 81
Localisation : Paris Ouest
Opeldel aime ce message
Re: restauration moteur ancien opel des années 60
Bonjour.
Surprise, surprise …
Il faut éviter de commander une ligne d’échappement complète chez Opel Parts ?
Pourquoi ?
J’ai commandé une ligne complète (neuve) allant du collecteur d’échappement jusqu’au silencieux de sortie plus un kit ! + de 500 Euros (Kapitän P2)
A la réception du colis je trouve bizarre qu’il soit si petit !
Le tube partant du collecteur jusqu’au premier pot de détente mesure environ 2,50 m de long. !
Je déballe donc l’ensemble du paquet, déjà, je m’aperçois que le tube côté collecteur sortait du colis !
Des deux silencieux étaient à l’intérieur ainsi que le coude qui passe au-dessus du pont : Ok
A ma grande stupeur je découvre que le grand tube d’échappement a été sectionné en deux !!! ce qui explique cela…
Sur la facture il y a marquée que le paquet ne doit pas dépasser 1,20m de long pour l’expédition par DHL….
Après un courrier, photo à l’appuie, la société m’a écrit qu’on était le seul à « rouspéter » pour un tube coupé !!! Les allemands comprennent très bien et les font ressouder par un artisan !!!
Maintenant vous savez ce qui vous attend ; soit que vous iriez le chercher directement chez Opel Parts, soit que vous aurez le droit de faire faire une belle soudure avec un MIG.
LD Historien de l’OOCB
Surprise, surprise …
Il faut éviter de commander une ligne d’échappement complète chez Opel Parts ?
Pourquoi ?
J’ai commandé une ligne complète (neuve) allant du collecteur d’échappement jusqu’au silencieux de sortie plus un kit ! + de 500 Euros (Kapitän P2)
A la réception du colis je trouve bizarre qu’il soit si petit !
Le tube partant du collecteur jusqu’au premier pot de détente mesure environ 2,50 m de long. !
Je déballe donc l’ensemble du paquet, déjà, je m’aperçois que le tube côté collecteur sortait du colis !
Des deux silencieux étaient à l’intérieur ainsi que le coude qui passe au-dessus du pont : Ok
A ma grande stupeur je découvre que le grand tube d’échappement a été sectionné en deux !!! ce qui explique cela…
Sur la facture il y a marquée que le paquet ne doit pas dépasser 1,20m de long pour l’expédition par DHL….
Après un courrier, photo à l’appuie, la société m’a écrit qu’on était le seul à « rouspéter » pour un tube coupé !!! Les allemands comprennent très bien et les font ressouder par un artisan !!!
Maintenant vous savez ce qui vous attend ; soit que vous iriez le chercher directement chez Opel Parts, soit que vous aurez le droit de faire faire une belle soudure avec un MIG.
LD Historien de l’OOCB
Daniel- Messages : 544
Date d'inscription : 22/04/2012
Age : 81
Localisation : Paris Ouest
Opeldel aime ce message
Re: restauration moteur ancien opel des années 60
Bonjour
- Outillage utile pour l’assemblage de pont d’échappement
Suite à une livraison désastreuse, que j’ai cité précédemment :
Il arrive que dans le transport que les tubes d’échappement soit mal traité et qu’il devient difficile de les assembler, coups, déformations, mal emballé, saboter, découper, etc.
La société : TECTAKE Expandeur Élargisseur pour Tube de Pot d'Echappement 30 - 83 mm Ø en Acier + 1 Coffret de rangement
Les élargisseurs de tuyau d'échappement sont votre meilleur assistant dans votre atelier.
Ces outils sont très faciles et simples à utiliser.
Ce kit est idéal pour les travaux de réparation ou pour éliminer les défauts d'étanchéité.
*** Points Forts :
Élargissement uniforme des tuyaux d'échappement.
Les bosselures peuvent également être éliminées.
Pour former des tubes et ouvertures de tubes déjà emboîtés avec apport de chaleur.
De nouveaux tuyaux d'échappement peuvent ainsi être ajustés sur de vieilles pièces d'échappement.
Pour obtenir le diamètre de tuyau souhaité, tournez la broche (entraînement hexagonal), cela élargit la dimension de l'outil et donc également le tube.
Peu encombrant une fois rangé dans un coffret en plastique.
*** Caractéristiques Techniques :
Pour un diamètre d'échappement : 30 - 83 mm Ø.
** Élargisseur « petit » :
Capacité : 30 - 44 mm Ø.
Entraînement hexagonal : 17 mm.
** Élargisseur « moyen » :
Capacité : 39 - 54 mm Ø.
Entraînement hexagonal : 17 mm.
** Élargisseur « grand » :
Capacité : 56 - 83 mm Ø.
Entraînement hexagonal : 19 mm.
** Matériaux :
Outils en Acier / Coffret en Plastique.
Pour une somme modique il vous rendra de bons services. Jusque là j’en suis satisfait.
Prix : 38,90 Euros. Livraison gratuite.-
LD Historien de l’OOCB
Bonjour
- Outillage utile pour l’assemblage de pont d’échappement
Suite à une livraison désastreuse, que j’ai cité précédemment :
Il arrive que dans le transport que les tubes d’échappement soit mal traité et qu’il devient difficile de les assembler, coups, déformations, mal emballé, saboter, découper, etc.
La société : TECTAKE Expandeur Élargisseur pour Tube de Pot d'Echappement 30 - 83 mm Ø en Acier + 1 Coffret de rangement
Les élargisseurs de tuyau d'échappement sont votre meilleur assistant dans votre atelier.
Ces outils sont très faciles et simples à utiliser.
Ce kit est idéal pour les travaux de réparation ou pour éliminer les défauts d'étanchéité.
*** Points Forts :
Élargissement uniforme des tuyaux d'échappement.
Les bosselures peuvent également être éliminées.
Pour former des tubes et ouvertures de tubes déjà emboîtés avec apport de chaleur.
De nouveaux tuyaux d'échappement peuvent ainsi être ajustés sur de vieilles pièces d'échappement.
Pour obtenir le diamètre de tuyau souhaité, tournez la broche (entraînement hexagonal), cela élargit la dimension de l'outil et donc également le tube.
Peu encombrant une fois rangé dans un coffret en plastique.
*** Caractéristiques Techniques :
Pour un diamètre d'échappement : 30 - 83 mm Ø.
** Élargisseur « petit » :
Capacité : 30 - 44 mm Ø.
Entraînement hexagonal : 17 mm.
** Élargisseur « moyen » :
Capacité : 39 - 54 mm Ø.
Entraînement hexagonal : 17 mm.
** Élargisseur « grand » :
Capacité : 56 - 83 mm Ø.
Entraînement hexagonal : 19 mm.
** Matériaux :
Outils en Acier / Coffret en Plastique.
Pour une somme modique il vous rendra de bons services. Jusque là j’en suis satisfait.
Prix : 38,90 Euros. Livraison gratuite.-
LD Historien de l’OOCB
- Outillage utile pour l’assemblage de pont d’échappement
Suite à une livraison désastreuse, que j’ai cité précédemment :
Il arrive que dans le transport que les tubes d’échappement soit mal traité et qu’il devient difficile de les assembler, coups, déformations, mal emballé, saboter, découper, etc.
La société : TECTAKE Expandeur Élargisseur pour Tube de Pot d'Echappement 30 - 83 mm Ø en Acier + 1 Coffret de rangement
Les élargisseurs de tuyau d'échappement sont votre meilleur assistant dans votre atelier.
Ces outils sont très faciles et simples à utiliser.
Ce kit est idéal pour les travaux de réparation ou pour éliminer les défauts d'étanchéité.
*** Points Forts :
Élargissement uniforme des tuyaux d'échappement.
Les bosselures peuvent également être éliminées.
Pour former des tubes et ouvertures de tubes déjà emboîtés avec apport de chaleur.
De nouveaux tuyaux d'échappement peuvent ainsi être ajustés sur de vieilles pièces d'échappement.
Pour obtenir le diamètre de tuyau souhaité, tournez la broche (entraînement hexagonal), cela élargit la dimension de l'outil et donc également le tube.
Peu encombrant une fois rangé dans un coffret en plastique.
*** Caractéristiques Techniques :
Pour un diamètre d'échappement : 30 - 83 mm Ø.
** Élargisseur « petit » :
Capacité : 30 - 44 mm Ø.
Entraînement hexagonal : 17 mm.
** Élargisseur « moyen » :
Capacité : 39 - 54 mm Ø.
Entraînement hexagonal : 17 mm.
** Élargisseur « grand » :
Capacité : 56 - 83 mm Ø.
Entraînement hexagonal : 19 mm.
** Matériaux :
Outils en Acier / Coffret en Plastique.
Pour une somme modique il vous rendra de bons services. Jusque là j’en suis satisfait.
Prix : 38,90 Euros. Livraison gratuite.-
LD Historien de l’OOCB
Bonjour
- Outillage utile pour l’assemblage de pont d’échappement
Suite à une livraison désastreuse, que j’ai cité précédemment :
Il arrive que dans le transport que les tubes d’échappement soit mal traité et qu’il devient difficile de les assembler, coups, déformations, mal emballé, saboter, découper, etc.
La société : TECTAKE Expandeur Élargisseur pour Tube de Pot d'Echappement 30 - 83 mm Ø en Acier + 1 Coffret de rangement
Les élargisseurs de tuyau d'échappement sont votre meilleur assistant dans votre atelier.
Ces outils sont très faciles et simples à utiliser.
Ce kit est idéal pour les travaux de réparation ou pour éliminer les défauts d'étanchéité.
*** Points Forts :
Élargissement uniforme des tuyaux d'échappement.
Les bosselures peuvent également être éliminées.
Pour former des tubes et ouvertures de tubes déjà emboîtés avec apport de chaleur.
De nouveaux tuyaux d'échappement peuvent ainsi être ajustés sur de vieilles pièces d'échappement.
Pour obtenir le diamètre de tuyau souhaité, tournez la broche (entraînement hexagonal), cela élargit la dimension de l'outil et donc également le tube.
Peu encombrant une fois rangé dans un coffret en plastique.
*** Caractéristiques Techniques :
Pour un diamètre d'échappement : 30 - 83 mm Ø.
** Élargisseur « petit » :
Capacité : 30 - 44 mm Ø.
Entraînement hexagonal : 17 mm.
** Élargisseur « moyen » :
Capacité : 39 - 54 mm Ø.
Entraînement hexagonal : 17 mm.
** Élargisseur « grand » :
Capacité : 56 - 83 mm Ø.
Entraînement hexagonal : 19 mm.
** Matériaux :
Outils en Acier / Coffret en Plastique.
Pour une somme modique il vous rendra de bons services. Jusque là j’en suis satisfait.
Prix : 38,90 Euros. Livraison gratuite.-
LD Historien de l’OOCB
Daniel- Messages : 544
Date d'inscription : 22/04/2012
Age : 81
Localisation : Paris Ouest
Opeldel aime ce message
Re: restauration moteur ancien opel des années 60
Bonjour cher Opelistes
En commandant une ligne d’échappement (neuve), complète, pour ma Kapitän Panoramique P2 de 1960 chez un grand fournisseur j’ai eu une mauvaise surprise à la livraison !
Le tube partant du collecteur jusqu’au premier pot d’échappement, mesurant 2,42 m de long était coupé en deux (en sifflet) !!!
Les deux morceaux étaient maintenus par un restant de métal. Les deux morceaux, pliés pour pouvoir rentrer dans l’emballage ( qui sortait largement du cartonnage) Ayant souffert du transport le tube, au niveau de la coupe c’est donc en plus, déformé.
Il fallut prendre un outil spécial pour refaire la rotondité du tube, puis de trouver un spécialiste qui veille le souder…
Garagiste refuse de souder le tube neuf, chaudronnier aussi, etc. J’ai donc fini par trouver un professionnel travaillant dans du matériel de haute technologie qui a put me le souder. Pas avec un MIG mais, nettement mieux avec un TIG.
Avec le confidemment j’ai perdu 5 mois. Le travail de soudage était superbe. Il est très difficile de trouver un spécialiste pour faire ce genre de travail.
Maintenant il y a le risque de rouille interne à l’endroit de la soudure.
Ayant photographié la coupe du tube (sabotage du tube, mal coupé, plié, déformé) et envoyé à l’expéditeur : Classic-Parts ; il m’a été dit que le transport DHL ne prenait que des colis ne dépassant pas 1,20 m de long !.
Donc si vous devez commander une ligne d’échappement pour votre Opel ne soyez pas surpris de voir à l’arrivée votre tube coupé en deux.
Paraît-il que je suis le seul à ‘’râler’’ pour un tube coupé en deux, un coup de soudure avec un MIG… les Allemands, les Belges, Hollandais, etc, trouvent cela normal !!!
Sur la facture, il est précisé les dimensions max pour l’expédition par DHL, mais cela n’est pas signalé au comment de la commande !
Mais la surprise ! se trouve donc à l’arrivée …
Bien se renseigner avant de passer la commande, si votre tube d’échappement : s’il sera livré « Entier ou Coupé » !!!
Autre possibilité, que vous alliez le chercher chez Classic-Parts avant qu’il ne soit tronçonné….
Vu le prix de l’ensemble, assez onéreux, il pourrait proposer un vrai « transporteur », quitte à mettre un supplément !!!
LD
En commandant une ligne d’échappement (neuve), complète, pour ma Kapitän Panoramique P2 de 1960 chez un grand fournisseur j’ai eu une mauvaise surprise à la livraison !
Le tube partant du collecteur jusqu’au premier pot d’échappement, mesurant 2,42 m de long était coupé en deux (en sifflet) !!!
Les deux morceaux étaient maintenus par un restant de métal. Les deux morceaux, pliés pour pouvoir rentrer dans l’emballage ( qui sortait largement du cartonnage) Ayant souffert du transport le tube, au niveau de la coupe c’est donc en plus, déformé.
Il fallut prendre un outil spécial pour refaire la rotondité du tube, puis de trouver un spécialiste qui veille le souder…
Garagiste refuse de souder le tube neuf, chaudronnier aussi, etc. J’ai donc fini par trouver un professionnel travaillant dans du matériel de haute technologie qui a put me le souder. Pas avec un MIG mais, nettement mieux avec un TIG.
Avec le confidemment j’ai perdu 5 mois. Le travail de soudage était superbe. Il est très difficile de trouver un spécialiste pour faire ce genre de travail.
Maintenant il y a le risque de rouille interne à l’endroit de la soudure.
Ayant photographié la coupe du tube (sabotage du tube, mal coupé, plié, déformé) et envoyé à l’expéditeur : Classic-Parts ; il m’a été dit que le transport DHL ne prenait que des colis ne dépassant pas 1,20 m de long !.
Donc si vous devez commander une ligne d’échappement pour votre Opel ne soyez pas surpris de voir à l’arrivée votre tube coupé en deux.
Paraît-il que je suis le seul à ‘’râler’’ pour un tube coupé en deux, un coup de soudure avec un MIG… les Allemands, les Belges, Hollandais, etc, trouvent cela normal !!!
Sur la facture, il est précisé les dimensions max pour l’expédition par DHL, mais cela n’est pas signalé au comment de la commande !
Mais la surprise ! se trouve donc à l’arrivée …
Bien se renseigner avant de passer la commande, si votre tube d’échappement : s’il sera livré « Entier ou Coupé » !!!
Autre possibilité, que vous alliez le chercher chez Classic-Parts avant qu’il ne soit tronçonné….
Vu le prix de l’ensemble, assez onéreux, il pourrait proposer un vrai « transporteur », quitte à mettre un supplément !!!
LD
Daniel- Messages : 544
Date d'inscription : 22/04/2012
Age : 81
Localisation : Paris Ouest
Opeldel aime ce message
Re: restauration moteur ancien opel des années 60
Sale blague, évidemment...

lucdm- Admin
- Messages : 3261
Date d'inscription : 20/04/2012
Age : 68
Localisation : Natoye / Président OOCB
Re: restauration moteur ancien opel des années 60
- Quelques produitsutiles pour la restauration des mécaniques anciennes OPEL
PRODUITS FREIN DE FILET, ADHÉSIFS, PRODUITS D'ÉTANCHÉITÉ ET DE LUBRIFICATION FONCTION DÉSIGNATION DESCRIPTION FREIN FILETS
Loctite 222
Couleur: violet
fluorescent opaque
Produit anaérobie adapté au freinage faible de vis et d'écrous de fixation, de réglage et de
précision.
Il doit être appliqué après avoir enlevé toute trace de lubrifiant à l'aide de l'activateur spé-
cifique.
Loctite 242
Couleur : bleu,
fluorescent
Produit anaérobie adapté à prévenir le desserrage de vis et d'écrous de tous types et à remplacer les fixations mécaniques.
Résistance modérée.
Il doit être appliqué après avoir enlevé toute trace de lubrifiant à l'aide de l'activateur spé-
cifique.
Loctite 243
Couleur : bleu,
fluorescent opaque
Produit alternatif au freinfilet faible 242 ; du fait de sa compatibilité avec l'huile, il n'exige pas
l'activation de surfaces légèrement lubrifiées.
Loctite 270
Couleur : vert,
fluorescent
Produit anaérobie pour le freinage fort de pièces filetées, boulons et goujons qui ne doivent
pas normalement être démontés. Il est possible de démonter en chauffant les pièces environ 80°C.
Il doit être appliqué après avoir enlevé toute trace de lubrifiant à l'aide de l'activateur spé-
cifique.
DÉGRAISSANTS ED
ACTIVATEURS
Loctite 703
Produit pour le dégraissage et le nettoyage des pièces avant l'application de produits
anaérobies Loctite; après séchage instantané, il accélère la polymérisation uniforme des
frein filets
Loctite 747
Produit spécifique pour le traitement de surfaces peu actives vis-à-vis de produits anaérobies
à polymérisation lente (série 5 et 6).
Il s'utilise également pour accélérer la polymérisation par basses températures ou dans le
cas d'assemblages présentant des jeux trop importants.
PRODUITS D'ÉTANCHÉITÉ
(pour plans de joint et raccords)
Loctite 510
Couleur : rouge
Produit anaérobie ultra-rapide utilisé pour l'étanchéité des plans métalliques. Il remplace le
joint conventionnel, car il peut "combler" des vides jusqu'à 0,4 mm.
Parfaitement stabilisé, il n'est pas nécessaire de refaire les serrages au couple prescrit.
Loctite 542
Couleur: marron
Produit anaérobie utilisé comme joint liquide pour l'étanchéité des raccords hydrauliques et
pneumatiques à filetage fin jusqu'à 19 mm (3/4”); Résistance moyenne à polymérisation rapide.
Démontage facile avec outillage classique.
Loctite 554
Couleur: rouge
Produit anaérobie pour l'étanchéité et le blocage. Il convient pour l'étanchéité des circuits de
refroidissement et de fluides industriels.
Produit à polymérisation lente. Il s'applique aussi sur des alliages non ferreux
Loctite 572
Couleur: blanc
Produit anaérobie pour l'étanchéité et le blocage. Il s'utilise sur les tuyauteries et les raccords
filetés jusqu'à un diamètre de 2”.
Produit à polymérisation très lente. Il s'applique sur la plupart des surfaces métalliques
usinées ou non.
Loctite 573
Couleur: vert
Produit anaérobie thixotropique utilisé pour l'étanchéité des plans métalliques.
Il assure un contact parfait entre les surfaces présentant un jeu maximum de 0,10 mm, en
comblant aussi les vides minuscules dûs à des imperfections de surface.
Produit à polymérisation très lente. Il s'applique sur la plupart des surfaces métallique. Il né-
cessite l'emploi d'un activateur.
Loctite 576
Couleur: brun
Produit anaérobie utilisé comme joint liquide. Il s'utilise sur des raccords filetés de grandes dimensions (jusqu'à 2”)
Produit à polymérisation très lente. Il convient aussi pour les alliages non ferreux et les dé-
montages fréquents.
FONCTION DÉSIGNATION DESCRIPTION ADHÉSIFS INSTANTANÉS
Loctite 401
Couleur : incolore
Colle cyanoacrylate instantanée pour le collage de surfaces acides et poreuses d'un grand
nombre de matériaux, tels que céramique, bois, caoutchouc et plastique (excepté polyolé-
fine).
Elle polymérise au bout de quelques secondes seulement par l'action de l'humidité de l'air
présente sur les surfaces à coller, quelles que soient les conditions ambiantes.
Loctite 495
Couleur : incolore
Colle cyanoacrylate pour assembler instantanément aussi bien des matériaux de mêmes
natures (caoutchouc-caoutchouc, plastique-plastique) que des matériaux de différentes
natures entre eux (métal-plastique, plastique-caoutchouc).
PRODUITS D'ÉTANCHÉITÉ
SILICONES
Silastic 738
(Dow Corning)
Couleur : blanc
laiteux
Élastomère siliconé mono composant. Non stabilisé. Prêt à l'emploi.
Il polymérise en un solide de consistance caoutchouteuse lorsqu'il réagit par l'action de
l'humidité de l'air. Il remplace les joints conventionnels sur des liaisons élastiques en comblant
des jeux supérieurs au millimètre.
Dirko Transparent
Couleur : transparent
Élastomère siliconé mono composant. Stabilisé. Prêt à l'emploi.
Il polymérise rapidement en formant un solide caoutchouteux lorsqu'il réagit par action de
l'humidité de l'air. Résistant aussi à des températures élevées.
PRODUITS D'ÉTANCHÉITÉ
POLYURÉTHANES
Betaseal HV3
(Gurit Essex)
Couleur : noir
Adhésif et scellant à base de prépolymère polyuréthanique hautement visqueux. Recommandé
pour les collages élastiques permanents à haute résistance.
Produit à polymérisation lente. Il convient pour le collage des vitres sur les structures respectives,
des treillis métalliques de protection, des plaques, etc. après dégraissage avec
un primaire.
PRODUITS DE BLOCAGE
Loctite 601
Couleur : vert,
fluorescent
Produit anaérobie à polymérisation rapide et à haute résistance mécanique.
Il convient pour rendre étanche et immobiliser les assemblages cylindriques en ajustement
libre et présentant des jeux jusqu'à 0,10 mm, pour le montage d'arbres sur rotors, engrenages,
roulements, poulies, bagues, coussinets, etc.
Loctite 638
Couleur : vert,
fluorescent
Adhésif structurel à polymérisation rapide et à haute résistance mécanique. Convient pour
le montage d'assemblages cylindriques en ajustement libre d'alliages non ferreux.
Loctite 648
Couleur: vert,
fluorescent
Adhésif structurel anaérobie à polymérisation rapide et à haute résistance mécanique.
Convient pour l'immobilisation d'assemblages cylindriques en ajustement libre, l'immobilisation permanente de pièces filetées, l'étanchéité de circuits de réfrigération, le montage de roulements, etc.
Produit alternatif à la Loctite 601. S'utilise par températures de fonctionnement plus élevées.
Loctite 986/AVX
Couleur : rouge,fluorescent.
Produit anaérobie scellant et immobilisant pour les assemblages cylindriques entre pièces
métalliques.
Produit à polymérisation lente. Présente, outre une bonne résistance mécanique et une
bonne tenue à la température, une excellente résistance à la pression chimique.
S'applique après activation des parties.
LUBRIFIANTS
Graisse
(NLGI 2 EP
ASTM D217: 265/295)
Graisse au lithium utilisée pour lubrifier les joints d'étanchéité, prévenir l'oxydation et faciliter
les opérations de montage.
Molikote
(Dow Corning)
Composé lubrifiant anti-usure, contenant du bisulfure de molybdène, utilisé pur ou dilué en
pourcentage avec de l'huile moteur lors du montage des bagues de paliers de moteurs endothermiques.
Vaseline Composé au PH neutre utilisé pour protéger les bornes et les cosses des batteries contre l'oxydation et la corrosion.
Huile moteur
10W - 30
Utilisé pour la dilution du lubrifiant anti-usure Molikote lors des étapes de montage des moteurs endothermiques.
LD
PRODUITS FREIN DE FILET, ADHÉSIFS, PRODUITS D'ÉTANCHÉITÉ ET DE LUBRIFICATION FONCTION DÉSIGNATION DESCRIPTION FREIN FILETS
Loctite 222
Couleur: violet
fluorescent opaque
Produit anaérobie adapté au freinage faible de vis et d'écrous de fixation, de réglage et de
précision.
Il doit être appliqué après avoir enlevé toute trace de lubrifiant à l'aide de l'activateur spé-
cifique.
Loctite 242
Couleur : bleu,
fluorescent
Produit anaérobie adapté à prévenir le desserrage de vis et d'écrous de tous types et à remplacer les fixations mécaniques.
Résistance modérée.
Il doit être appliqué après avoir enlevé toute trace de lubrifiant à l'aide de l'activateur spé-
cifique.
Loctite 243
Couleur : bleu,
fluorescent opaque
Produit alternatif au freinfilet faible 242 ; du fait de sa compatibilité avec l'huile, il n'exige pas
l'activation de surfaces légèrement lubrifiées.
Loctite 270
Couleur : vert,
fluorescent
Produit anaérobie pour le freinage fort de pièces filetées, boulons et goujons qui ne doivent
pas normalement être démontés. Il est possible de démonter en chauffant les pièces environ 80°C.
Il doit être appliqué après avoir enlevé toute trace de lubrifiant à l'aide de l'activateur spé-
cifique.
DÉGRAISSANTS ED
ACTIVATEURS
Loctite 703
Produit pour le dégraissage et le nettoyage des pièces avant l'application de produits
anaérobies Loctite; après séchage instantané, il accélère la polymérisation uniforme des
frein filets
Loctite 747
Produit spécifique pour le traitement de surfaces peu actives vis-à-vis de produits anaérobies
à polymérisation lente (série 5 et 6).
Il s'utilise également pour accélérer la polymérisation par basses températures ou dans le
cas d'assemblages présentant des jeux trop importants.
PRODUITS D'ÉTANCHÉITÉ
(pour plans de joint et raccords)
Loctite 510
Couleur : rouge
Produit anaérobie ultra-rapide utilisé pour l'étanchéité des plans métalliques. Il remplace le
joint conventionnel, car il peut "combler" des vides jusqu'à 0,4 mm.
Parfaitement stabilisé, il n'est pas nécessaire de refaire les serrages au couple prescrit.
Loctite 542
Couleur: marron
Produit anaérobie utilisé comme joint liquide pour l'étanchéité des raccords hydrauliques et
pneumatiques à filetage fin jusqu'à 19 mm (3/4”); Résistance moyenne à polymérisation rapide.
Démontage facile avec outillage classique.
Loctite 554
Couleur: rouge
Produit anaérobie pour l'étanchéité et le blocage. Il convient pour l'étanchéité des circuits de
refroidissement et de fluides industriels.
Produit à polymérisation lente. Il s'applique aussi sur des alliages non ferreux
Loctite 572
Couleur: blanc
Produit anaérobie pour l'étanchéité et le blocage. Il s'utilise sur les tuyauteries et les raccords
filetés jusqu'à un diamètre de 2”.
Produit à polymérisation très lente. Il s'applique sur la plupart des surfaces métalliques
usinées ou non.
Loctite 573
Couleur: vert
Produit anaérobie thixotropique utilisé pour l'étanchéité des plans métalliques.
Il assure un contact parfait entre les surfaces présentant un jeu maximum de 0,10 mm, en
comblant aussi les vides minuscules dûs à des imperfections de surface.
Produit à polymérisation très lente. Il s'applique sur la plupart des surfaces métallique. Il né-
cessite l'emploi d'un activateur.
Loctite 576
Couleur: brun
Produit anaérobie utilisé comme joint liquide. Il s'utilise sur des raccords filetés de grandes dimensions (jusqu'à 2”)
Produit à polymérisation très lente. Il convient aussi pour les alliages non ferreux et les dé-
montages fréquents.
FONCTION DÉSIGNATION DESCRIPTION ADHÉSIFS INSTANTANÉS
Loctite 401
Couleur : incolore
Colle cyanoacrylate instantanée pour le collage de surfaces acides et poreuses d'un grand
nombre de matériaux, tels que céramique, bois, caoutchouc et plastique (excepté polyolé-
fine).
Elle polymérise au bout de quelques secondes seulement par l'action de l'humidité de l'air
présente sur les surfaces à coller, quelles que soient les conditions ambiantes.
Loctite 495
Couleur : incolore
Colle cyanoacrylate pour assembler instantanément aussi bien des matériaux de mêmes
natures (caoutchouc-caoutchouc, plastique-plastique) que des matériaux de différentes
natures entre eux (métal-plastique, plastique-caoutchouc).
PRODUITS D'ÉTANCHÉITÉ
SILICONES
Silastic 738
(Dow Corning)
Couleur : blanc
laiteux
Élastomère siliconé mono composant. Non stabilisé. Prêt à l'emploi.
Il polymérise en un solide de consistance caoutchouteuse lorsqu'il réagit par l'action de
l'humidité de l'air. Il remplace les joints conventionnels sur des liaisons élastiques en comblant
des jeux supérieurs au millimètre.
Dirko Transparent
Couleur : transparent
Élastomère siliconé mono composant. Stabilisé. Prêt à l'emploi.
Il polymérise rapidement en formant un solide caoutchouteux lorsqu'il réagit par action de
l'humidité de l'air. Résistant aussi à des températures élevées.
PRODUITS D'ÉTANCHÉITÉ
POLYURÉTHANES
Betaseal HV3
(Gurit Essex)
Couleur : noir
Adhésif et scellant à base de prépolymère polyuréthanique hautement visqueux. Recommandé
pour les collages élastiques permanents à haute résistance.
Produit à polymérisation lente. Il convient pour le collage des vitres sur les structures respectives,
des treillis métalliques de protection, des plaques, etc. après dégraissage avec
un primaire.
PRODUITS DE BLOCAGE
Loctite 601
Couleur : vert,
fluorescent
Produit anaérobie à polymérisation rapide et à haute résistance mécanique.
Il convient pour rendre étanche et immobiliser les assemblages cylindriques en ajustement
libre et présentant des jeux jusqu'à 0,10 mm, pour le montage d'arbres sur rotors, engrenages,
roulements, poulies, bagues, coussinets, etc.
Loctite 638
Couleur : vert,
fluorescent
Adhésif structurel à polymérisation rapide et à haute résistance mécanique. Convient pour
le montage d'assemblages cylindriques en ajustement libre d'alliages non ferreux.
Loctite 648
Couleur: vert,
fluorescent
Adhésif structurel anaérobie à polymérisation rapide et à haute résistance mécanique.
Convient pour l'immobilisation d'assemblages cylindriques en ajustement libre, l'immobilisation permanente de pièces filetées, l'étanchéité de circuits de réfrigération, le montage de roulements, etc.
Produit alternatif à la Loctite 601. S'utilise par températures de fonctionnement plus élevées.
Loctite 986/AVX
Couleur : rouge,fluorescent.
Produit anaérobie scellant et immobilisant pour les assemblages cylindriques entre pièces
métalliques.
Produit à polymérisation lente. Présente, outre une bonne résistance mécanique et une
bonne tenue à la température, une excellente résistance à la pression chimique.
S'applique après activation des parties.
LUBRIFIANTS
Graisse
(NLGI 2 EP
ASTM D217: 265/295)
Graisse au lithium utilisée pour lubrifier les joints d'étanchéité, prévenir l'oxydation et faciliter
les opérations de montage.
Molikote
(Dow Corning)
Composé lubrifiant anti-usure, contenant du bisulfure de molybdène, utilisé pur ou dilué en
pourcentage avec de l'huile moteur lors du montage des bagues de paliers de moteurs endothermiques.
Vaseline Composé au PH neutre utilisé pour protéger les bornes et les cosses des batteries contre l'oxydation et la corrosion.
Huile moteur
10W - 30
Utilisé pour la dilution du lubrifiant anti-usure Molikote lors des étapes de montage des moteurs endothermiques.
LD
Daniel- Messages : 544
Date d'inscription : 22/04/2012
Age : 81
Localisation : Paris Ouest
Opeldel aime ce message
Re: restauration moteur ancien opel des années 60
Les couples de serrage spécifiques d'éléments importants et les serrages qui demandent une méthode d'exécution particulière, sont indiqués dans chacun des paragraphes concernant l'assemblage.
Les couples de serrage indiqués se réfèrent aux montages de vis et écrous sans lubrification et éventuellement avec le filetage enduit d'un produit anaérobie de frein de filet.
Les valeurs indiquées se réfèrent à des serrages sur des matériaux en acier ou en fonte; pour les matières tendres telles que l'aluminium, le cuivre ou les matières plastiques, les tôles ou panneaux, les couples de serrage doivent être diminués de 50%.
DIMENSION VIS
CLASSE VIS
8.8 Nm lb.ft. 10,9 Nm lb.ft.
PAS GROS
8,8 10,9
Nm lb.ft. Nm lb.ft.
M6x1 8,0 – 8,8 5.9 – 6.5 11,8 – 13,0 8.7 – 9.6
M8x1,25 19,4 – 21,4 14.3 – 15.8 28,5 – 31,5 21.0 – 23.2
M10x1,5 38,4 – 42,4 28.3 – 31.2 56,4 – 62,4 41.6 – 46.0
M12x1,75 66,5 – 73,5 49.0 – 54.2 96,9 – 107 71.4 – 78.9
M14x2 106 – 117 78.1 – 86.2 156 – 172 115,0 – 126,8
M16x2 164 – 182 120.9 – 134.1 241 – 267 117.6 – 196.8
M18x2,5 228 – 252 168.0 – 185.7 334 – 370 246.2 – 272.7
M20x2,5 321 – 355 236.6 – 261.6 472 – 522 347.9 – 384.7
M22x2,5 441 – 487 325.0 – 358.9 647 – 715 476.8 – 527.0
M24x3 553 – 611 407.6 – 450.3 812 – 898 598.4 – 661.8
M27x3 816 – 902 601.4 - 664.8 1198 - 1324 882.9 - 975.8 -
PAS FIN
8,8 10,9
Nm lb.ft. Nm lb.ft.
M8x1 20,8 – 23,0 15.3 – 17.0 30,6 – 33,8 22.6 – 24.9 M10x1,25 40,6 – 44,8 29.9 – 33.0 59,7 – 65,9 44.0 – 48.6
M12x1,25 72,2 – 79,8 53.2 – 58.8 106 – 118 78.1 – 87.0
M12x1,5 69,4 – 76,7 51.1 – 56.5 102 – 112 75.2 – 82.5
M14x1,5 114 – 126 84.0 – 92.9 168 – 186 123.8 – 137.1
M16x1,5 175 – 194 129 – 143 257 – 285 189.4 – 210.0
M18x1,5 256 – 282 188.7 – 207.8 375 – 415 276.4 – 305.9
M20x1,5 355 – 393 261.6 – 289.6 523 – 578 385.5 – 426.0
M2x1,5 482 – 532 355.2 – 392.1 708 – 782 521.8 – 576.3
M24x2 602 – 666 443.7 – 490.8 884 – 978 651.5 – 720.8
Ps : Sur certains manuels techniques d’atelier Opel les valeurs de serrages sont en Ib. Ft
LD
Les couples de serrage indiqués se réfèrent aux montages de vis et écrous sans lubrification et éventuellement avec le filetage enduit d'un produit anaérobie de frein de filet.
Les valeurs indiquées se réfèrent à des serrages sur des matériaux en acier ou en fonte; pour les matières tendres telles que l'aluminium, le cuivre ou les matières plastiques, les tôles ou panneaux, les couples de serrage doivent être diminués de 50%.
DIMENSION VIS
CLASSE VIS
8.8 Nm lb.ft. 10,9 Nm lb.ft.
PAS GROS
8,8 10,9
Nm lb.ft. Nm lb.ft.
M6x1 8,0 – 8,8 5.9 – 6.5 11,8 – 13,0 8.7 – 9.6
M8x1,25 19,4 – 21,4 14.3 – 15.8 28,5 – 31,5 21.0 – 23.2
M10x1,5 38,4 – 42,4 28.3 – 31.2 56,4 – 62,4 41.6 – 46.0
M12x1,75 66,5 – 73,5 49.0 – 54.2 96,9 – 107 71.4 – 78.9
M14x2 106 – 117 78.1 – 86.2 156 – 172 115,0 – 126,8
M16x2 164 – 182 120.9 – 134.1 241 – 267 117.6 – 196.8
M18x2,5 228 – 252 168.0 – 185.7 334 – 370 246.2 – 272.7
M20x2,5 321 – 355 236.6 – 261.6 472 – 522 347.9 – 384.7
M22x2,5 441 – 487 325.0 – 358.9 647 – 715 476.8 – 527.0
M24x3 553 – 611 407.6 – 450.3 812 – 898 598.4 – 661.8
M27x3 816 – 902 601.4 - 664.8 1198 - 1324 882.9 - 975.8 -
PAS FIN
8,8 10,9
Nm lb.ft. Nm lb.ft.
M8x1 20,8 – 23,0 15.3 – 17.0 30,6 – 33,8 22.6 – 24.9 M10x1,25 40,6 – 44,8 29.9 – 33.0 59,7 – 65,9 44.0 – 48.6
M12x1,25 72,2 – 79,8 53.2 – 58.8 106 – 118 78.1 – 87.0
M12x1,5 69,4 – 76,7 51.1 – 56.5 102 – 112 75.2 – 82.5
M14x1,5 114 – 126 84.0 – 92.9 168 – 186 123.8 – 137.1
M16x1,5 175 – 194 129 – 143 257 – 285 189.4 – 210.0
M18x1,5 256 – 282 188.7 – 207.8 375 – 415 276.4 – 305.9
M20x1,5 355 – 393 261.6 – 289.6 523 – 578 385.5 – 426.0
M2x1,5 482 – 532 355.2 – 392.1 708 – 782 521.8 – 576.3
M24x2 602 – 666 443.7 – 490.8 884 – 978 651.5 – 720.8
Ps : Sur certains manuels techniques d’atelier Opel les valeurs de serrages sont en Ib. Ft
LD
Daniel- Messages : 544
Date d'inscription : 22/04/2012
Age : 81
Localisation : Paris Ouest
Opeldel aime ce message
Re: restauration moteur ancien opel des années 60
Suite :
- Quelques unités de conversions :
- Si vous ne trouvez plus de roulements en Europe, ou à des prix démentiels, vous les retrouverez à des prix ‘’ normaux’’ aux USA ; GB ; Japan ; Australie (Holden), etc.
CONVERSION UNITÉS ANGLO-SAXONNES
EN UNITÉS MÉTRIQUES
inch x 25,40 = mm
foot x 0,305 = m
yard x 0,914 = m
Eng.miles x 1,609 = km
Sq.in. x 6,452 = cm²
Sq.ft. x 0,093 = m²
Sq.yard x 0,835 m²
u.in. x 16,39 = cm³
Cu.ft. x 28,36 = m³
Cu.yard x 0,763 m³
Imp.gall. x 4,547 = litres
US gall. x 3,785 litres
pint x 0,568 litres
quart x 1,137 litres
US.gpm x 3,785 = l/min
oz. x 0,028 = kg
lb.x 0,454 = kg
lb.ft. x 0,139 = kgm
lb.in. x 17,87 = kg/m
psi x 0,070 = kg/cm²
lb./Imp.gall x 0,100 = kg/l
lb./US.gall x 0,120 = kg/l
lb./cu.ft. x 16,21 = kg/m³
lb.ft. x 1,356 = Nm
psi x 1,379 = bar
CONVERSION UNITÉS MÉTRIQUES EN
UNITÉS ANGLO-SAXONNES
mm x 0,0394 = inch
m x 3,281 = foot
m x 1,094 = yard
km x 0,622 = Eng.miles
cm² x 0,155 = Sq.in.
m² x 10,77 = Sq.ft.
m² x 1,197 = Sq.yard
cm³ x 0,061 = Cu.in.
m³ x 0,035 = Cu.ft
m³ x 1,311 = Cu.yard
litres x 0,220 = Imp.gall.
litres x 0,264 = US gall.
litres x 1,762 = pint
litres x 0,880 = quart
l/min x 0,2642 = US.gpm
kg/l x 35,25 = oz.
kg/l x 2,203 = lb.
kgm x 7,233 = lb.ft.
kg/m x 0,056 = lb.in.
kg/cm² x 14,22 = psi
kg/ x 10,00 = lb./Imp.gal.
kg/ x 8,333 = lb./US.gal.
kg/m³ x 0,062 = lb./cu.ft.
Nm x 0,737 = lb.ft.
bar x 14,503 = psi
LD
- Quelques unités de conversions :
- Si vous ne trouvez plus de roulements en Europe, ou à des prix démentiels, vous les retrouverez à des prix ‘’ normaux’’ aux USA ; GB ; Japan ; Australie (Holden), etc.
CONVERSION UNITÉS ANGLO-SAXONNES
EN UNITÉS MÉTRIQUES
inch x 25,40 = mm
foot x 0,305 = m
yard x 0,914 = m
Eng.miles x 1,609 = km
Sq.in. x 6,452 = cm²
Sq.ft. x 0,093 = m²
Sq.yard x 0,835 m²
u.in. x 16,39 = cm³
Cu.ft. x 28,36 = m³
Cu.yard x 0,763 m³
Imp.gall. x 4,547 = litres
US gall. x 3,785 litres
pint x 0,568 litres
quart x 1,137 litres
US.gpm x 3,785 = l/min
oz. x 0,028 = kg
lb.x 0,454 = kg
lb.ft. x 0,139 = kgm
lb.in. x 17,87 = kg/m
psi x 0,070 = kg/cm²
lb./Imp.gall x 0,100 = kg/l
lb./US.gall x 0,120 = kg/l
lb./cu.ft. x 16,21 = kg/m³
lb.ft. x 1,356 = Nm
psi x 1,379 = bar
CONVERSION UNITÉS MÉTRIQUES EN
UNITÉS ANGLO-SAXONNES
mm x 0,0394 = inch
m x 3,281 = foot
m x 1,094 = yard
km x 0,622 = Eng.miles
cm² x 0,155 = Sq.in.
m² x 10,77 = Sq.ft.
m² x 1,197 = Sq.yard
cm³ x 0,061 = Cu.in.
m³ x 0,035 = Cu.ft
m³ x 1,311 = Cu.yard
litres x 0,220 = Imp.gall.
litres x 0,264 = US gall.
litres x 1,762 = pint
litres x 0,880 = quart
l/min x 0,2642 = US.gpm
kg/l x 35,25 = oz.
kg/l x 2,203 = lb.
kgm x 7,233 = lb.ft.
kg/m x 0,056 = lb.in.
kg/cm² x 14,22 = psi
kg/ x 10,00 = lb./Imp.gal.
kg/ x 8,333 = lb./US.gal.
kg/m³ x 0,062 = lb./cu.ft.
Nm x 0,737 = lb.ft.
bar x 14,503 = psi
LD
Daniel- Messages : 544
Date d'inscription : 22/04/2012
Age : 81
Localisation : Paris Ouest
Opeldel aime ce message
Page 7 sur 8 • 1, 2, 3, 4, 5, 6, 7, 8

» restauration opel ascona
» Opel Rekord Restauration.
» Restauration Ascona C.
» Bonnes années à tous
» Moteur 2.0L 16V
» Opel Rekord Restauration.
» Restauration Ascona C.
» Bonnes années à tous
» Moteur 2.0L 16V
oocb :: Partie Publique :: L'atelier
Page 7 sur 8
Permission de ce forum:
Vous ne pouvez pas répondre aux sujets dans ce forum